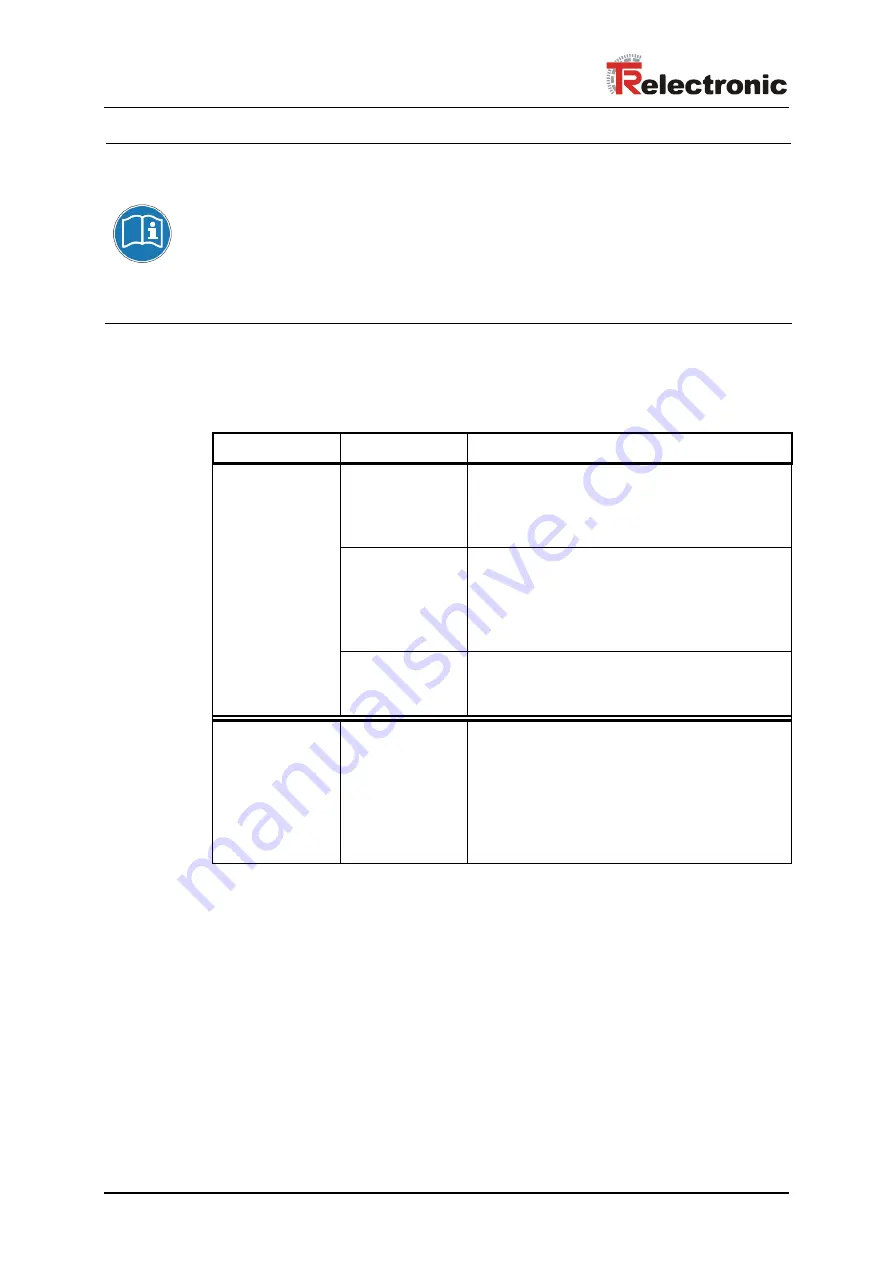
Trouble-shooting and diagnostic facilities
©
TR-Electronic GmbH 1997, All Rights Reserved
Printed in the Federal Republic of Germany
Page 44 of 45
TR - ECE - BA - GB - 0009 - 08
03/04/2010
According to the PNO encoder profile, an encoder must set the bits 'Ext.diag'
(extended diagnostic information available) and 'Stat.diag' (static error) in the
event of an internal error being detected in the station status. This means that,
in case of error, the encoder stops providing position data and is removed from
the process image by the PROFIBUS master until the error bits are reset. It is
not possible for the user to acknowledge the error via the PROFIBUS in this
way.
This function is only guaranteed provided the Commissioning Diagnostic
function is activated.
4.3 Other faults
Fault Cause
Remedy
Encoder step
changes
Strong vibrations
Vibrations, shocks and jolts, e.g. on presses, are
cushioned by so-called "shock modules". If the error
persists despite these precautions, the encoder must be
replaced.
Electrical
faults
EMC
Electrical faults can be countered by means of insulating
plastic flanges and couplings, and by data and power
supply cables with twisted-pair conductors. The screening
and wiring arrangement must conform to the assembly
guidelines for PROFIBUS.
Excessive axial and
radial loading of shaft
or scanning defect.
Couplings prevent mechanical strain on the shaft. If the
error persists despite this precaution, the encoder must be
replaced..
Profibus operates
when the encoder is
not connected, but
indicates a fault when
the bus cover is
mounted on the
encoder
PROFIBUS Data-A
and Data-B reversed
Inspect all connections and conductors relating to the
wiring of the encoder.