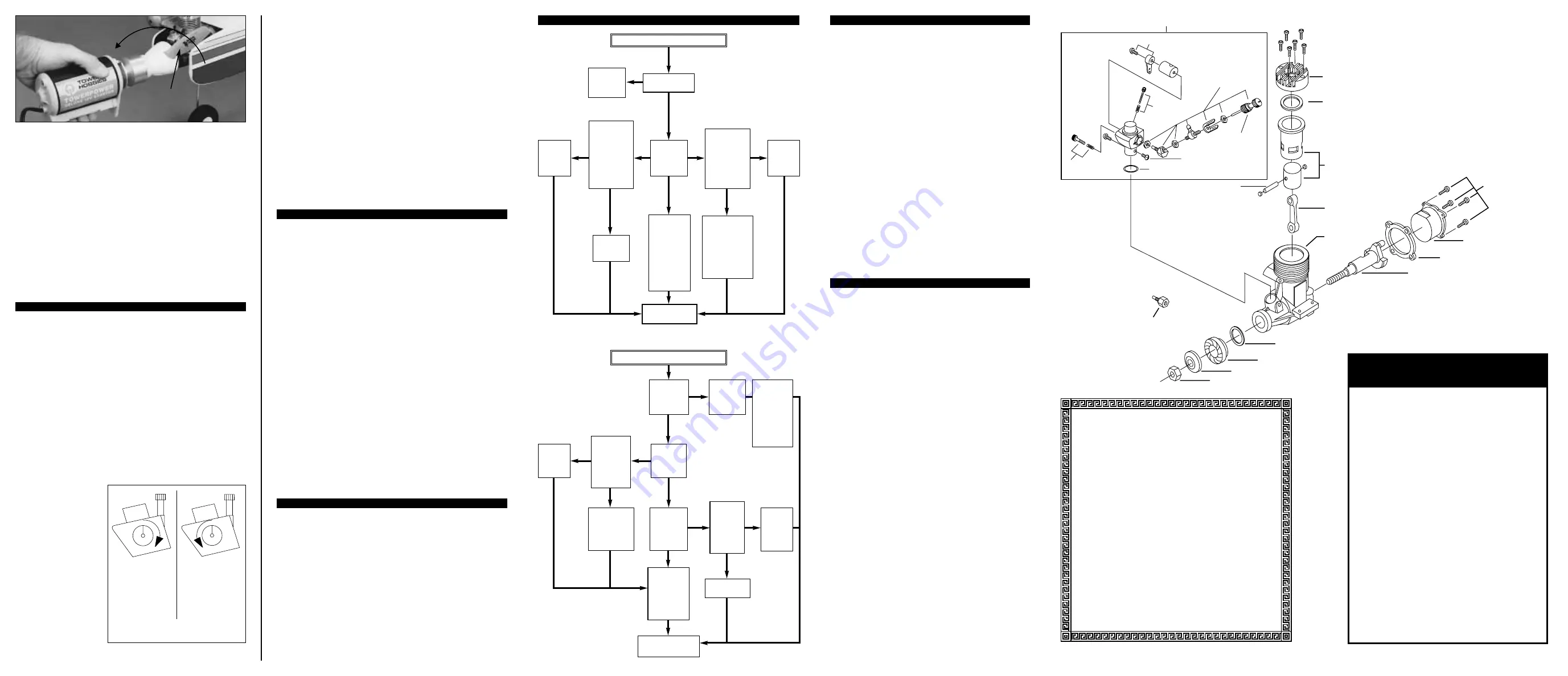
If using an electric starter to start the engine, make sure the starter is turning
counterclockwise. If your engine has a spinner on it, place the large opening of the
rubber adapter on your starter against the spinner. Turn the starter on and hold it
against the spinner until the engine starts. Because the engine is new, it may be tight.
You may need to turn the starter on first and bump the spinner with the rubber adapter
to get it started the first few times. If only a propeller nut is on the front of the propeller,
turn the rubber adapter on the starter around and center the small hole of the rubber
adapter over the nut. Turn the starter on and hold it against the propeller until the
engine starts. If the starter has difficulties turning the engine, the engine may be
flooded with fuel. Clear the engine of fuel as described above.
Do not
continue to try to
start a flooded engine. The connecting rod in the engine could be damaged.
10.
