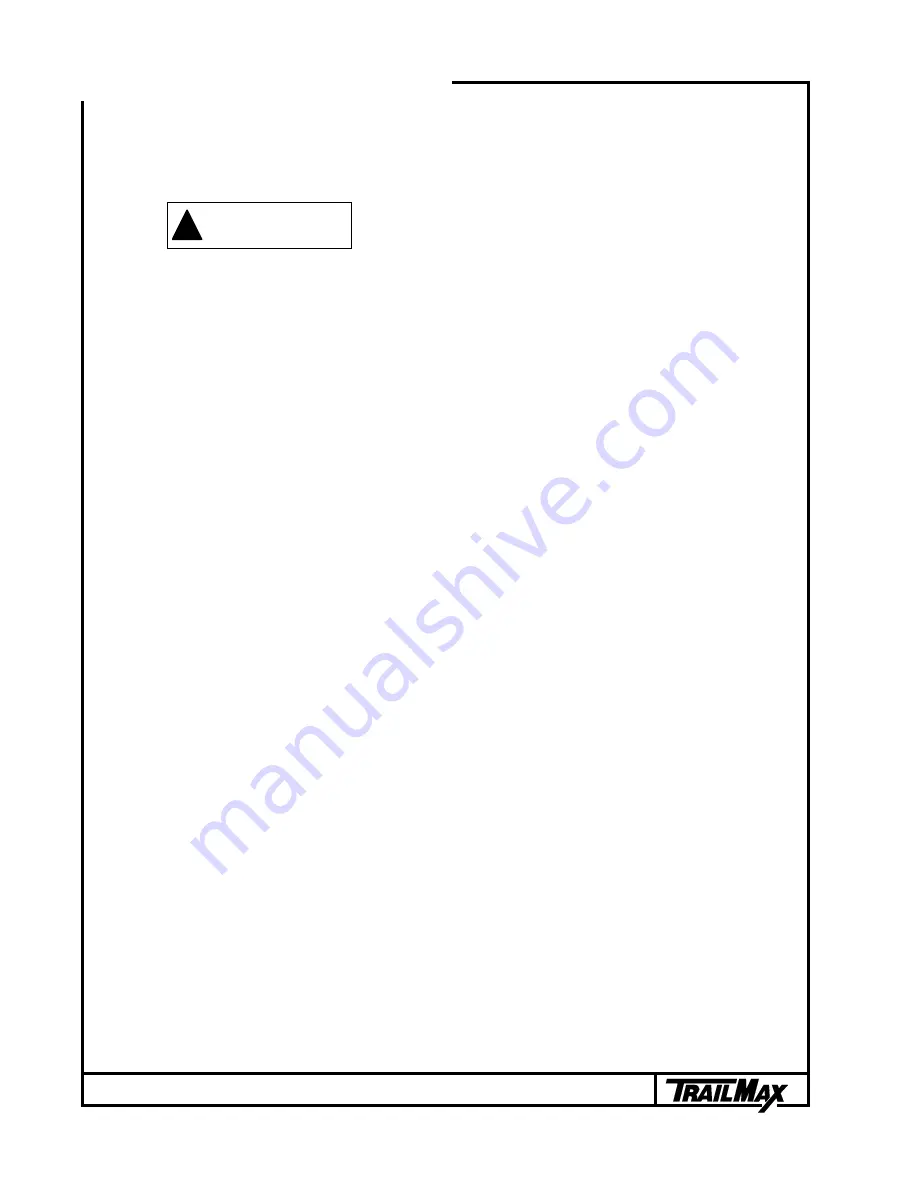
®
page 28
T-16-UT (4+16)
Maintenance
Corrosive Environment Warning
CORROSIVE ENVIRONMENTS!
Saltwater, granular fertilizers and other corrosive materials are destruc-
tive to metal. To prolong the life of a braking system used under corrosive
conditions the actuator should be flushed after use with a high pressure
water hose. Failure to properly clean the actuator could weaken it and/or
cause it to fail and result in serious injury and/or property damage.
Hydraulic Lines
Occassionally check the condition and security of the lines and hoses that comprise
the brake hydraulic system. Check that the lock tabs and clamps are in place and
securely holding the lines to the frame. Look for signs of leakage, especially if you have
had to add fluid to the reservoir frequently.
Check the tubing for kinks, cracks, blockage and corrosion, and replace any that
are questionable. Inspect the hoses for age checking (cracking of the outer rubber
sheath), damage, blisters, or other signs of impending failure and replace as neces-
sary.
Hydraulic Brakes
The hydraulic brake system incorporates a free backing solenoid which allows a surge
actuator equipped trailer to move easily in reverse. Without this feature the surge actuator
would be applying the trailer brakes as the tow vehicle is attempting to back the trailer. See
page 60 for proper wiring of electrical plug for use with free backing solenoid.
WARNING
!
Summary of Contents for T-16-UT (4+16)
Page 43: ...page 43 T 16 UT 4 16 Parts 1 2 3 5 4...
Page 51: ...page 51 T 16 UT 4 16 Parts P A R T S THIS PAGE LEFT BLANK INTENTIONALLY...
Page 53: ...page 53 T 16 UT 4 16 Parts P A R T S 1 2 3 3 3 4 5 6 7 8 10 11 12 13 14 15 9 16 17 18 19 20...
Page 55: ...page 55 T 16 UT 4 16 Parts P A R T S 1 1 2 3 4 5 6 7 8 9 10 11 12 13 14 15 16 17 18 19 20...
Page 59: ...page 59 T 16 UT 4 16 Parts P A R T S 5 4 10 9 7 2 3 2 1 8 6...
Page 63: ...page 63 T 16 UT 4 16 Parts P A R T S 3 4 1 7 8 10 2 9 5 6...