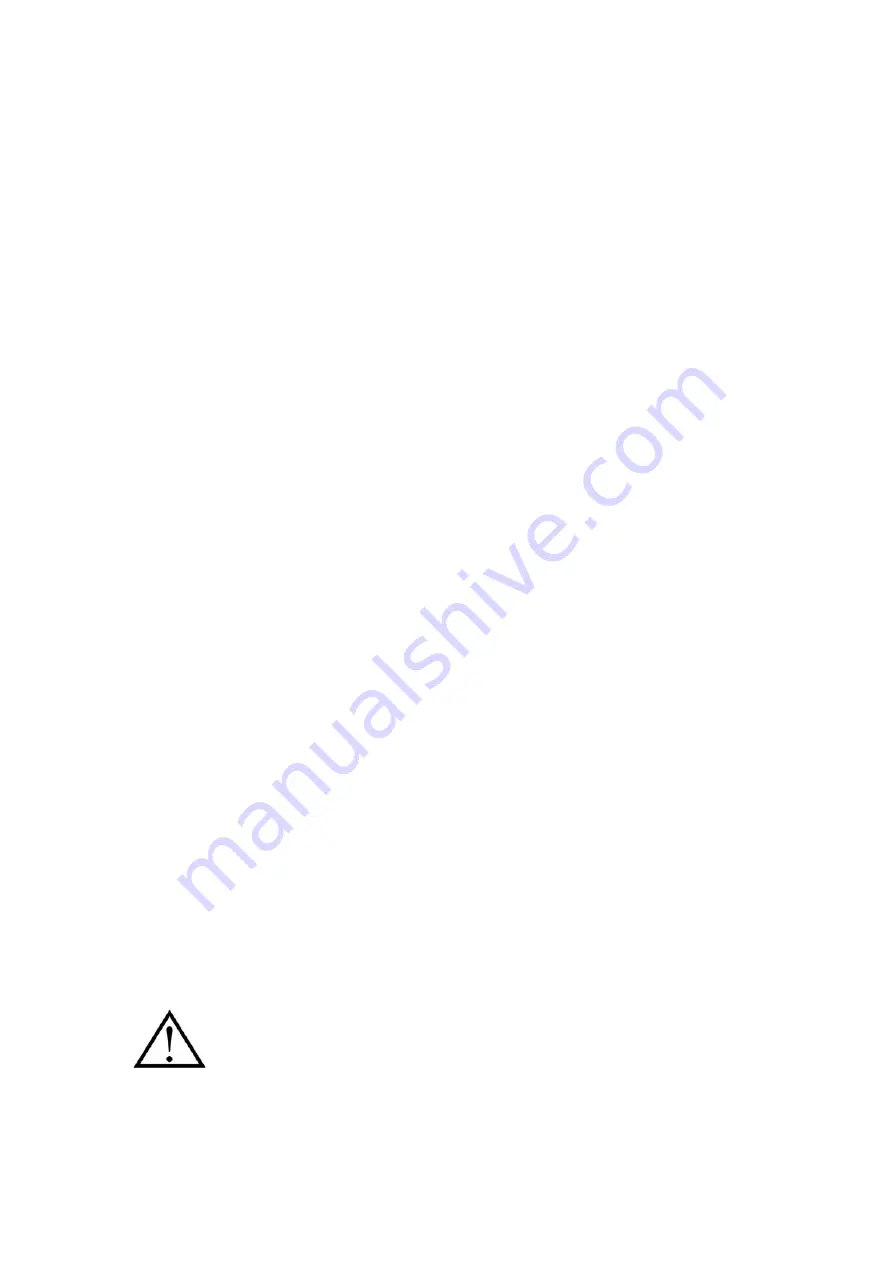
7
Operator’s Manual – BM-21 Bevelling Machine
11)
If cutting edge of insert is worn out, rotate insert in socket by 90° or, if all edges are worn out,
replace with new insert specified in Operator’s Manual.
12)
Before every use, inspect machine to ensure it is not damaged. Check whether any part is
cracked and whether all parts are properly fitted. Make sure to maintain proper conditions that
may affect machine operation.
13)
Maintain machine and tools with care. Cover steel parts with thin grease layer to protect them
against rust when not in use for a long period.
14)
After every use, remove metal chips from machine, particularly from milling head, ensuring that
power cord is unplugged from power socket.
15)
Use only parts recommended by manufacturer and specified in Operator’s Manual.
16)
Perform all maintenance work and repairs only with power cord disconnected from power socket.
17)
Replace damaged parts of machine only with genuine parts.
18)
Perform all mechanical and electrical repairs only in service centre appointed by seller.
19)
If machine falls on a hard surface, from a height, is wet or has other damage that could affect
technical state of machine, stop operation and immediately send machine to service centre for
inspection.
WARNING! Do not hold rotating parts.
Safety rules must be closely observed.