After the engine starts allow it to warm up for 15-30 seconds before removing the
glow plug clip. Do not reach around the spinning propeller to remove it, as this is how
many accidents happen. Instead, reposition yourself behind the propeller before
removing the glow plug clip or adjusting the needle valve.
Engine “Break-in”
Have an assistant hold the airplane securely. Start engine and advance to full throttle.
Slowly, by turning “clockwise,” lean the needle valve. As you do this, you will hear the
engine pick up speed, with the exhaust sound becoming higher in pitch. At the same
time, you will also hear that the engine will start running smoother. At some point, the
sound of the exhaust will start trying to change from a low pitch to a higher pitch
sound. It will alternate back and forth as you adjust the needle. Continue to slowly lean
the needle valve.
Eventually, the engine will be running mainly at the higher-pitch sound with an
occasional misfire or momentary change to the lower-pitch sound. “Richen” the needle
5-6 clicks from this point, and allow the engine to run at this setting for at least five
minutes.
If, at some time during the break-in process, the engine runs the tank out of fuel, don’t
change the needle valve setting. Just refill the fuel tank, set the throttle at 1/4 open,
connect the glow plug clip, and start the engine. Since it’s been running, it should start
easily. If it doesn’t start right away, remove the glow plug clip, and prime the engine as
described above. Once you’ve restarted the engine, advance the throttle to full and
continue the process.
After five minutes, give the fuel
line a quick pinch. You should
hear the engine increase speed
then return to normal. If, when
you pinch the fuel line, the
engine does not change speed,
or if it slows down, immediately
richen the needle valve at least
1/4 turn. Try pinching the fuel
line again.The engine MUST
increase speed when the fuel
line is pinched.
If, when you pinch the fuel line,
you do get an increase in engine
speed, repeat the pinch five
times at 30-second intervals, but
do not adjust the needle valve
between pinches.
Now lean the needle valve about 1/8 turn (clockwise). The engine should increase
speed slightly. Allow the engine to run at this setting for a minute or two and then
repeat the pinching process like before (five pinches at 30-second intervals). Did the
engine jump in speed? If so, then lean the needle another 1/8 turn (clockwise).
Continue this process until a quick pinch will result in no change in engine speed.
If, at any point, the engine starts to slow down while you are leaning the needle valve,
or when you pinch the fuel line, immediately stop and turn the needle valve back at
least 1/4 turn (counterclockwise). This means that you have turned the needle valve
too far. If this happens when you first start adjusting the needle valve, run the engine
longer at the first setting, it hasn’t run long enough to accept the new setting.
Eventually, you will get to the point where a quick pinch will not cause the engine to
speed up. You will either hear no change, or the engine will slow down a bit. Richen
the needle valve so that you can hear the engine speed up when you give the fuel line
a pinch. Allow the engine to run at this setting for a full tank of fuel.
While the engine is running at this setting, pinch the fuel line occasionally to make sure
you get a speed increase. As the fuel level in the tank lowers, most engines will tend to
lean a bit, so make sure the needle valve setting allows for this. If the engine will run at
this setting for an entire tank of fuel, it’s time to set the idle speed and mixture.
Adjusting the Idle
Slowly close the throttle. The engine will begin to slow down. You will also hear it start
to misfire and run a bit rough. This is normal. The carburetor opening should be about
1/16” open when the engine is idling.
If the engine will not idle smoothly, or tries to stop, the air-bleed screw will need to be
adjusted. With the engine running, close the throttle to a point just short of where the
engine stops. Pinch the fuel line. If the engine speeds up a bit, the mixture is rich.
Stop the engine and turn the air-bleed screw counterclockwise 1/4 turn. Restart the
engine and repeat the process until no change occurs. Note that the airbleed screw is
adjusted exactly in reverse of the needle valve (for the airbleed screw, “in” (turning
clockwise) is rich, and “out” (turning counterclockwise) is lean).
If the engine slows down when you pinch the fuel line, the mixture is lean. Richen the
airbleed screw 1/4 turn clockwise. Repeat the process until you get no change in
engine speed when you pinch the fuel line.
Since the engine is running slowly, a very quick pinch may not have much effect. You
may have to pinch the fuel line for a few seconds. Don’t pinch off the fuel line long
enough to stop the engine.
Another way to check your idle setting is to throttle down the engine and then let it idle.
