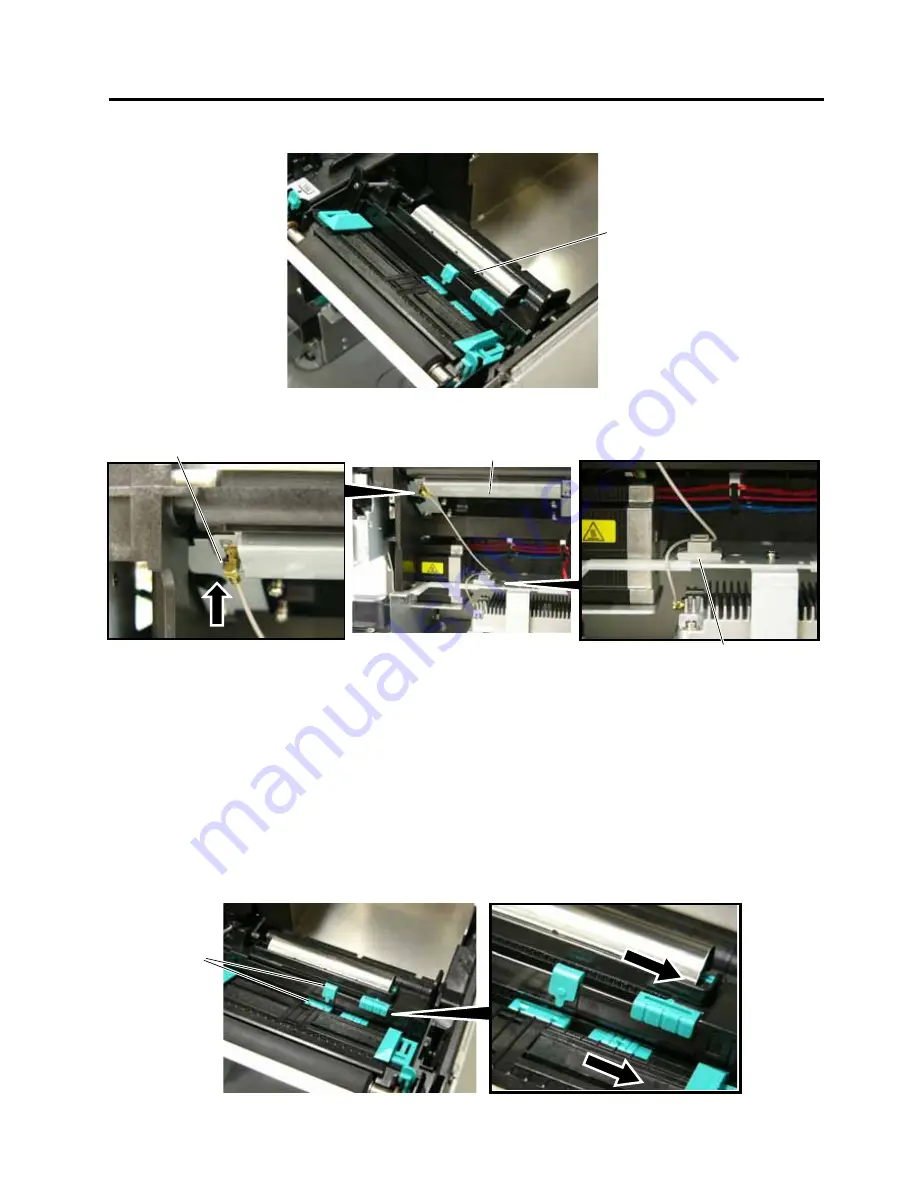
INSTALLATION PROCEDURE FOR OPTIONAL EQUIPMENT
EO15-33001A
(Revision Date: Feb. 25, 2008)
8. RFID Module: B-SA704-RFID-U2-EU-R
8- 9
15. Re-place the Media Sensor Block.
16. Connect the Antenna Cable to the Antenna Ass’y until it clicks, and fasten the Antenna Cable with the
Cable Clamp, as shown below.
17. Reattach the Side Panel to the printer with reference to Step 2.
18. Close the Front Cover and the Top Cover. Now, an installation of the RFID Module has been finished.
In the case short-pitch RFID tags (20mm) are used, refer to Section 4 to attach the Shield Sheet and
Section 5 to configure the RFID module settings.
When short-pitch tags are not used, refer to Section 5 to configure the RFID module settings.
•
When Short-Pitch RFID Tags (20mm) are used:
When short-pitch tags (20 mm) are used, the supplied Shield Sheet needs to be attached for proper
read/write operation.
Follow the procedure below to attach the Shield Sheet to the Media Guide Bock.
1. Before attaching the Shield Sheet, move the Media Sensor to the right-most position. Failure to do this
disables a media sensor position adjustment.
Media Sensor Block
Antenna Ass’y
Antenna Cable
Cable Clamp
Media
Sensor