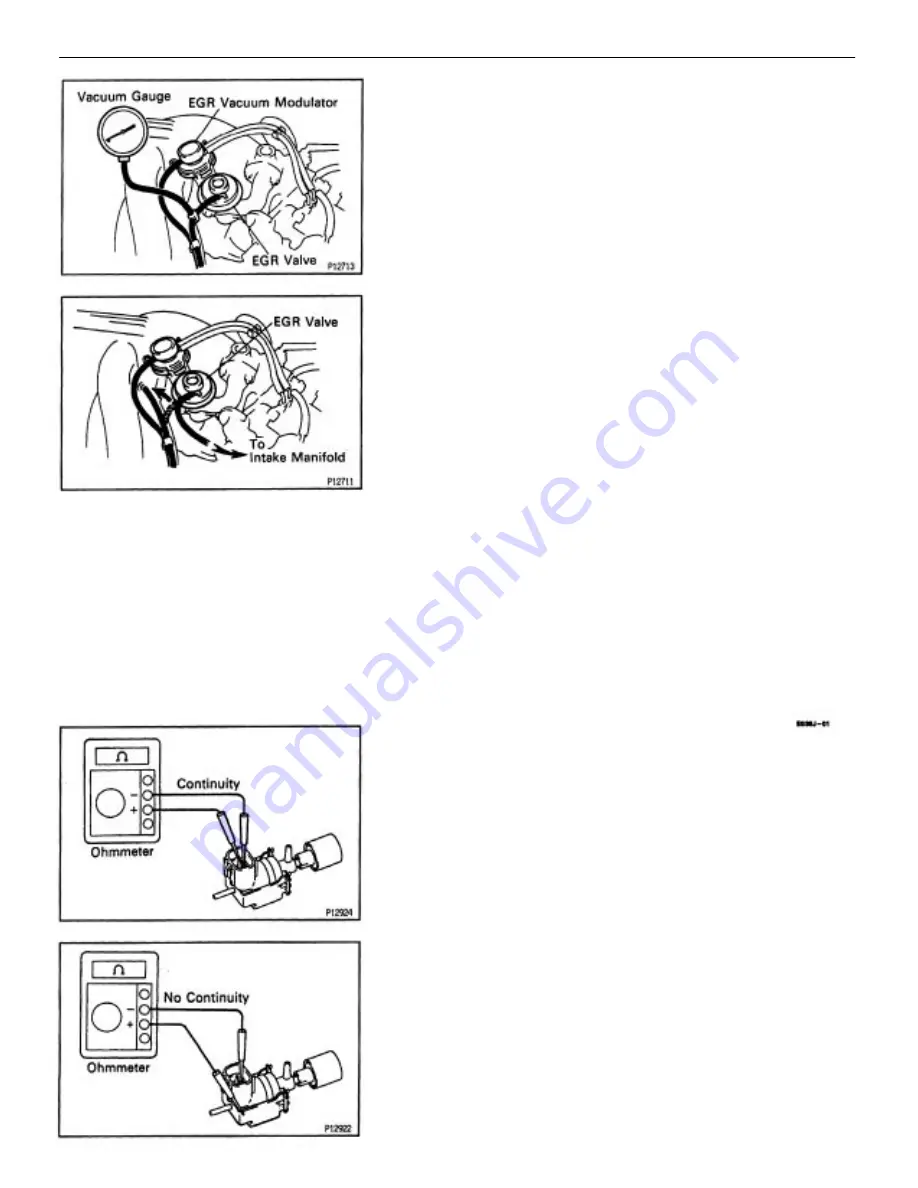
VSV INSPECTION
1. REMOVE VSV
2. INSPECT VSV
A. Inspect VSV for open circuit
Using an ohmmeter, check that there is continuity
between the terminals.
Resistance:
33 – 39
at 20
C (68
F)
If there is no continuity, replace the VSV.
B. Inspect VSV for ground
Using an ohmmeter, check that there is no continuity
between each terminal and the body.
!f there is continuity, replace the VSV.
(c) Reconnect the vacuum hoses to their proper loca–
tions.
IF NO PROBLEM IS FOUND DURING THIS
INSPECTION, SYSTEM IS NORMAL; OTHERWISE
INSPECT EACH PART
9. INSPECT EGR VALVE
(a) Apply vacuum directly to the EGR valve with the
engine idle.
(b) Check that the engine runs rough or dies.
8. REMOVE VACUUM GAUGE
Remove the vacuum gauge, and reconnect the
vacuum hoses to their proper locations.
–
1MZ–FE ENGINE
EMISSION CONTROL SYSTEMS
EG2–209
Summary of Contents for 1 MZ-FE
Page 1: ...1MZ FE ENGINE 1MZ FE ENGINE EG2 1 ...
Page 22: ...Adjusting Shim Selection Chart Intake 1MZ FE ENGINE ENGINE MECHANICAL EG2 22 ...
Page 23: ...Adjusting Shim Selection Chart Exhaust 1MZ FE ENGINE ENGINE MECHANICAL EG2 23 ...
Page 39: ...TIMING BELT COMPONENTS FOR REMOVAL AND INSTALLATION 1MZ FE ENGINE ENGINE MECHANICAL EG2 39 ...
Page 40: ... 1MZ FE ENGINE ENGINE MECHANICAL EG2 40 ...
