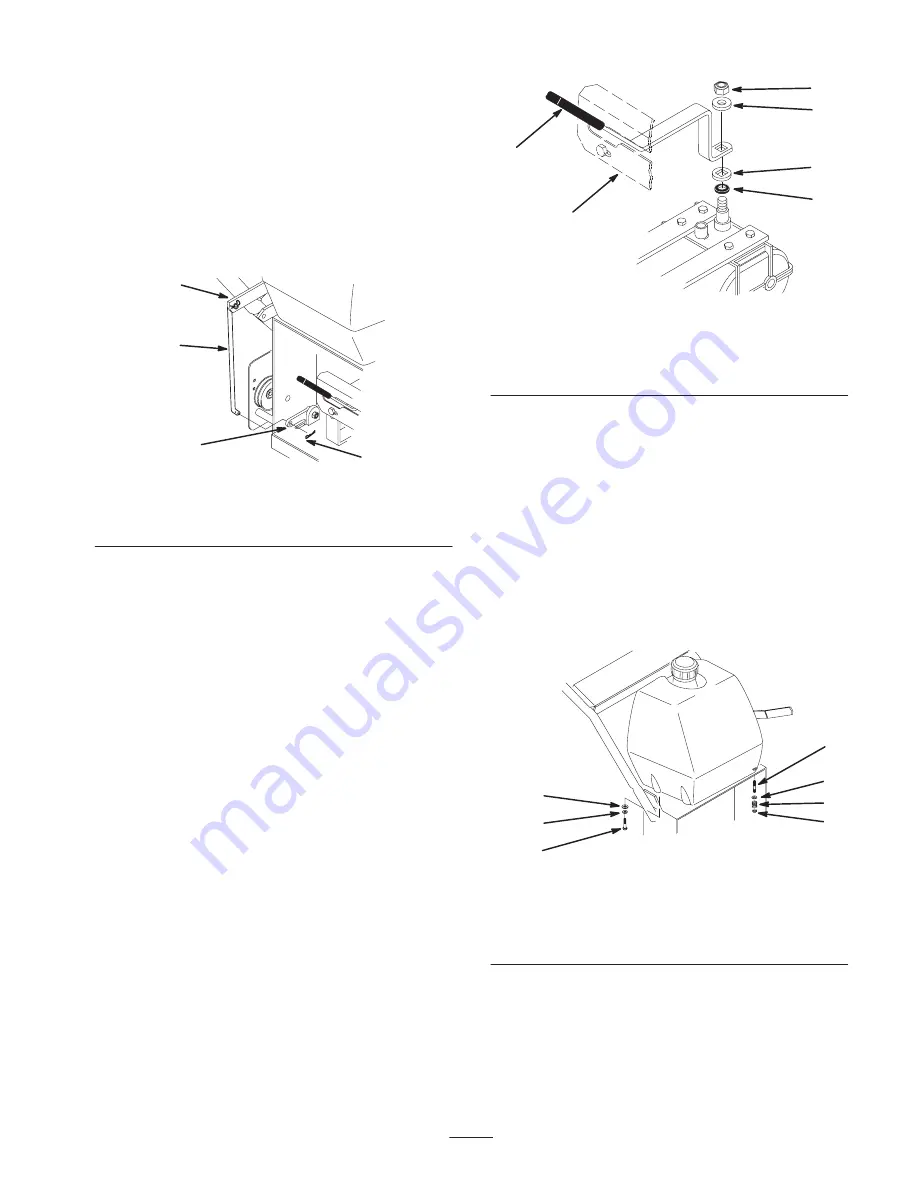
15
Installing the Blade Control
(PTO) Rod
1. Rotate blade control lever (PTO) vertical away from left
handle so rod drops down.
2. Remove hairpin cotters from bottom end of blade
control rod (PTO) (Fig. 9).
3. Secure blade control (PTO) rod through hole in
bellcrank with hairpin cotters (Fig. 9).
m–3783
1
3
2
4
Figure 9
1.
Blade control lever
2.
Blade control rod
3.
Bellcrank
4.
Hairpin cotter
Installing the Shift Lever
1. Remove the locknut (3/8 in.) and spring disk washer
from the stud on top of the transmission.
Note: Do not remove rubber seal washer and square hole
washer from transmission shaft.
2. Slide shift lever through control panel and align
mounting hole in lever with square on transmission
shaft. Secure lever to transmission with previously
removed spring washer and locknut (Fig. 10).
3. Replace the spring washer, dish down and locknut
(Fig. 8).
4. Torque nut to 35 ft. lbs. (47 N
m).
5. Shift lever to second gear and check alignment of lever
in slot of shifter plate. Clearance between top of lever
and the top of the slot should be about equal to the
clearance between bottom of the lever and the bottom
of the slot.
6. If clearance is not correct, remove lever and bend it
slightly to adjust.
Note: Do not bend lever while attached to transmission
shaft or damage may occur.
6
1
m–3772
5
2
3
4
Figure 10
1.
Shift lever
2.
Control panel
3.
Rubber seal washer
4.
Square hole washer
5.
Spring washer
6.
Locknut 3/8
Mounting the Fuel Tank
1. Align fuel tank to top of rear frame and secure fuel tank
right side with 2 bolts (5/16 x 7/8 in.), 2 lock washers
(5/16 in.) and 2 washers (5/16 in.) (Fig. 11).
2. Secure fuel tank left side to frame with 2 studs (5/16 x
7/8 in.), 2 washers (5/16 in.) and 2 locknuts (5/16 in.)
(Fig. 11).
Note: Tighten left side of control panel until it is
completely tight and then unscrew locknut one full turn.
This will allow the spring to work.
m–3771
1
2
3
5
4
6
3
Figure 11
1.
Bolt, 5/8 x 7/8 in.
2.
Lock washer, 5/16 in.
3.
Washer, 5/16 in.
4.
Stud
5.
Spring
6.
Locknut
3. Push fuel line onto fuel tank fitting and secure with
hose clamp (Fig. 12).