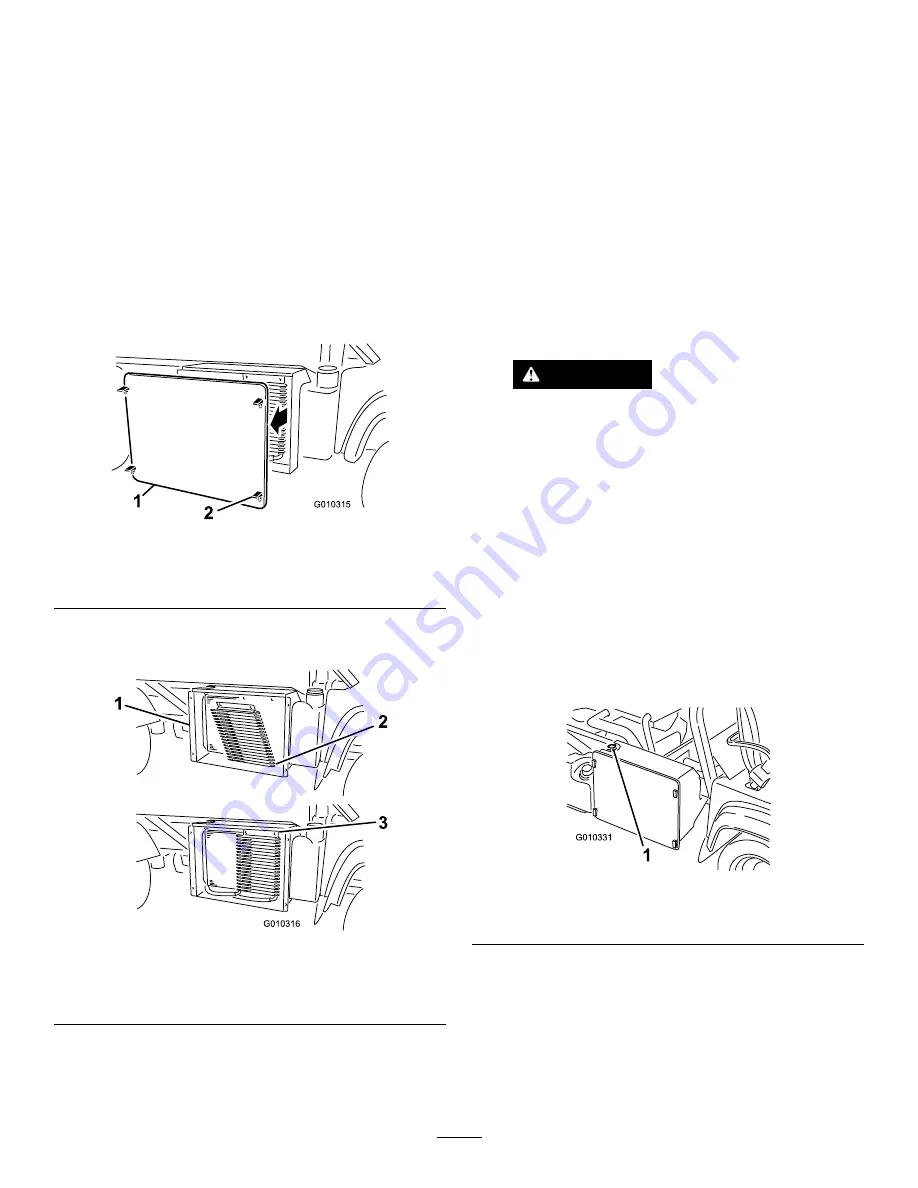
Removing Debris from the
Cooling System
Service Interval:
Before each use or daily—Remove
debris from the engine area and
radiator. (Clean it more frequently in
dirty conditions.)
1.
Park the machine on a level surface.
2.
Engage the parking brake.
3.
Shut off the engine and remove the key.
4.
Clean the engine area thoroughly of all debris.
5.
Unlatch and remove the radiator screen from the
front of the radiator (
g010315
Figure 54
1.
Radiator screen
2.
Latch
6.
If equipped, rotate the latches and pivot the oil
cooler away from the radiator (
g010316
Figure 55
1.
Radiator housing
3.
Latches
2.
Oil cooler
7.
Clean the radiator, oil cooler, and screen with
compressed air.
Note:
Blow debris away from the radiator.
8.
Install the cooler and screen to the radiator.
Changing the Engine
Coolant
Service Interval:
Every 1,000 hours/Every 2 years
(whichever comes first)
Cooling-system capacity:
3.7 L (4 US qt)
Coolant type:
a 50/50 solution of water and
permanent ethylene-glycol antifreeze
1.
Park the machine on a level surface.
2.
Raise the bed and install the bed safety support
on the extended lift cylinder to secure the bed.
CAUTION
If the engine has been running, the
cooling system pressurizes with hot
coolant that can escape and cause burns.
•
Do not open the radiator cap when the
engine is running.
•
Allow the engine to cool for at least
15 minutes or until the radiator cap is
cool enough to touch without burning
your hand.
•
Use a rag to open the radiator cap.
Open the cap slowly to allow the
steam to escape.
3.
Remove the radiator cap (
).
g010331
Figure 56
1.
Radiator cap
4.
Remove the reserve-tank cap (
).
49
Summary of Contents for Workman HDX 07383
Page 64: ...Notes ...
Page 65: ...Notes ...