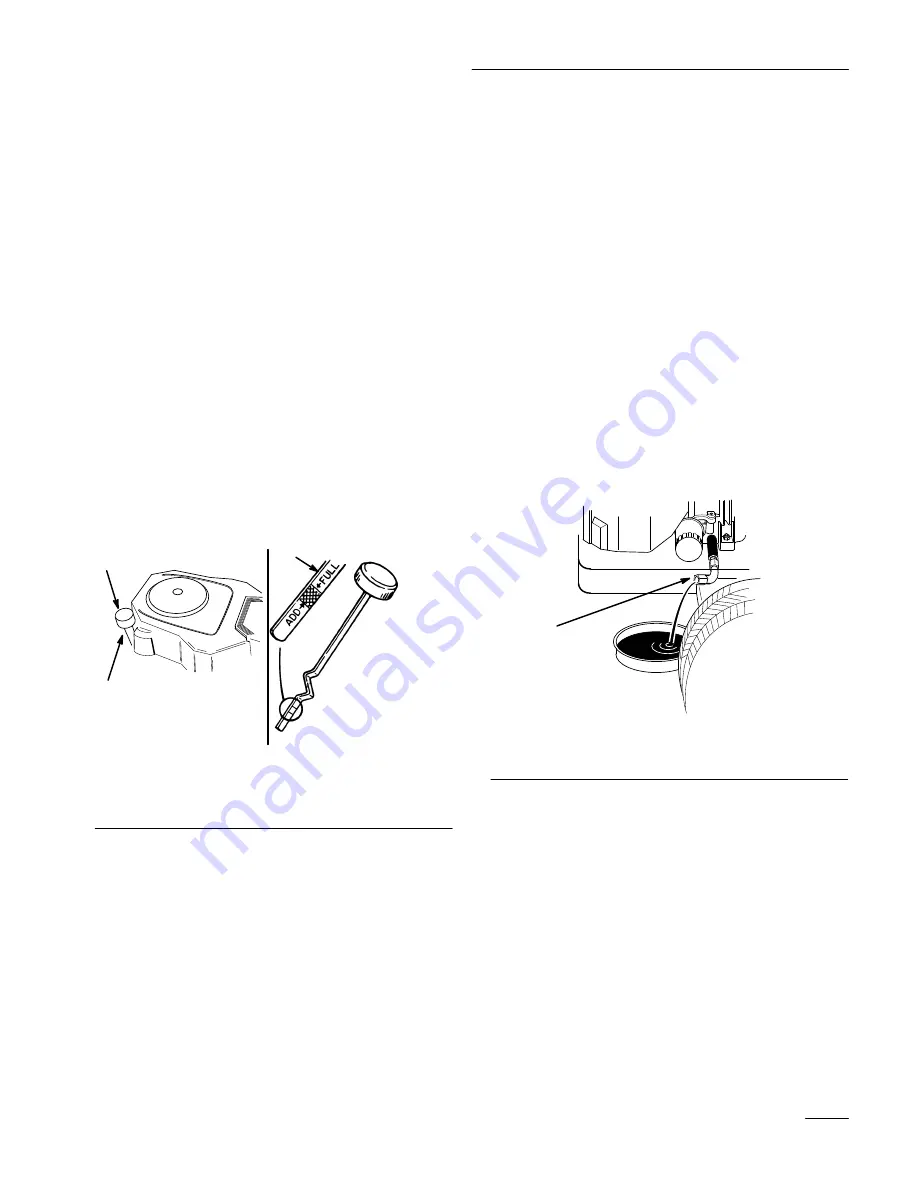
Maintenance
23
Checking Oil Level
1.
Park the machine on a level surface, disengage
the power take off (PTO) and turn the ignition
key to “OFF” to stop the engine. Remove the
key.
2.
Clean around the oil dipstick (Fig. 16) so dirt
cannot fall into the filler hole and damage the
engine.
3.
Unscrew the oil dipstick and wipe the metal end
clean (Fig. 16).
4.
Slide the oil dipstick fully into the filler tube, do
not thread onto tube (Fig. 16). Pull the dipstick
out and look at the metal end. If oil level is low,
slowly pour only enough oil into the filler tube
to raise the level to the “FULL” mark.
IMPORTANT: Do not overfill the crankcase
with oil because the engine may be damaged.
ÌÌÌ
ÌÌÌ
ÌÌÌ
1
2
3
m–3081
Figure 16
1.
Oil dipstick
2.
Metal end
3.
Filler tube
Changing/Draining Oil
1.
Start the engine and let it run five minutes. This
warms the oil so it drains better.
2.
Park the machine so that the drain side is slightly
lower than the opposite side to assure the oil
drains completely. Then disengage the power
take off (PTO), set the parking brake, and turn
the ignition key to “OFF” to stop the engine.
Remove the key.
3.
Place a pan below the oil drain. Open the drain
cap (Fig. 17).
4.
When oil has drained completely, close the drain
cap.
Note:
Dispose of the used oil at a certified
recycling center.
1
m–3082
Figure 17
1.
Oil drain
5.
Slowly pour approximately 80% of the specified
amount of oil specified, page 22, into the filler
tube (Fig. 16). Now check the oil level; refer to
Checking Oil Level, page 23. Slowly add
additional oil to bring to “FULL” mark on
dipstick.