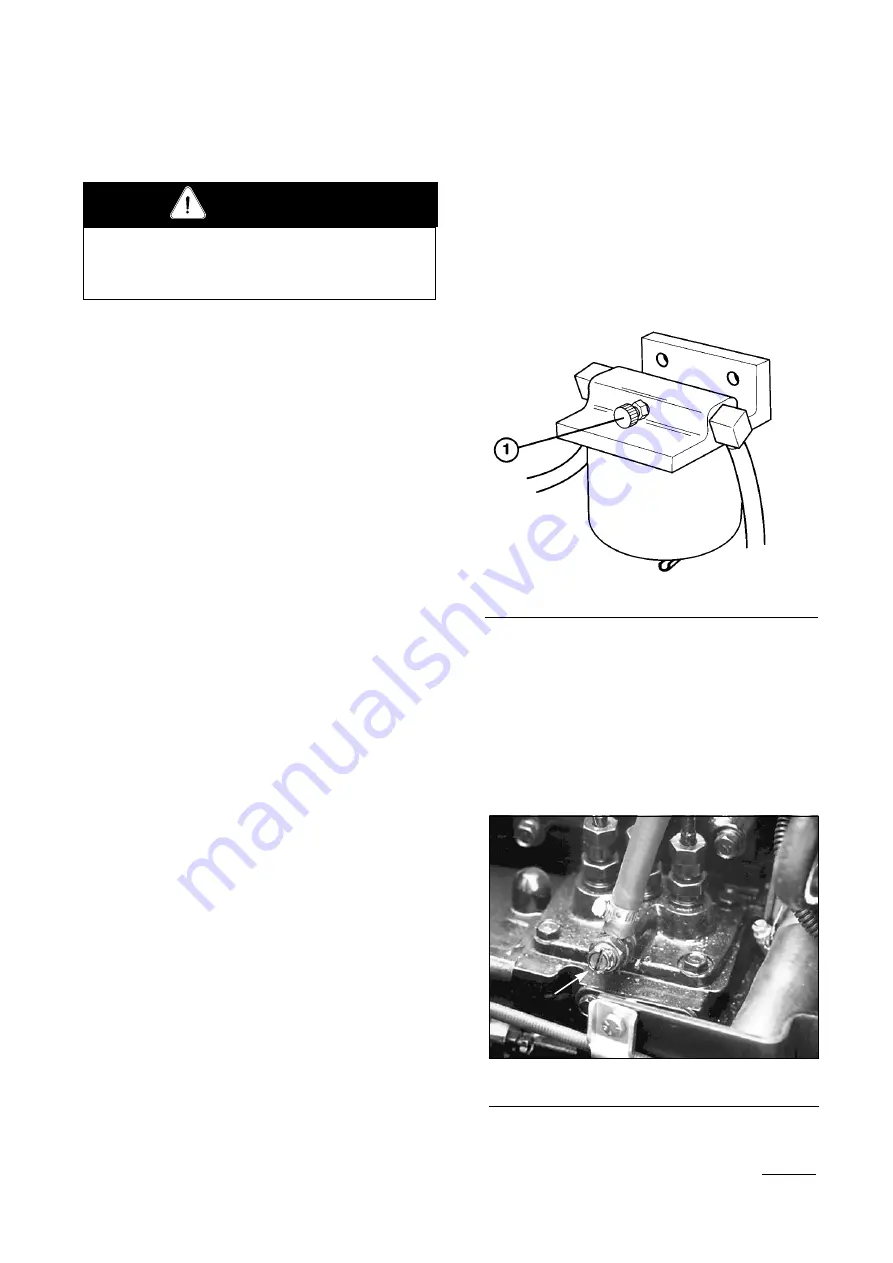
17
STARTING AND STOPPING
IMPORTANT: The fuel system must be bled if
any of the following situations have occurred.
A.
Initial start up of a new machine.
B.
The engine has ceased running due to lack of
fuel.
C.
Maintenance has been performed upon fuel sys-
tem components; i.e., filter replaced, separator
serviced, etc.
Refer to Bleeding The Fuel System
1.
Sit on the seat, keeping your foot off the trac-
tion pedal. Assure the parking brake is engaged,
the traction pedal is in NEUTRAL, the throttle
is in the SLOW position and the ENABLE /
DISABLE switch is in the DISABLE position.
2.
Turn the ignition switch to the ON/Preheat posi-
tion. An automatic timer will control preheat
for 6 seconds. After preheat, turn the key to
START. CRANK THE ENGINE FOR NO
LONGER THAN 15 SECONDS. Release the
key when the engine starts. If additional preheat
is required, turn the key to OFF then to the
ON/Preheat position. Repeat the process as
needed.
3.
Run the engine at idle speed or partial throttle
until the engine warms up.
4.
To stop, move all controls to NEUTRAL and
set the parking brake. Return the throttle to the
idle position, turn the key to OFF and remove it
from switch.
BLEEDING THE FUEL SYSTEM
1.
Raise the hood over the engine.
2.
Loosen the air bleed screw on top of the fuel fil-
ter/water separator (Fig. 15)
3.
Turn the key in the ignition switch to ON. The
electric fuel pump will begin operation, forcing
air out around the air bleed screw. Leave the
key in the ON position until a solid stream of
fuel flows out around the screw. Tighten the
screw and turn the key to OFF.
4.
Open the air bleed screw on the fuel injection
pump with a 12 mm wrench.
Before servicing or making adjustments to the
machine, stop the engine and remove the key from
the switch.
CAUTION
Operation
Figure 15
1.
Air Bleed Screw
Figure 16
1.
Fuel injection Pump Bleed Screw
➀
Summary of Contents for reelmaster 5300-d
Page 40: ......