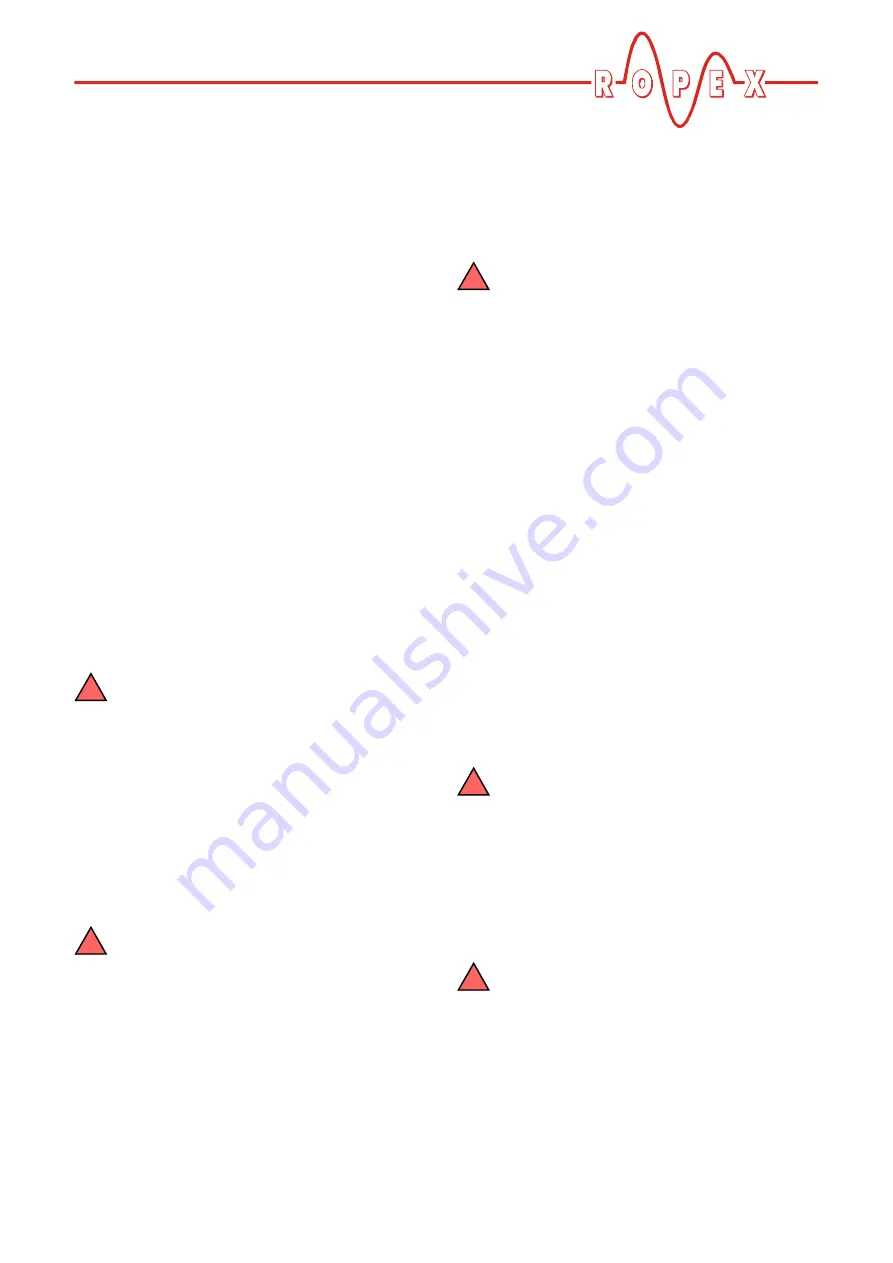
Safety and warning notes
RES-403
Page 3
1
Safety and warning notes
This RESISTRON temperature controller is
manufactured according to DIN EN 61010-1. In the
course of its manufacture it passed through quality
assurance, whereby it was subjected to extensive
inspections and tests.
It left the factory in perfect condition.
The recommendations and warning notes contained in
these operating instructions must be complied with, in
order to guarantee safe operation.
The device can be operated within the limits indicated
in the "Technical Data" without impairing its operational
safety. Installation and maintenance may only be
performed by technically trained, skilled persons who
are familiar with the associated risks and warranty
provisions.
1.1
Use
RESISTRON temperature controllers may only be used
for heating and temperature control of heatsealing
bands which are expressly suitable for them, and
providing the regulations, notes and warnings
contained in these instructions are complied with.
In case of non-compliance or use contrary to
the intended purpose, there is a risk that
safety will be impaired or that the heatsealing band,
electrical wiring, transformer etc. will overheat.
Ensuring such compliance is the personal
responsibility of the user.
1.2
Heatsealing band
A basic prerequisite for reliable and safe operation of
the system is the use of suitable heatsealing bands.
The resistance of the heatsealing band which
is used must have a positive minimum
temperature coefficient in order to guarantee
trouble-free operation of the RESISTRON
temperature controller.
The temperature coefficient must be specified as
follows:
e.g.
Alloy-20:
TCR = 1100 ppm/K
NOREX:
TCR = 3500 ppm/K
The RESISTRON temperature controller must be set
and coded according to the temperature coefficient of
the heatsealing band.
The use of incorrect alloys with a too low
temperature coefficient and incorrect coding
of the RESISTRON temperature controller lead to
uncontrolled heating and ultimately to burn-out of
the heatsealing band!
The heatsealing bands that were originally supplied
must be identified by detail specification, part number
or some other means that will assure that replacement
bands are identical.
1.3
Impulse transformer
A suitable impulse transformer is necessary to ensure
that the control loop functions perfectly. This
transformer must be designed according to VDE 0570/
EN 61558 (isolating transformer with reinforced
insulation) and have a one section bobin. When the
impulse transformer is installed, suitable shock
protection must be provided in accordance with the
national installation regulations for electrical
equipment. In addition, water, cleaning solutions and
conductive fluids must be prevented from seeping into
the transformer.
Incorrect installation of the impulse
transformer impairs electrical safety.
1.4
Current transformer PEX-W2/-W3
The current transformer supplied with the RESISTRON
temperature controller is an integral part of the control
system.
Only the original ROPEX PEX-W2 or PEX-W3
current transformer may be used. Other
transformers may cause the equipment to
malfunction.
The current transformer may only be operated if it is
connected to the RESISTRON temperature controller
correctly (see section 9, "Startup and operation"). The
relevant safety instructions contained in section 8.3,
"Power supply", must be obeyed. External monitoring
modules can be used in order to additionally increase
!
!
TCR
10
4
–
×
10 K
1
–
≥
!
!
!