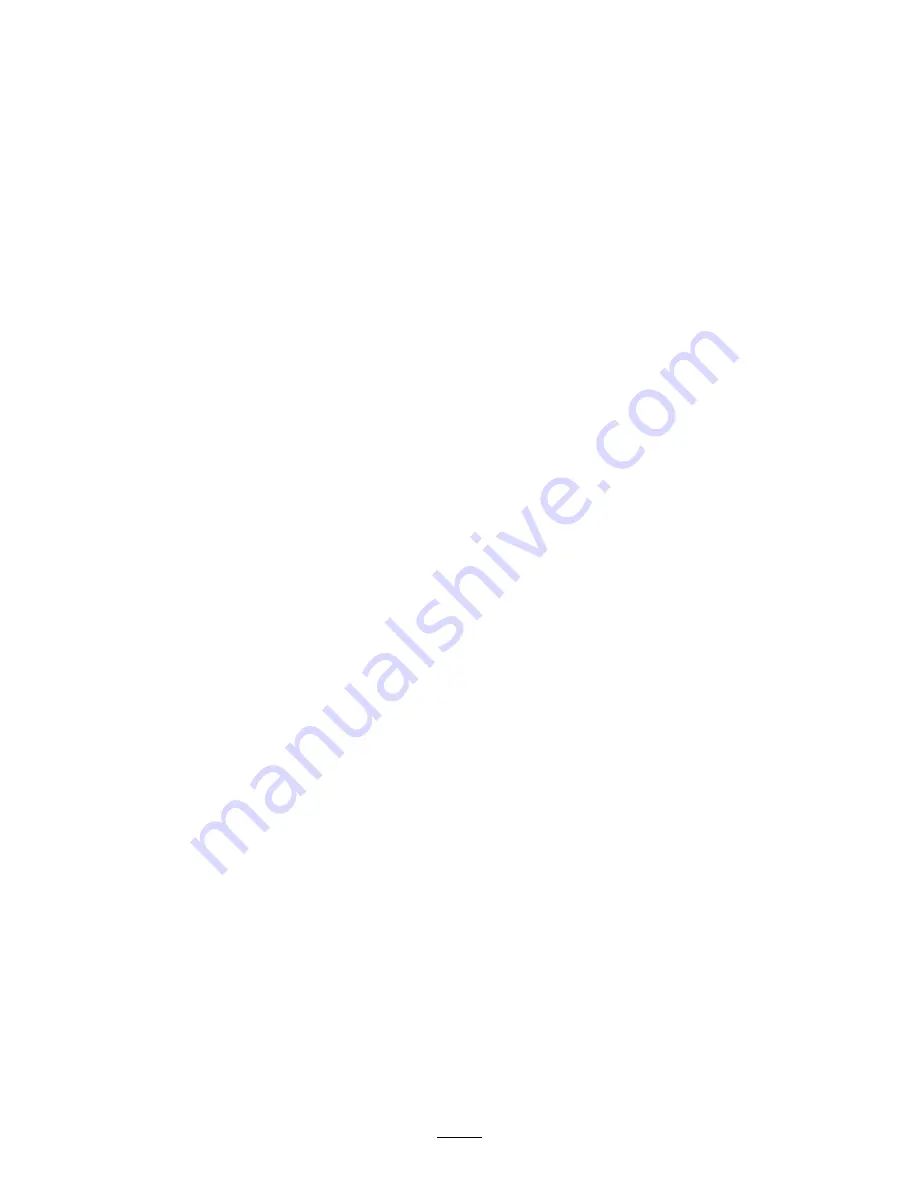
Bleeding the Fuel System
You must bleed the fuel system before starting the engine if
any of the following situations have occurred:
•
Initial start up of a new machine.
•
Engine has ceased running due to lack of fuel.
•
Maintenance has been performed upon fuel system
components; i.e., filter is replaced, separator is serviced,
etc.
1.
Park the machine on a level surface and ensure that the
fuel tank is at least half full.
2.
Open the hood.
3.
Turn the key in the ignition switch to the O
N
position
and crank the engine.
Note:
The mechanical pump sucks fuel out of the
tank, fills the fuel filter and fuel hose, and forces the
air into the engine. Fully purge all the air out of the
system; the engine might fire erratically until all air is
purged out. When all the air is purged and the engine
is running smoothly, run the engine for a few minutes
to ensure that the air is fully purged.
Draining the Fuel Tank
Service Interval:
Every 800 hours
Before storage
Drain and clean the fuel tank if the fuel system becomes
contaminated or if the machine is to be stored for an extended
period. Use clean fuel to flush out the tank.
Checking the Fuel Lines and
Connections
Service Interval:
Every 400 hours/Yearly (whichever comes
first)
Check the fuel lines and connections. Inspect them for
deterioration, damage, or loose connections.
Electrical System
Maintenance
Important:
Before welding on the machine, disconnect
both cables from the battery and the terminal connector
from the alternator to prevent damage to the electrical
system.
Electrical System Safety
•
Disconnect the battery before repairing the machine.
Disconnect the negative terminal first and the positive
last. Connect the positive terminal first and the negative
last.
•
Charge the battery in an open, well-ventilated area, away
from sparks and flames. Unplug the charger before
connecting or disconnecting the battery. Wear protective
clothing and use insulated tools.
Checking the Electrical
System
Service Interval:
Every 500 hours
Inspect all electrical connections and cables and replace any
which are damaged or corroded. Spray a good-quality water
inhibitor onto exposed connections to keep moisture out.
35
Summary of Contents for Groundsmaster 3400
Page 49: ...Notes...
Page 50: ...Notes...