If it gradually slows down and then quits, lean the airbleed screw. If it speeds up just
before it quits, richen the airbleed screw.
Once you have the air bleed screw adjusted and the engine idles smoothly, move the
throttle from idle to full speed. There may be a slight hesitation as the throttle is
advanced, but this is normal. The engine should not be sluggish going from idle to full
speed. There should also be a smooth transition when the throttle is reduced from full
speed to idle. The engine should be idling the same as in the beginning of this step.
Your engine is now ready to fly.
Stopping and Restarting the Engine:
To stop the engine before it runs out of fuel, we suggest that the radio be set up so
that when the throttle and throttle trim are moved to the low-speed position, the
carburetor can be completely closed. If your throttle was not set up this way, pinch the
fuel line from the fuel tank to the carburetor to stop the engine.
Restarting the Engine:
If the engine is still warm, try to start the engine without priming it first. If the engine
has cooled down it may need to be primed.
If the engine does not start after priming, the engine may be flooded. Clear the excess
fuel from the engine as described before. Attach the glow plug clip to the glow plug
and check that it glows bright orange. If it does, re-install it in the engine. If it does not,
replace the glow plug with a new one. Try to restart the engine without priming it.
Turn with
electric starter
Rotate the
needle valve
counter
clockwise to
"richen" the
engine
Rotate the
needle valve
clockwise to
"lean" the
engine
Do
not
adjust screws while engine is running
Care and Maintenance:
• We suggest that a fuel filter be installed between the carburetor and the
fuel tank to prevent dirt from entering the carburetor.
• At the end of a day of flying, remove all the fuel from the fuel tank. Start
the engine and allow it to run at idle until it stops. This will remove any
fuel left inside of the crankcase.
• Put a few drops of a quality “after-run oil” in the carburetor. Flip the
propeller a few times to distribute the oil throughout the engine. This will
prevent rust and corrosion from damaging the engine.
• Wipe off the outside of the engine with denatured alcohol to remove any
fuel residue and dirt. If the residue is left on the engine, the heat from
the engine will bake it on the next time it is run. Baked on residue
reduces the cooling of the engine.
• Do not disassemble the engine unless you are a qualified to do so.
• Avoid running the engine in dusty conditions. If the area you fly in is
dusty, such as a dirt runway, we suggest installing an air filter made for
airplane engines.
• After flying, check all engine mounting bolts, muffler screws, propeller
nut and spinner to make sure they have not loosened up.
Safety Precautions and Warnings
1.
Keep all spectators at least 20 feet away when operating engine.
2.
Keep yourself out of the path of the prop. Do not lean over the propeller
when starting or adjusting the engine.
3.
We recommend wood propellers only. All plastic or fiberglass props
require special handling. Follow instructions of the propeller manufacturers.
4.
Always balance the propeller before installing it on the engine. Never use
a propeller that is damaged, no matter how slight.
5.
Make sure the edges of the spinner do not touch the propeller blades.
The sharp edges may cut into the propeller blades and cause them to
break.
6.
Be sure your glow plug cord will not interfere with the propeller when
running.
7.
Never use your fingers to start the engine. Always use a chicken stick or
electric starter.
8.
Make all engine adjustments from behind the propeller. Always stop the
engine before adjusting idle stop screw or air bleed screw.
9.
Do not operate the engine in an area with loose gravel or sand.
10.
Wear safety glasses when starting and running the engine.
11.
Keep all loose clothing such as neck ties and shirt sleeves away from
the propeller. Remove any objects from your shirt pockets to prevent them
from falling into the propeller.
12.
Keep all engine fuel away from children, sparks and excessive heat.
Do not smoke while handling model fuel. Model fuel is highly flammable
and must be handled with caution.
13.
Never operate the model engine in an enclosed area. The engine
produces deadly carbon monoxide and must be run in a well ventilated
area.
14.
Model engines get very hot when running. Do not touch any part of the
engine until it cools.
TOWG4100 (Carburetor Assembly)
TOWG4650
TOWG4450
TOWG4290
TOWG4370
TOWG4410
TOWG4650
TOWG4570
TOWG5340
TOWG5030
TOWG5070
TOWG4330
TOWG5160(4 pcs.)
TOWG5160 (6 pcs.)
