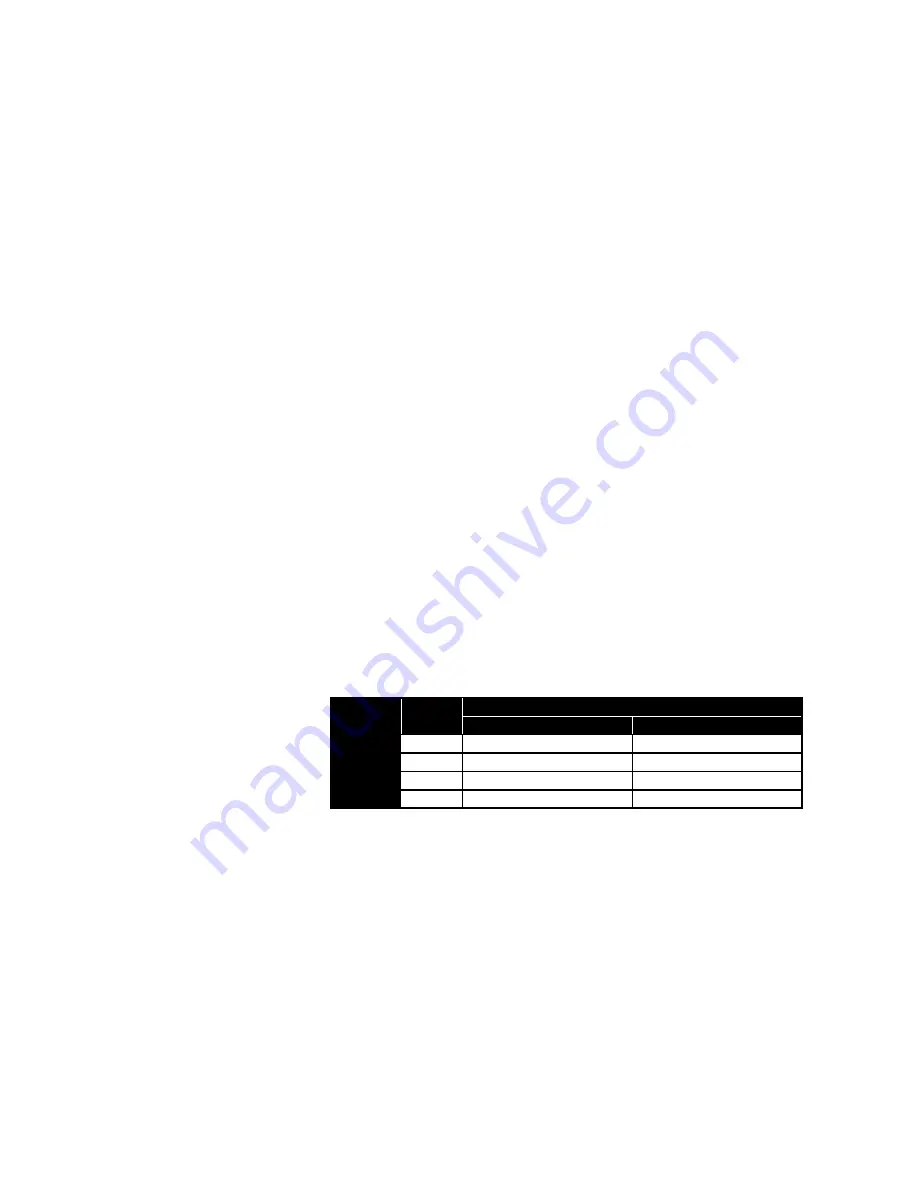
TD - Series
- 22 -
TD Series
Digital Solid State Soft Starter 48 - 1250A
5.5.2 Starting Mode
The
TD
is capable of several different starting modes, but is set from the factory
for the most common applications. A second ramp profile is available for use
should you need it but unless wired to do so, the
TD
defaults to Ramp 1. This
section describes functions for Ramp 1, with references to function numbers that
do the same thing for Ramp 2 if required. Refer to Appendix 2 for a detailed
description of the differences in Ramp Profiles and their uses.
F010 = Ramp Profile Selection
Factory Setting = 1
Range
=
1 - 4
This Function selects the type of Ramp Profile desired. Ramp profiles
can be either Voltage Ramp or Current Ramp. See Appendix 2 for
details. Each Ramp Profile consists of 3 settings:
Initial Torque, Ramp Time and Maximum Current Limit
Because there are two ramps available, there are 4 settings to cover
the combinations of profiles possible. If you are not using the 2nd
ramp, the TD will ignore all settings in reference to Ramp 2.
Select Voltage Ramp by setting
F010 = 1
(factory default)
When Voltage Ramp is selected,
Set Initial Torque with
F011
(see below)
Set Ramp with
F013
(see below)
Set Maximum Current Limit with
F014
(see below)
Or;
Select Current Ramp by setting
F010 = 2
When Current Ramp is selected,
Set Initial Torque with
F012
(see below)
Set Ramp Time with
F013
(see below)
Set Maximum Current Limit with
F014
(see below)
Ramp 1
Ramp 2
1
Voltage Ramp
Voltage Ramp
2
Current Ramp
Current Ramp
3
Voltage Ramp
Current Ramp
4
Current Ramp
Voltage Ramp
Ramp Type
Setting
F010
Ramp
Profile
Selection
F011 = Initial Voltage of Ramp 1
Factory Setting = 60%
Range = 0 - 100%
Sets the initial voltage of ramp 1 when
F010 = 1 or 3
. The initial torque
level should be set to provide just enough torque to make the motor
shaft begin to rotate while preventing torque shock damage to
mechanical components.
F012 = Initial Current of Ramp 1
Factory Setting = 200%
Range = 0 - 600%
Sets the initial current of ramp 1 (when
F010 = 2 or 4)
. Current
percentages are based on the Motor FLA as set in F001. The initial
torque level should be set to provide just enough torque to make the
motor shaft begin to rotate while preventing torque shock damage to
mechanical components.