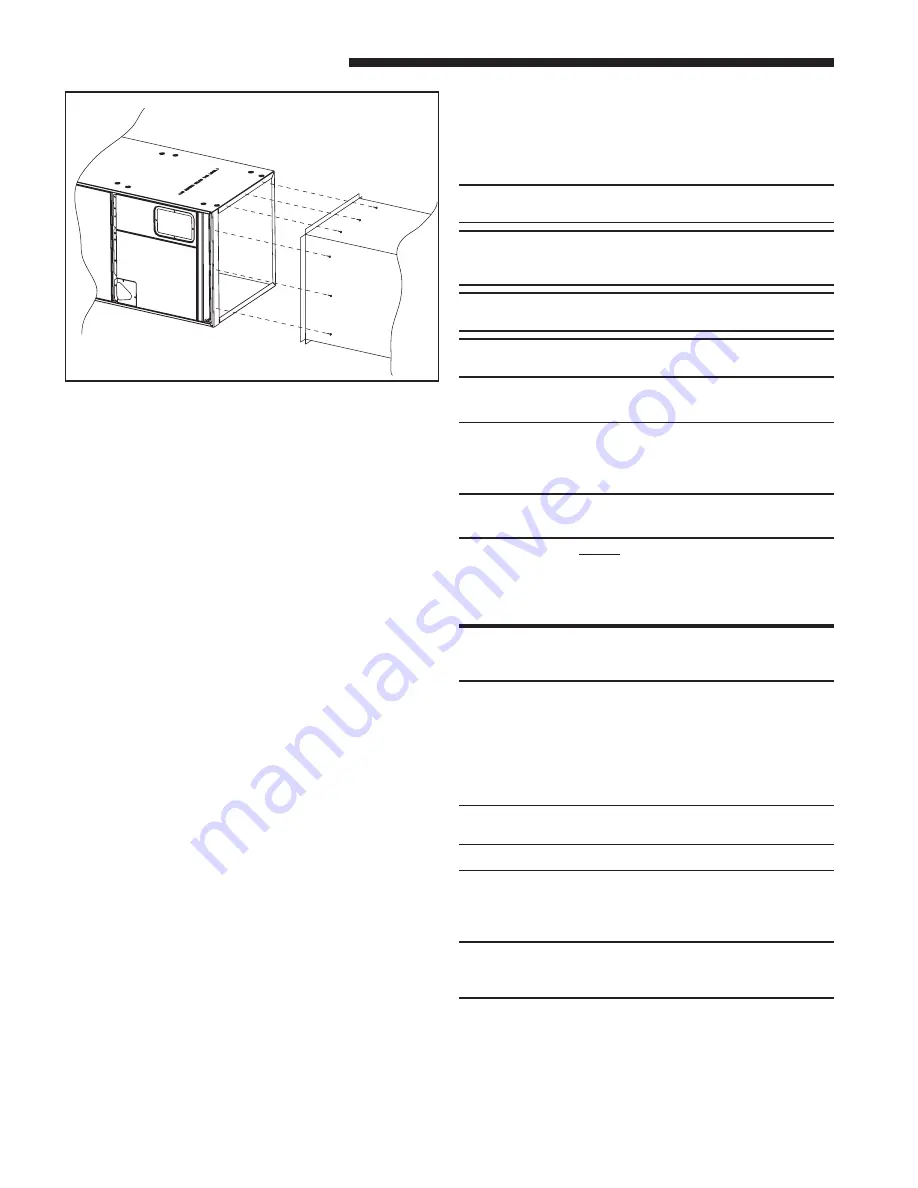
8
18-GE08D1-10
Installer’s Guide
d. If the unit is not suspended it must be isolated
carefully to prevent sound transmission. Vibra-
tion isolators (purchased locally) must be placed
under the unit.
e. It is always recommended that an auxiliary
drain pan be installed under a horizontal air
handler (See Condensate Drain Piping) to pre-
vent possible damage to ceilings.
f. Isolate the auxiliary drain pan from the unit or
from the structure.
g. Connect the auxiliary drain line to a separate
drain line (no trap is needed in this line) and
terminate according to local codes.
h. If a return duct is connected to the Air Handler,
it must be the same dimensions as the return
opening shown in the outline drawings.
i. On units with sheetmetal returns: Return ple-
num should be flanged. Sheetmetal screws must
be 1/2" in length or shorter.
j. No sheetmetal screws may be used to attach re-
turn ductwork on the side of the unit.
k.
Openings where field wiring enters the cab-
inet must be completely sealed.
Location of
power entry is shown on the outline drawing.
Use 2.5" clear stickers to seal all unused electri-
cal knockouts and cage nut openings. See Fig-
ure 11.
l. After ductwork connections are made, seal air-
tight and per local codes.
D. DUCT CONNECTIONS
The supply and return air ducts should be connected to
the unit with flame retardant duct connectors.
Convertible duct flanges are provided on the discharge
opening to provide a “flush fit” for 3/4" or 1-1/2" duct
board applications. See the Outline drawing for sizes
of the duct connections. After the duct is secured, seal
around the supply duct to prevent air leakage.
NOTE: No sheetmetal screws may be used to attach re-
turn ductwork on the side.
NOTE: On units with sheetmetal returns: Return ple-
num should be flanged. Sheetmetal screws must be
1/2" in length or shorter. See Figure 12.
NOTE: If the convertible duct flanges are not used, they
must be removed and discarded for proper airflow.
NOTE: Any duct board return connection can be made
to the sides of the unit using tape or mastic.
E. REFRIGERANT PIPING
IMPORTANT:
Refrigerant piping must be routed to maintain service ac-
cess to blower compartment and provide easy removal of
filter access panel and filter.
1. Refrigerant connections are made outside the cabi-
net.
NOTE: TXV bulb
MUST
be protected (wrap a wet rag
around the suction line between the TXV bulb and the
braze joint) or removed, while brazing the tubing. Over-
heating of the sensing bulb will affect the functional
characteristics and performance of the air handler.
NOTE: The area around refrigerant lines must be sealed
and electrical inlets need to be sealed at both the low
and the high voltage.
2. Installation of refrigerant lines is covered in the in-
stallation instructions packaged with the outdoor
unit. Evacuation, leak testing and brazing pro-
cedures are included in those instructions. Read
those instructions before starting installation of re-
frigerant lines.
NOTE: Torque specification for TXV equals 1/6 turn past
finger tight.
F. BRAZING TO EVAPORATOR
NOTE: A brazing shield is provided in the information
pack accompanying this unit. This shield fits over the
refrigerant fittings while brazing. Wet the shield before
brazing. See Figure 13.
IMPORTANT:
Do NOT unseal refrigerant tubing until ready to cut and fit
refrigerant lines.
1. Remove the sealing caps from indoor coil field con-
nections.
2. Field supplied tubing should be cut square, round
and free of burrs at the connecting end. Clean the
tubing to prevent contaminants from entering the
system.
Flange Attachment
w