TOWG5260
(OPTIONAL STRAIGHT
SPRAY BAR ADAPTER)
TOWG4220
TOWG4220
TOWG4650
TOWG5160 (2 PCS)
TOWG4880
TOWG5220
TOWG5400
TOWG4490
TOWG5300
Does it run
continuously?
It should
be ready
to go.
NO
NO
YES
YES
YES
YES
NO
YES
NO
NO
NO
YES
YES
YES
NO
YES
NO
NO
YES
The engine starts
Is fuel
getting to
the
engine?
Check for
clogging in
the
carburetor
or fuel line
and check
needle
valve
setting.
Is the
needle
valve
setting 2-
1/2 to 3
turns out
from
closed?
Try starting the
engine again.
Does the
engine quit
when the
glow plug
clip is
removed?
The
engine
may be
flooded.
Reset the
needle
valve.
Replace
the glow
plug.
Check that
the pressure
line is
connected to
the muffler.
The fuel may
be bad.
Does the
engine
turn over
easily?
Is fuel in
the fuel
line?
Is the
glow plug
red hot?
Remove
to check.
Check the
needle
valve
setting and
prime the
engine.
Is foreign
matter
clogging
the fuel
tank or
fuel line?
Is the
battery
for the
glow
plug clip
charged?
The engine does not start
The
engine
may be
flooded.
Check
needle
valve
setting.
Remove the
obstruction
from the fuel
tank or fuel
line.
Charge
or
replace
the
batteries
Replace the
glow plug.
Try starting the
engine again.
Trouble Shooting:
Limited Warranty:
Your engine is warrantied to be free of defects in parts and workmanship
for a period of 2 years from the date of purchase when returned for service
accompanied by your proof of purchase. Crash damage and problems
caused by neglect, abuse or over-leaning will not be covered under
warranty. Damage caused by customer disassembly, tampering, use of
substandard fuel, use of incorrect accessories (glow plug, propeller, etc.),
or any use of the engine for which it is not specifically intended will
automatically void the warranty of the engine. Should your engine require
warranty or non-warranty service, please return it via an insured shipper to
our national servicing facility.
Hobby Services
P.O. Box 9021
1610 Interstate Dr.
Champaign, IL 61821
Ph. (217) 398-0007
9:00
A
.
M
. to 5:00
P
.
M
. Central time. Monday through Friday
Along with your engine and proof of purchase date, please enclose a
complete written explanation detailing the problems. State your name and
address clearly. For repairs not covered under warranty, you must specify
whether you wish the charges to be billed C.O.D. or if you wish to be
notified of the charges so you can send a check. VISA and MasterCard are
also accepted
May need
to remove
glow plug
and turn
over
engine,
also clean
glow plug.
Ordering Parts is Easy —
Just Call Tower Hobbies Toll Free at
1-800-637-6050
STOCK #
DESCRIPTION
TOWG4100. . . . . . CARBURETOR ASSEMBLY
TOWG4220. . . . . . CARBURETOR SCREWS IDLE AND STOP
TOWG4290. . . . . . CONNECTING ROD
TOWG4330. . . . . . COVER PLATE
TOWG4370. . . . . . CRANKCASE
TOWG4410. . . . . . CRANKSHAFT
TOWG4450. . . . . . CYLINDER LINER AND PISTON
TOWG4490. . . . . . CYLINDER HEAD
TOWG4570. . . . . . DRIVE WASHER
TOWG4650. . . . . . GASKET SET (3)
TOWG4720. . . . . . MUFFLER ASSEMBLY
TOWG4760. . . . . . MUFFLER ASSEMBLY SCREW
TOWG4840. . . . . . MUFFLER MOUNTING SCREWS
TOWG4880. . . . . . NEEDLE VALVE
TOWG4990. . . . . . PRESSURE TAP
TOWG5030. . . . . . PROPELLER NUT
TOWG5070. . . . . . PROPELLER WASHER
TOWG5160. . . . . . SCREW SET (12)
TOWG5220. . . . . . SPRAYBAR ASSEMBLY-ANGLED
TOWG5260. . . . . . SPRAYBAR ADAPTER-STRAIGHT
TOWG5300. . . . . . THROTTLE ARM AND SCREW
TOWG5340. . . . . . THRUST WASHER
TOWG5400. . . . . . WRIST PIN WITH RETAINERS