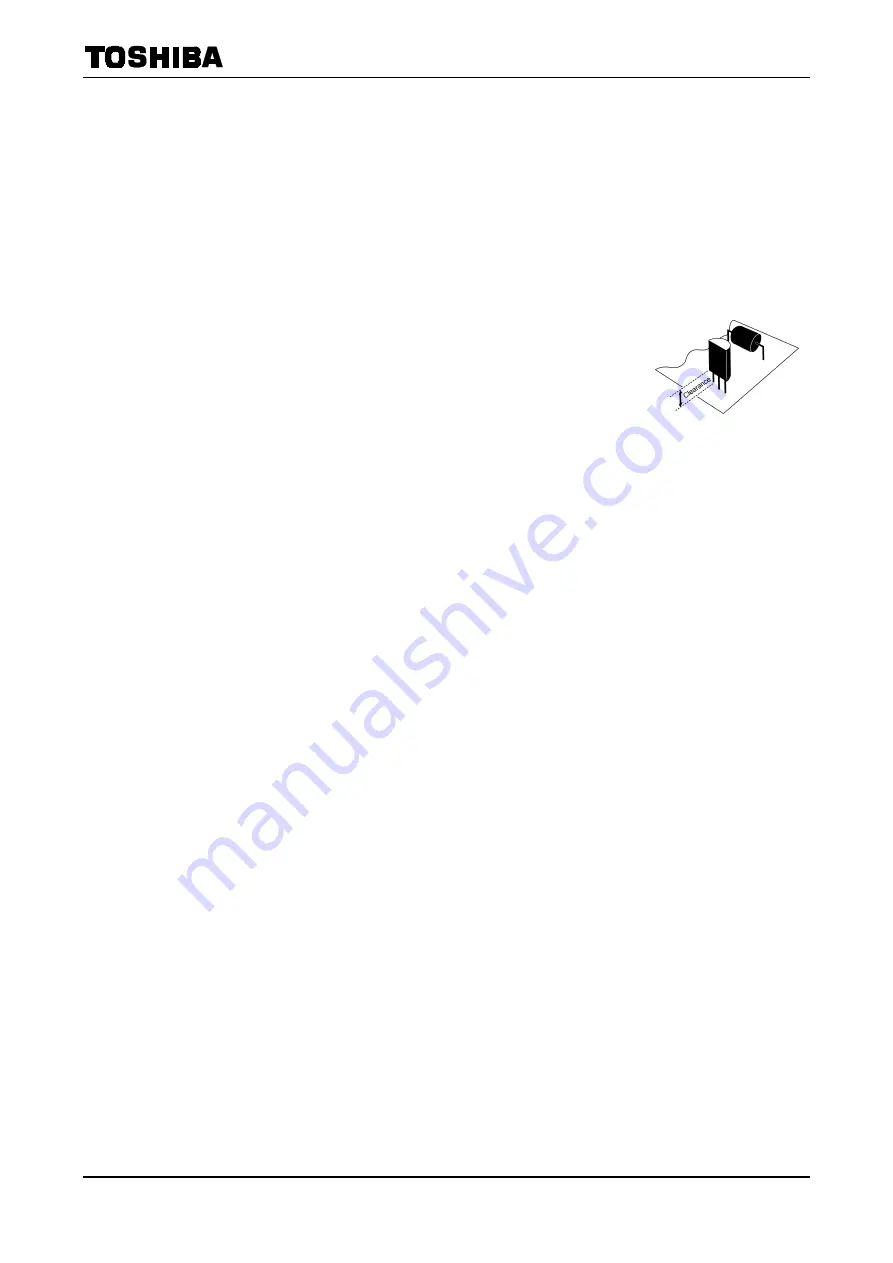
[6] Handling Guide
111
on the internal leads. If the relative difference is great enough, the device’s internal leads, adhesive
properties or sealant can be damaged. Observe these precautions during the lead-forming process
(this does not apply to surface-mount devices):
(1) Lead insertion hole intervals on the printed circuit board should match the lead pitch of the
device precisely.
(2) If lead insertion hole intervals on the printed circuit board do not precisely match the lead pitch
of the device, do not attempt to forcibly insert devices by pressing on them or by pulling on their
leads.
(3) For the minimum clearance specification between a device and a
printed circuit board, refer to the relevant device’s datasheet and
databook. If necessary, achieve the required clearance by forming the
device’s leads appropriately. Do not use the spacers which are used to
raise devices above the surface of the printed circuit board during
soldering to achieve clearance. These spacers normally continue to
expand due to heat, even after the solder has begun to solidify; this applies severe stress to the
device.
(4) Observe the following precautions when forming the leads of a device prior to mounting.
•
Use a tool or jig to secure the lead at its base (where the lead meets the device package)
while bending so as to avoid mechanical stress to the device. Also avoid bending or
stretching device leads repeatedly.
•
Be careful not to damage the lead during lead forming.
•
Follow any other precautions described in the individual datasheets and databooks for each
device and package type.
3.5.2 Socket
Mounting
(1) When socket mounting devices on a printed circuit board, use sockets which match the inserted
device’s package.
(2) Use sockets whose contacts have the appropriate contact pressure. If the contact pressure is
insufficient, the socket may not make a perfect contact when the device is repeatedly inserted and
removed; if the pressure is excessively high, the device leads may be bent or damaged when they
are inserted into or removed from the socket.
(3) When soldering sockets to the printed circuit board, use sockets whose construction prevents flux
from penetrating into the contacts or which allows flux to be completely cleaned off.
(4) Make sure the coating agent applied to the printed circuit board for moisture-proofing purposes
does not stick to the socket contacts.
(5) If the device leads are severely bent by a socket as it is inserted or removed and you wish to
repair the leads so as to continue using the device, make sure that this lead correction is only
performed once. Do not use devices whose leads have been corrected more than once.
(6) If the printed circuit board with the devices mounted on it will be subjected to vibration from
external sources, use sockets which have a strong contact pressure so as to prevent the sockets
and devices from vibrating relative to one another.