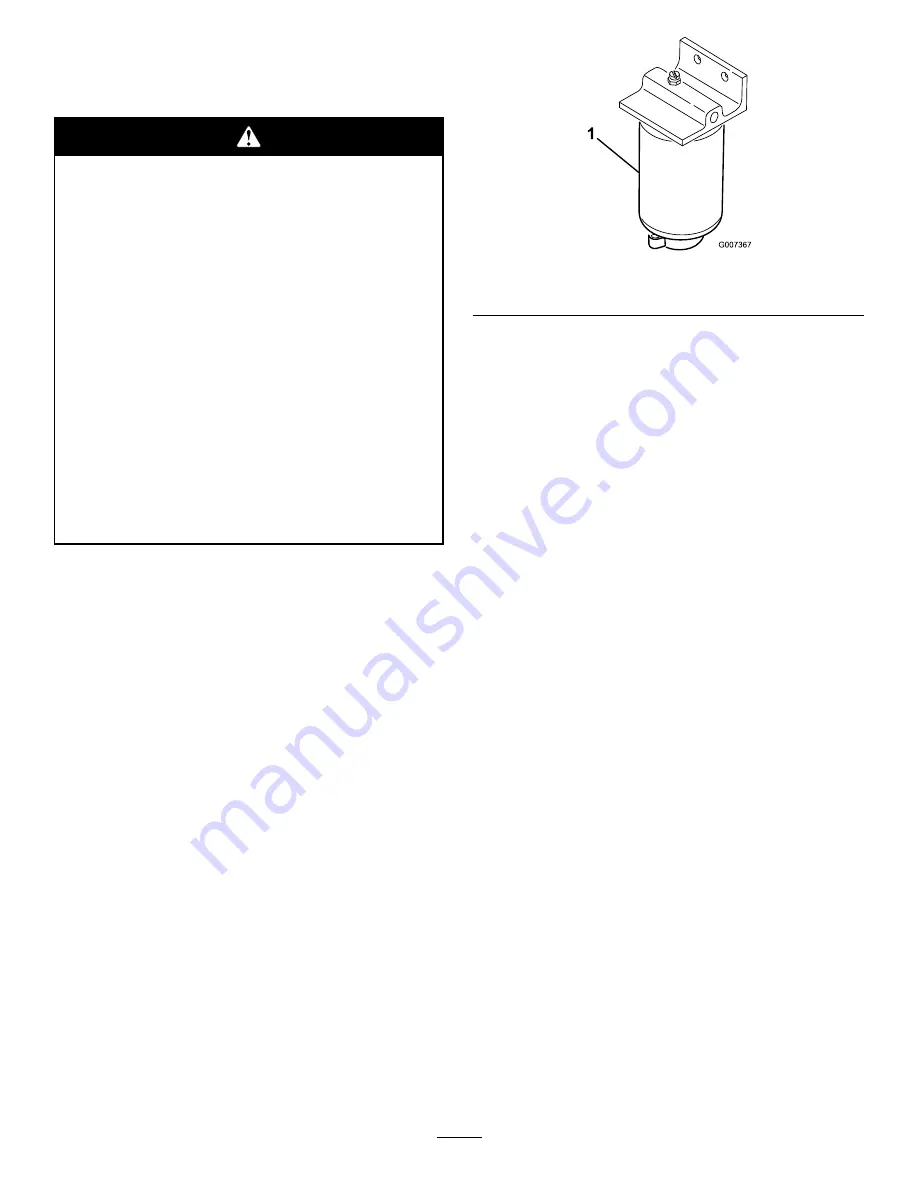
Fuel System
Maintenance
Under certain conditions, diesel fuel and fuel
vapors are highly flammable and explosive. A
fire or explosion from fuel can burn you and
others and can cause property damage.
•
Use a funnel and fill the fuel tank outdoors,
in an open area, when the engine is off and
is cold. Wipe up any fuel that spills.
•
Do not fill the fuel tank completely full. Add
fuel to the fuel tank until the level is 1/4 to
1/2 in. (6 to 13 mm) below the bottom of
the filler neck. This empty space in the tank
allows the fuel to expand.
•
Never smoke when handling fuel, and stay
away from an open flame or where fuel
fumes may be ignited by a spark.
•
Store fuel in a clean, safety-approved
container and keep the cap in place.
Draining the Fuel Tank
Service Interval:
Every 800 hours
Before storage
Drain and clean the fuel tank if the fuel system becomes
contaminated or if the machine is to be stored for an
extended period. Use clean fuel to flush out the tank.
Checking the Fuel Lines and
Connections
Check the fuel lines and connections every 400 hours
or yearly, whichever comes first. Inspect them for
deterioration, damage, or loose connections.
Servicing the Water Separator
Service Interval:
Every 400 hours
Drain water or other contaminants from water separator
(Figure 64) daily. Replace filter canister after every 400
hours of operation.
1. Place a clean container under the fuel filter.
2. Loosen the drain plug on the bottom of the filter
canister.
Figure 64
1.
Water separator filter canister
3. Clean the area where the filter canister mounts.
4. Remove the filter canister and clean the mounting
surface.
5. Lubricate the gasket on the filter canister with clean
oil.
6. Install the filter canister by hand until the gasket
contacts mounting surface, then rotate it an
additional 1/2 turn.
7. Tighten the drain plug on the bottom of the filter
canister.
Fuel Pick-up Tube Screen
The fuel pick-up tube, located inside the fuel tank, is
equipped with a screen to help prevent debris from
entering the fuel system. Remove the fuel pick-up tube
and clean screen as required.
Bleeding Air from the Fuel
Injectors
Note:
This procedure should be used only if the
fuel system has been purged of air through normal
priming procedures and the engine will not start; refer
to Bleeding the Fuel System in , page .
1. Loosen the pipe connection to the No. 1 nozzle and
holder assembly (Figure 65).
45