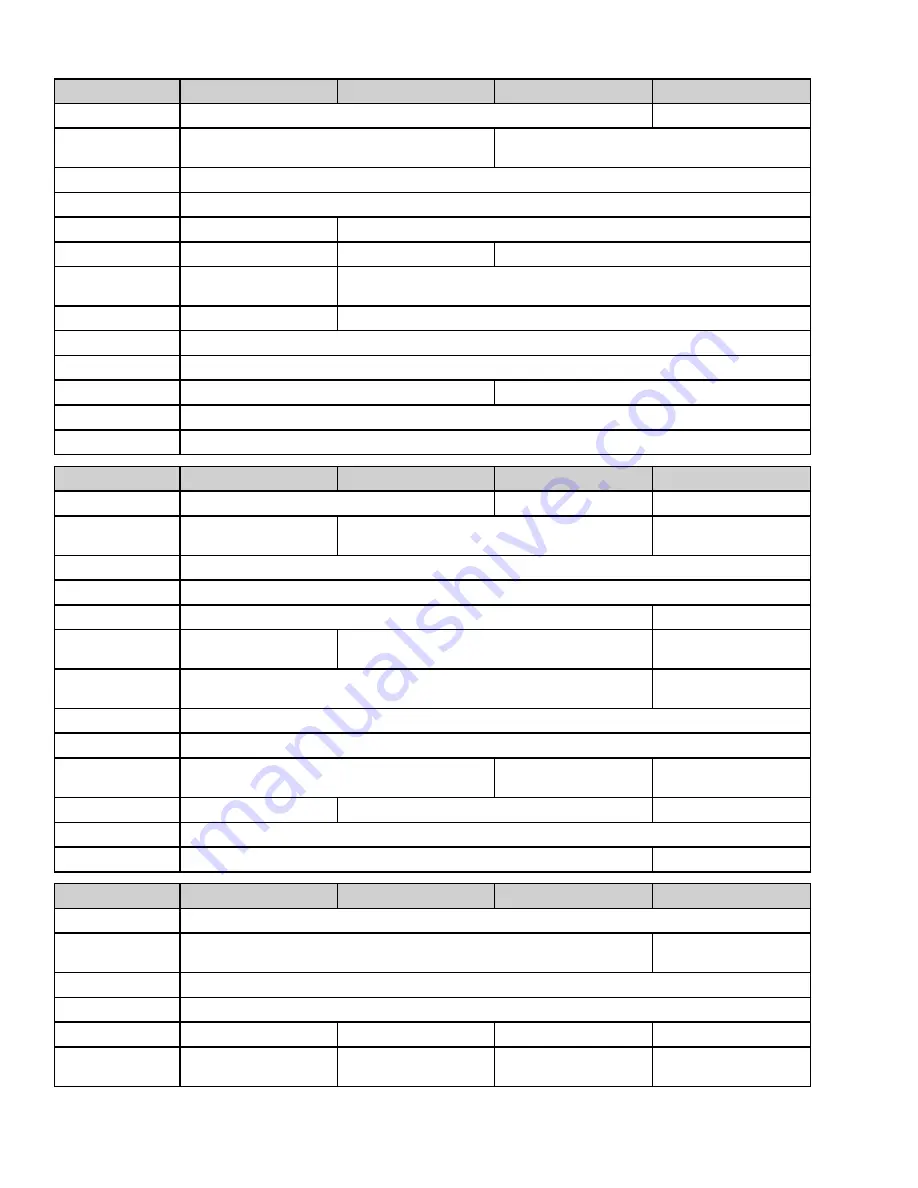
Specifications
Model
74685
74687
74690
74694
Deck Size
107 cm (42 inches)
127 cm (50 inches)
Deck
Construction
Stamped
Fabricated
HOC Type
3 Point
HOC Range
3.81–11.43 cm (1.5-4.5 inches)
Engine
Toro Single
Toro Twin
Engine Model
LC1P92F-1 (CE)
LC2P77F
LC2P77F(49 ST)
Engine
Displacement
452cc
708cc
Engine RPM
2600 ± 100 rpm
2850 ± 100 rpm
Fuel Tank Cap
11 L (3 gallons)
Hydro Transaxle
Hydro-Gear ZT-2100
Suspension
N/A
MYRIDE®
Bagger Capacity
8 Bushel
Battery Size
230 CCA
Model
75742TA
75745TA
75755TA
74710
Deck Size
107 cm (42 inches)
127 cm (50 inches)
81 cm (32 inches)
Deck
Construction
Stamped
Fabricated
Stamped
HOC Type
3 Point
HOC Range
3.81–11.43 cm (1.5-4.5 inches)
Engine
Toro Twin
Toro Single
Engine Model
LC2P77F
LC2P77F (49 ST)
LC1P92F-1
(DOM,50ST)
Engine
Displacement
708cc
452cc
Engine RPM
3300 ± 100 rpm
Fuel Tank Cap
11 L (3 gallons)
Hydro Transaxle
Hydro-Gear ZT-2100
Hydro-Gear ZT-2200
Long Axle
Hydro-Gear ZT-2100
Suspension
N/A
MYRIDE®
N/A
Bagger Capacity
8 Bushel
Battery Size
230 CCA
195 CCA
Model
75740
75741
75742
75743
Deck Size
107 cm (42 inches)
Deck
Construction
Stamped
Fabricated
HOC Type
3 Point
HOC Range
3.81–11.43 cm (1.5-4.5 inches)
Engine
Toro Single
Kawasaki Twin
Toro Twin
Kawasaki Twin
Engine Model
LC1P92F-1
(DOM,50ST)
FR600V-_S04-R
(CARB)
LC2P77F
FR691V-AS26-R
Specifications and Maintenance: Specifications
Page 2–2
TIMECUTTER® Service Manual
3433-938 Rev A
Summary of Contents for TIME CUTTER ZS 4200S
Page 2: ...Revision History Revision History Page 2 TIMECUTTER Service Manual 3433 938 Rev A ...
Page 6: ...Preface Page 6 TIMECUTTER Service Manual 3433 938 Rev A ...
Page 26: ...Troubleshooting General Troubleshooting Page 3 6 TIMECUTTER Service Manual 3433 938 Rev A ...
Page 50: ...Engine Service and Repairs Page 4 24 TIMECUTTER Service Manual 3433 938 Rev A ...
Page 154: ...Chassis Service and Repairs Page 5 104 TIMECUTTER Service Manual 3433 938 Rev A ...
Page 188: ...Mower Deck System Service and Repairs Page 7 16 TIMECUTTER Service Manual 3433 938 Rev A ...
Page 212: ...Electrical System Service and Repairs Page 8 24 TIMECUTTER Service Manual 3433 938 Rev A ...
Page 215: ... Drawing Rev A Sheet 1 3433 938 Rev A Page A 3 Electrical Schematic g316875 ...