Page 57: ...CYLINDER HEAD COMPONENTS FOR REMOVAL AND INSTALLATION 1MZ FE ENGINE ENGINE MECHANICAL EG2 57 ...
Page 58: ... 1MZ FE ENGINE ENGINE MECHANICAL EG2 58 ...
Page 59: ... 1MZ FE ENGINE ENGINE MECHANICAL EG2 59 ...
Page 60: ... 1MZ FE ENGINE ENGINE MECHANICAL EG2 60 ...
Page 61: ... 1MZ FE ENGINE ENGINE MECHANICAL EG2 61 ...
Page 122: ... 1MZ FE ENGINE ENGINE MECHANICAL EG2 122 ...
Page 123: ... 1MZ FE ENGINE ENGINE MECHANICAL EG2 123 ...
Page 135: ...COMPONENTS FOR PREPARATION AND AFTER ASSEMBLY 1MZ FE ENGINE ENGINE MECHANICAL EG2 135 ...
Page 189: ...EXHAUST SYSTEM COMPONENTS 1MZ FE ENGINE ENGINE MECHANICAL EG2 189 ...
Page 197: ...COMPONENT LAYOUT 1MZ FE ENGINE EMISSION CONTROL SYSTEMS EG2 197 ...
Page 198: ...SCHEMATIC DRAWING 1MZ FE ENGINE EMISSION CONTROL SYSTEMS EG2 198 ...
Page 217: ...SFI SYSTEM DESCRIPTION 1MZ FE ENGINE SFI SYSTEM EG2 217 ...
Page 219: ...SYSTEM CIRCUIT 1MZ FE ENGINE SFI SYSTEM EG2 219 ...
Page 245: ...COMPONENTS FOR REMOVAL AND INSTALLATION 1MZ FE ENGINE SFI SYSTEM EG2 245 ...
Page 258: ...FUEL TANK AND LINE COMPONENTS 1MZ FE ENGINE SFI SYSTEM EG2 258 ...
Page 284: ...COMPONENTS FOR REMOVAL AND INSTALLATION 1MZ FE ENGINE SFI SYSTEM EG2 284 ...
Page 288: ...COMPONENTS FOR REMOVAL AND INSTALLATION 1MZ FE ENGINE SFI SYSTEM EG2 288 ...
Page 290: ...1MZ FE ENGINE Memo ...
Page 292: ...COMPONENTS FOR REMOVAL AND INSTALLATION 1MZ FE ENGINE SFI SYSTEM EG2 292 ...
Page 299: ...KNOCK SENSOR COMPONENTS FOR REMOVAL AND INSTALLATION 1MZ FE ENGINE SFI SYSTEM EG2 299 ...
Page 309: ...1MZ FE ENGINE Memo ...
Page 320: ...WATER PUMP COMPONENTS FOR REMOVAL AND INSTALLATION 1MZ FE ENGINE COOLING SYSTEM EG2 320 ...
Page 321: ... 1MZ FE ENGINE COOLING SYSTEM EG2 321 ...
Page 335: ...COMPONENTS FOR REMOVAL AND INSTALLATION 1MZ FE ENGINE COOLING SYSTEM EG2 335 ...
Page 351: ...Hydraulic Motor COMPONENTS FOR REMOVAL AND INSTALLATION 1MZ FE ENGINE COOLING SYSTEM EG2 351 ...
Page 374: ...OIL PUMP COMPONENTS FOR REMOVAL AND INSTALLATION 1MZ FE ENGINE LUBRICATION SYSTEM EG2 374 ...
Page 375: ... 1MZ FE ENGINE LUBRICATION SYSTEM EG2 375 ...
Page 376: ... 1MZ FE ENGINE LUBRICATION SYSTEM EG2 376 ...
Page 394: ...1MZ FE ENGINE TROUBLESHOOTING 1MZ FE ENGINE EG2 394 ...
Page 395: ... 1MZ FE ENGINE EG2 395 ...
Page 423: ...PARTS LOCATION 1MZ FE ENGINE PARTS LOCATION EG2 423 ...
Page 424: ...WIRING DIAGRAM 1MZ FE ENGINE WIRING DIAGRAM EG2 424 ...
Page 425: ... 1MZ FE ENGINE WIRING DIAGRAM EG2 425 ...
Page 429: ... MEMO 1MZ FE ENGINE EG2 429 ...
Page 442: ...Location of Connectors in Body 1MZ FE ENGINE LOCATION OF CONNECTORS EG2 442 ...
Page 443: ...Fuel Pump Wagon 1MZ FE ENGINE LOCATION OF CONNECTORS EG2 443 ...
Page 452: ...WIRING DIAGRAM 1MZ FE ENGINE CIRCUIT INSPECTION EG2 452 ...
Page 464: ...WIRING DIAGRAM 1MZ FE ENGINE CIRCUIT INSPECTION EG2 464 ...
Page 494: ...WIRING DIAGRAM 1MZ FE ENGINE CIRCUIT INSPECTION EG2 494 ...
Page 518: ...WIRING DIAGRAM 1MZ FE ENGINE CIRCUIT INSPECTION EG2 518 ...
Page 576: ...WIRING DIAGRAM 1MZ FE ENGINE CIRCUIT INSPECTION EG2 576 ...