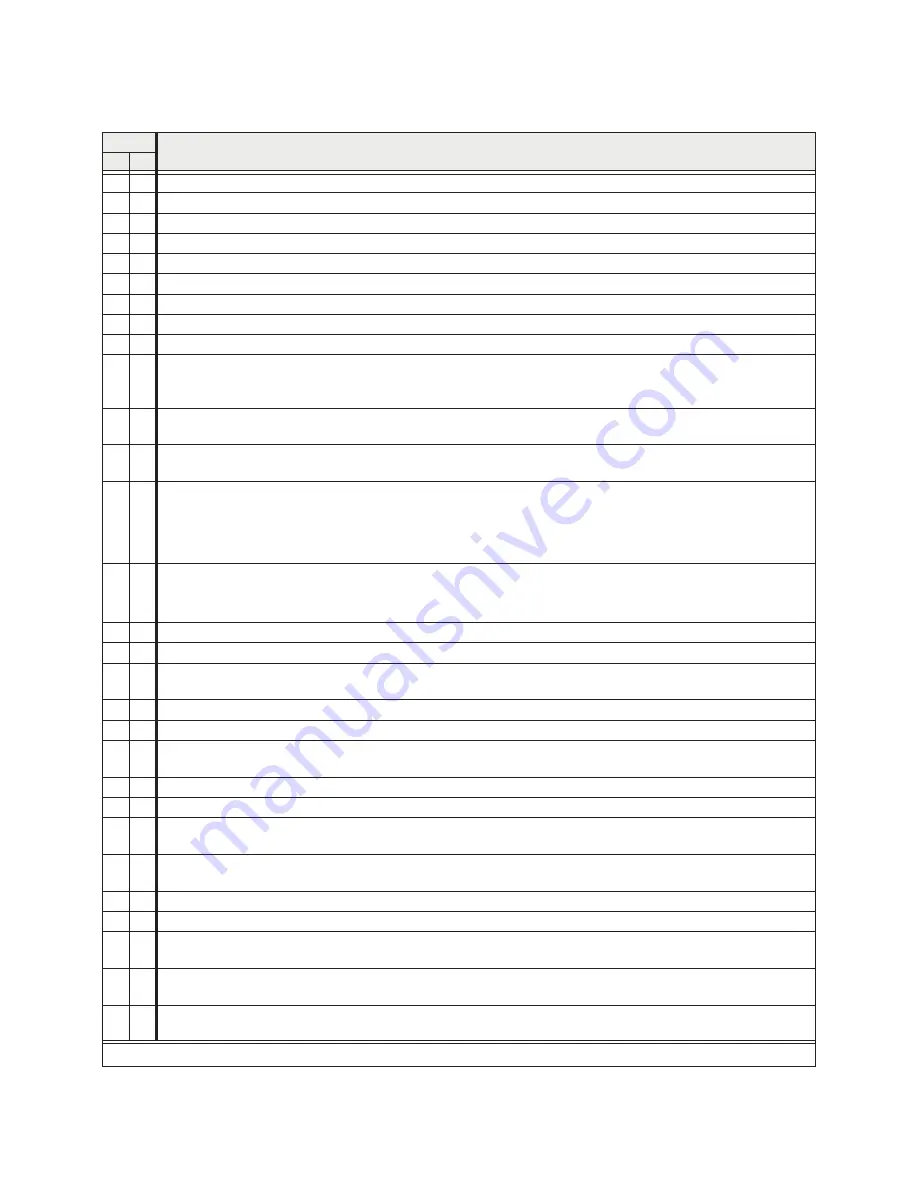
186
Q9 ASD Installation and Operation Manual
Table 4. Discrete Input Terminal Assignment Selections and Descriptions.
Sel. No.
Terminal Selection Descriptions
NO NC
0
1
Unassigned
— No operation.
2
3
Forward
— Provides a Forward run command.
4
5
Reverse
— Provides a Reverse run command.
6
7
Standby
— Enables the Forward and Reverse operation commands.
8
9
Reset
— Resets the device and any active faults.
10
11
(Pre)Set Speed 1
—Preset Speed 1 is used as the LSB of the 4-bit nibble that is used to select a Preset Speed.
12
13
(Pre)Set Speed 2
— Preset Speed 2 is used as the second bit of the 4-bit nibble that is used to select a Preset Speed.
14
15
(Pre)Set Speed 3
— Preset Speed 3 is used as the third bit of the 4-bit nibble that is used to select a Preset Speed.
16
17
(Pre)Set Speed 4
— Preset Speed 4 is used as the MSB of the 4-bit nibble that is used to select a Preset Speed.
18
19
Jog
— Jog is the term used to describe turning on the motor for discrete increments of time and is used when precise
positioning of motor-driven equipment is required. This terminal activates a Jog for the duration of the activation. The
Jog settings may be configured at
20
21
Emergency Off
— Terminates the output signal from the drive and may apply a brake if so configured. The braking
method may be selected at
.
22
23
DC Braking
— The drive outputs a DC current that is injected into the windings of the motor to quickly brake the
motor.
24
25
A/D 1/2
— Accel/Decel Switching 1 and 2 — Activate or deactivate this terminal to toggle to and from the Accel/
Decel profile 1 and 2.
Accel/Decel profiles are comprised of the Accel/Decel settings, Pattern, and Switching Frequency, respectively.
See
for more information on this terminal setting.
28
29
Motor 1/2
— Motor Profile 1 and 2 — Activate or deactivate this terminal to select Motor profile 1 or 2, respectively.
Motor profiles are comprised of Frequency Mode 1 and 2, Base Frequency/Base Frequency Voltage, Torque
Boost, and Electronic Thermal Protection Level settings.
36
37
PID Off
— Turns off PID control.
46
47
External Over-heat
— Causes an Over-Heat Trip (OH).
48
49
Local Priority
(Cancels Serial Priority) — Overrides any serial control and returns the Command and Frequency
control to
and
.
50
51
Hold
(3-Wire Stop) — Decelerates the motor to a stop.
52
53
PID Differentiation/Integration Clear
— Clears the PID value.
54
55
PID Forward/Reverse Switching
— Toggles the gradient characteristic of the feedback response of the V/I
terminal during PID-controlled operation.
56
57
Forced Run
— PID control is ignored for the duration of activation.
58
59
Fire Speed
— Run
for the duration of the activation (see
for more information on this setting).
60
61
My Function Run
— Activates the configured My Function feature. See
for more information on this
parameter.
66
67
Autotuning
— Initiates the Autotune function. Set
to Autotuning by Input Terminal Signal to use this
function.
70
71
Servo Lock
— Holds the motor at 0 Hz until a Run command is received.
74
75
kWH Clear
— Clears the kWH Meter display.
76
77
Trace Back
— Initiates the data Read/Store function of the Trace Selection parameter. See
for more
information on this feature.
80
81
Damper Feedback
— Activation of this terminal indicates an open damper and enables the system for normal
operation. This terminal connects to a Damper Open/Damper Closed switch.
86
87
Binary Write
— Writes the status of the discrete input terminals to the control board during binary input speed
control.
Note:
NO/NC = Normally Open/Normally Closed.
Summary of Contents for Q9 Series
Page 2: ......
Page 4: ......
Page 8: ......
Page 219: ...Q9 ASD Installation and Operation Manual 209 Figure 30 See Table 14 for Actual Dimensions ...