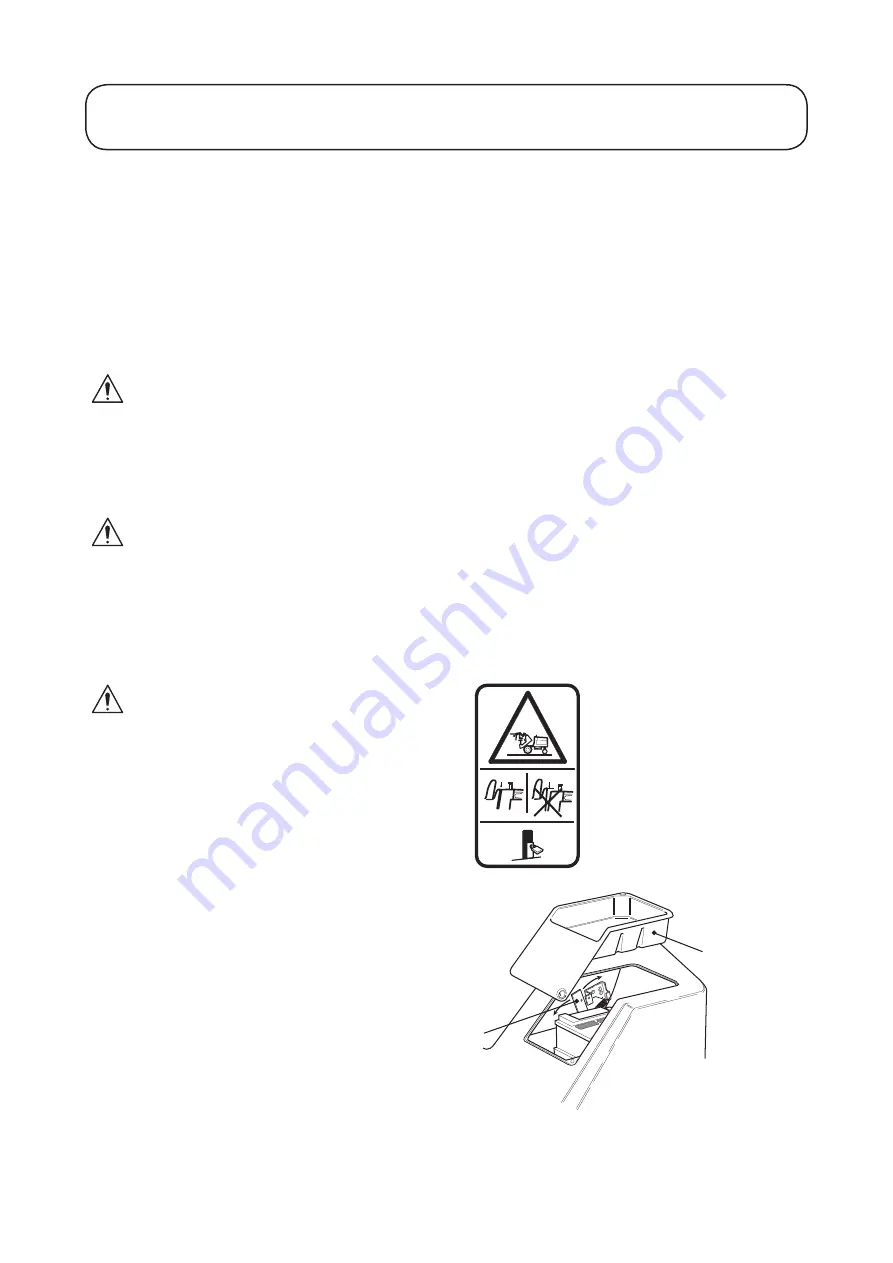
1.29
1.29
Speed Control Pedals
The speed control pedal can be adjusted to provide
two speed ranges.
Securing the speed control cable through hole ‘A’
will provide 0-22 km/hr (0-14 mph) forward and
0-11 km/hr (0-7 mph) reverse. Securing the cable
through hole ‘B’ will provide 0-19 km/hr (0-12
mph) forward and 0-8 km/hr (0-5 mph) reverse.
WARNING: PREVENT ACCIDENTS - En-
sure that the control cable is securely fastened
to the travel control pedal mechanism. Ensure
that both the cable and pedal articulate freely
through their full range of travel and that the
mechanism freely returns to neutral when
released.
WARNING: PREVENT ACCIDENTS - En-
sure that the control cable is correctly routed
underneath the operator platform such that it is
clear of any obstructions and impediments to its
operation.
Operator Platform Latching Mechanism
WARNING: PREVENT ACCIDENTS -
Never operate the mower without first checking
that the operator platform latching mechanism
is fully engaged and in good working order.
Check behind the seat and ensure that the top
of the platform is flush with the top of the fuel
tank. Also check beneath the tool tray and
ensure that the release lever is padlocked in the
correct position.
IMPORTANT: PREVENT DAMAGE -
Engage the parking brake and lower the
cutterheads to the ground. Remove ignition key
and close ignition key and close ignition cover
before raising and lowering the platform.
Releasing the platform:
Release and remove the
tool tray from the left hand side of the platform.
Release the padlock securing the locking latch
handle with key provided. Move the locking latch
handle towards the front of the mower (position A)
until the latch hooks clear the locking bar and raise
the platform. The gas spring will provide
assistance.
OPERATING THE MOWER
2
1
A
B
1. Tool tray
2. Locking latch handle
3. Padlock
A. Release
B. Securing
Summary of Contents for LT3240
Page 2: ......
Page 4: ......
Page 69: ...1 69 1 69 HYDRAULIC CIRCUIT DIAGRAM...
Page 73: ...1 73 1 73 NOTES...
Page 74: ...1 74 1 74 NOTES...
Page 75: ...1 75 1 75 NOTES...
Page 78: ......