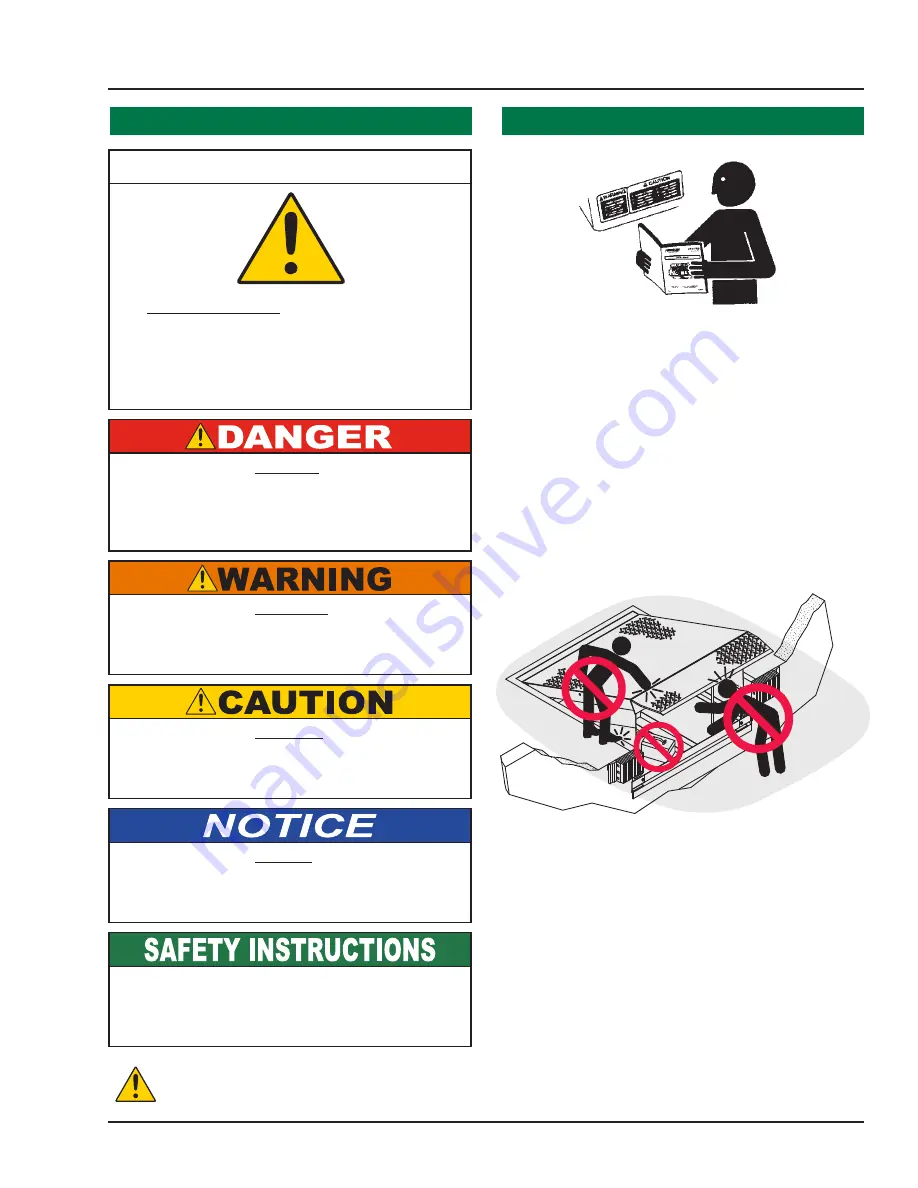
1
Read and understand the Owner’s/User’s Manual and
become thoroughly familiar with the equipment and its
controls before operating the equipment.
Never operate equipment while a safety device or
guard is removed or disconnected.
Never remove DANGER, WARNING, or CAUTION
signs, Placards or Decals on the equipment unless
replacing them.
4111-0072 — Dec. 2018
© 2018 Systems, LLC
General Operational Precautions
Op
era
ting
Zon
e
Ope
rati
ng
Zo
ne
Figure 1
Recognize Precautionary Information
PRECAUTIONS
WARNING:
This product can expose you to chemicals including lead, which are known to the State of California to
cause cancer or birth defects or other reproductive harm. For more information go to www.P65Warnings.ca.gov
Safety-Alert Symbol
The Safety-Alert Symbol is a graphic representation
intended to convey a safety message without the
use of words. When you see this symbol, be alert
to the possibility of death or serious injury. Follow
the instructions in the safety message panel.
The use of the word DANGER signifies the
presence of an extreme hazard or unsafe practice
which will most likely result in death or severe
injury.
The use of the word WARNING signifies the
presence of a serious hazard or unsafe practice
which could result in death or serious injury.
The use of the word CAUTION signifies possible
hazard or unsafe practice which could result in
minor or moderate injury.
The use of the word NOTICE indicates information
considered important, but not hazard-related, to
prevent machine or property damage.
Indicates a type of safety sign, or separate panel on
a safety sign, where safety-related instructions or
procedures are described.
Do not start the equipment until all unauthorized
personnel in the area have been warned and have
moved outside the operating zone (Figure 1).
Remove any tools or foreign objects from the
operating zone before starting.
Keep the operating zone free of obstacles that could
cause a person to trip or fall.