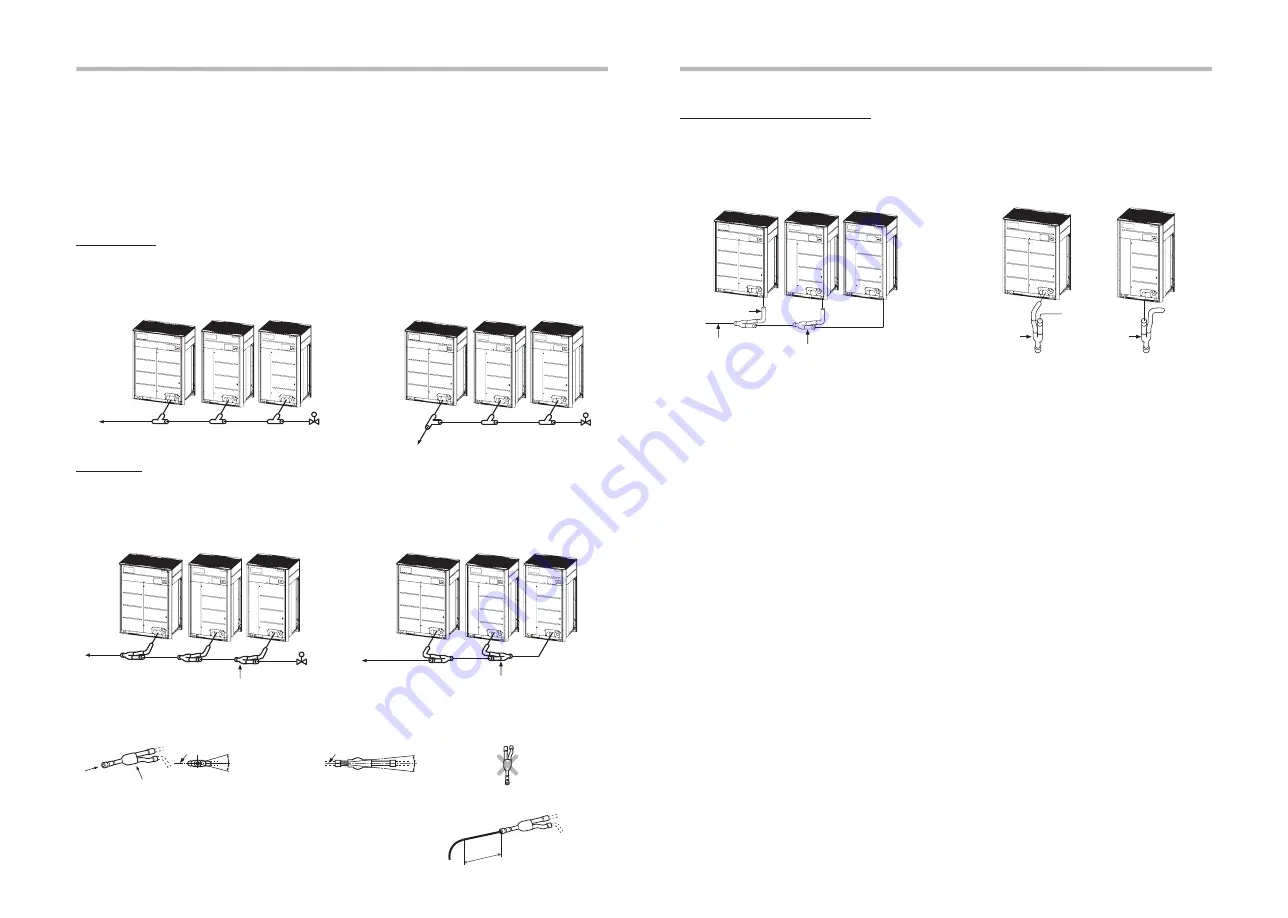
24-EN
23-EN
– 12 –
EN
5. Be careful of the connecting arrangement of the header unit and follower units. Set the outdoor units in order of
capacity from the one with the largest capacity. (A (Header unit)
≥
B
≥
C)
• Be sure to use a header unit for the leading outdoor unit to be connected to the main pipe. (Figure 1 and 3)
• Be sure to use a outdoor unit connection piping kit (RBM-BT14E / RBM-BT24E/ RBM-BT34E : separately
purchased) to connect each outdoor unit.
• Be careful of the direction of the Outdoor unit connection piping kit for the liquid side. (As shown in Figure 2, a
Outdoor unit connection piping kit cannot be attached so that the refrigerant of the main pipe
fl
ows directly into
the header unit.)
Liquid piping
Header unit
A
Header unit
A
Follower unit
B
Follower unit
B
Follower unit
C
Follower unit
C
Main pipe
Main pipe
To the indoor unit
To the indoor unit
Incorrect
T
Figure 1
T
Figure 2
Correct
Incorrect
Gas piping
Header unit
A
Header unit
A
Follower unit
B
Follower unit
B
Follower unit
C
Follower unit
C
Main pipe
Main pipe
To the indoor unit
To the indoor unit
To gas-side branch unit
Extension valve
T
Figure 3
T
Figure 4
Correct
Incorrect
[Inverse connection of a gas-side branch unit]
• When attaching a Y-shaped branching joint for the gas side, attach it level with the ground (Be sure not to
exceed ±15 degrees.). Regarding a T-shape branching joint for the liquid side, there is no restriction for its angle.
A
B
(Horizontal line)
(Horizontal line)
(A arrow view)
(B arrow view)
Within ±15
degrees
Within ±15 degrees
Do not connect
the branching
vertically.
At a level position
500 mm
or more
• In case of using the Y-shaped branching joint for connecting between
outdoor units (Discharge gas joint and Suction gas joint), please keep
the straight part of at least 500 mm at the inlet.
When drawing pipes downward
Header unit
A
[Vertical connection of branch units]
Follower unit
B
Follower unit
C
L-shaped
pipe
To gas-side branch
unit
To gas-side branch
unit
To gas-side
branch unit
To gas-side
branch unit
T
Figure 5
T
Figure 6
Correct
Incorrect
• Adding only one follower unit is possible. Install the additional unit so that its position is opposite to the header
unit. Use an extension valve for installation (See the
fi
gure above.).
Specify the pipe diameter in advance to allow for adding another unit.