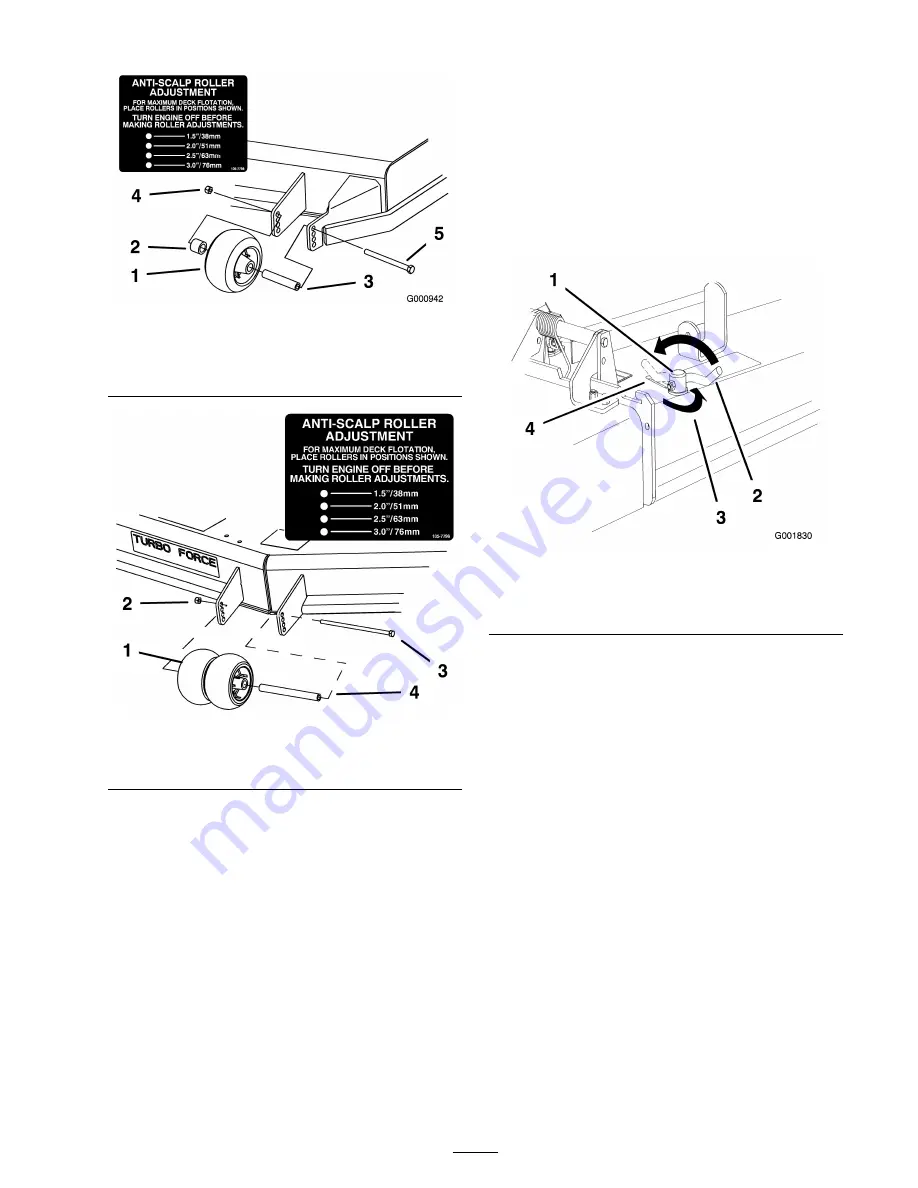
Figure 20
1. Anti-scalp roller
4. Flange Nut
2. Spacer
5. Bolt
3. Bushing
Figure 21
1. Anti-scalp roller
3. Flange Nut
2. Bushing
4. Bolt
Adjusting the Flow Bafe
The mower discharge flow can be adjusted for
different types of mowing conditions. Position the
cam lock and baffle to give the best quality of cut.
1. Disengage the PTO, move the motion control
levers to the neutral locked position and set
the parking brake.
2. Stop the engine, remove the key, and wait for
all moving parts to stop before leaving the
operating position.
3. To adjust the cam lock, swing the lever up to
loosen the cam lock (Figure 22).
4. Adjust the baffle and cam lock in the slot to
the desired discharge flow.
5. Swing the lever back over to tighten the baffle
and cam lock (Figure 22).
6. If the cam does not lock the baffle into place
or it is too tight, loosen the lever and then
rotate the cam lock. Adjust the cam lock until
the desired locking pressure is achieved.
Figure 22
1. Cam lock
3. Rotate cam to increase or
decrease locking pressure
2. Lever
4. Slot
Positioning the Flow Bafe
The following figures are only recommendations
for use. Adjustments will vary by grass type,
moisture content, and height of grass.
Note:
If the engine power draws down and the
mower ground speed is the same, open up the
baffle.
Position A
This is the full rear position. The suggested use
for this position is a follows.
•
Use for short, light grass mowing conditions.
•
Use in dry conditions.
•
For smaller grass clippings.
•
Propels grass clippings farther away from the
mower.
23
Summary of Contents for Z449 Z Master
Page 8: ...Slope Chart 8 ...
Page 10: ...98 5954 103 2644 105 7798 107 1613 107 1687 107 1688 10 ...
Page 56: ...Schematics Wire Diagram Rev A 56 ...
Page 57: ......
Page 58: ......