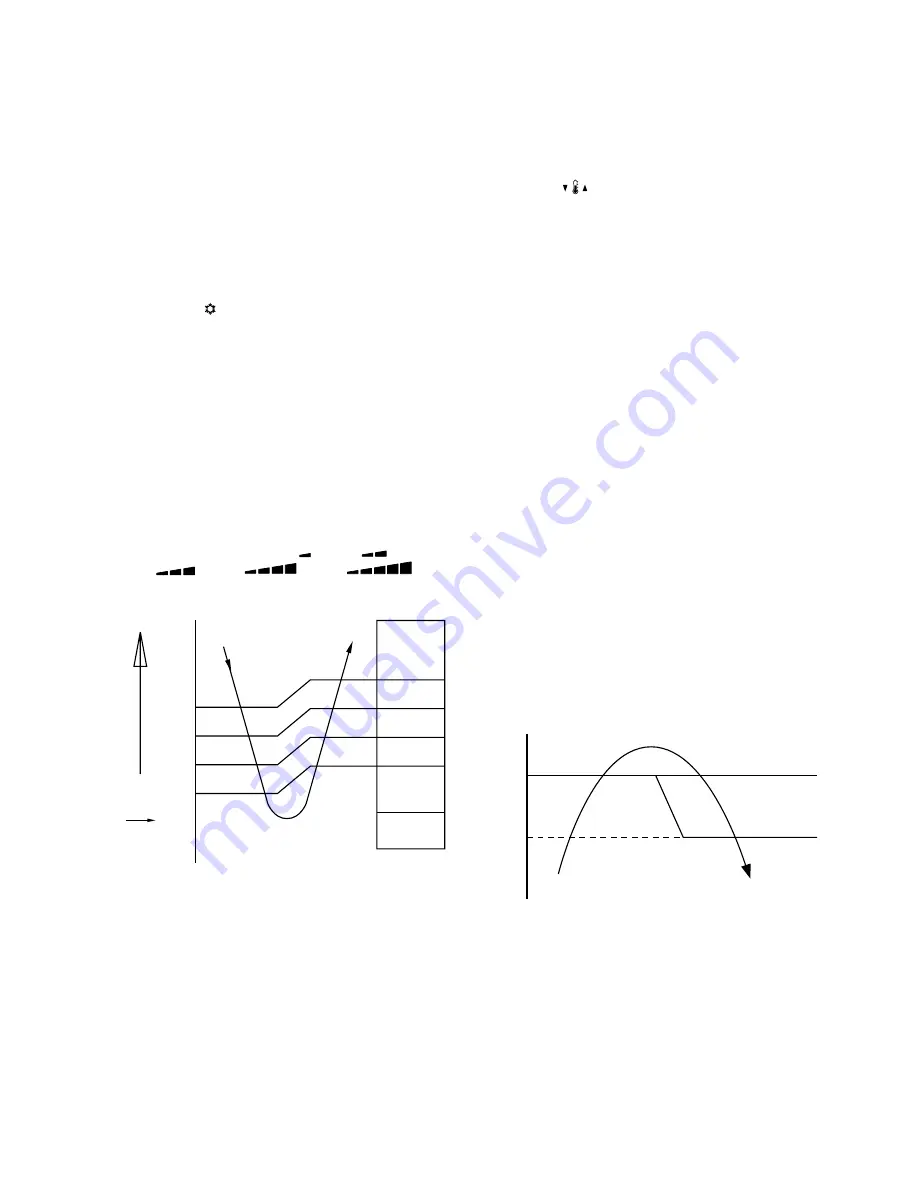
FILE NO. SVM-03008
– 26 –
8-2. Description of Operation Circuit
•
Turning [ON] the breaker flashes the operation
lamp. (1Hz)
This is the display of power-ON (or notification of
power failure).
•
When pushing [START/STOP] button of the
remote control, receive sound is issued from the
main unit, and the next operations are performed
together with opening the vertical air flow louvers.
8-2-1. Cooling operation
(The Remote Control MODE Button is Set to
the COOL Position)
•
Once the setting is made, the operation mode is
memorized in the microcomputer so that the same
operation can be effected thereafter simply by
pushing [START/STOP] button.
•
A cooling operation signal is transmitted to
outdoor unit.
•
The outdoor unit controls the outdoor fan relay
R01, R02 and R03, and the compressor motor
speed according to the operation command signal
sent from the indoor unit.
•
When [FAN] button is set to AUTO, the indoor fan
motor operates as shown in Fig. 8-2-1. When
[FAN] button is set to LOW , LOW
+
,
MED
, MED
+
, HIGH
, the
motor operates with a constant air flow.
NOTE :
*1: Calculated from difference in motor speed of M+
and L, and controlled.
Fig. 8-2-1 Setting of air flow [Fan AUTO]
(1) Cooling capacity control
•
The cooling capacity and room temperature
are controller by changing the compressor
motor speed according to both the difference
between the temperature detected by the room
temperature sensor and the temperature set by
TEMP
button and also any change in room
temperature.
•
When compressor has been activated or
reactivated, it operates with Max.41 rps for 2
minutes, with Max.91 rps from 2 minutes to 3
minutes, and with Max.88 rps after 3 minutes
passed.
•
When room temperature is lower than set
temperature, indoor fan motor is operated at
fan speed L as shown in Fig. 8-2-1 while the
outdoor unit stops.
(2) Prevent-freezing control
If temperature of indoor heat exchanger detected
by the indoor heat exchanger sensor is 5
°
C lower,
compressor motor speed is gradually lowered to
prevent freezing of the indoor heat exchanger. If
temperature is 7
°
C or higher, return the operation
to the above item (1).
(3) Current release control
The input current of compressor and outdoor fan
motor (Precisely inverter main circuit control
section) which occupy most of air conditioner input
is detected by the outdoor current sensor, and
compressor motor speed is gradually lowered so
that current value does not exceed 9.0A if current
value exceeds 9.0A. When the current value
lowers to 8.5A, return the operation to the above
item (1).
Fig. 8-2-2
Set
temp.
+3
M+
*1
*1
*1
L
+2.5
+2
+1.5
+1
+0.5
0
−
0.5
°
C
(Room temp.)
−
(Set temp.)
In normal
operation
Normal control
9.0
8.5
Current v
a
lue (A)
Comp. motor
speed down
Comp. motor
speed keep