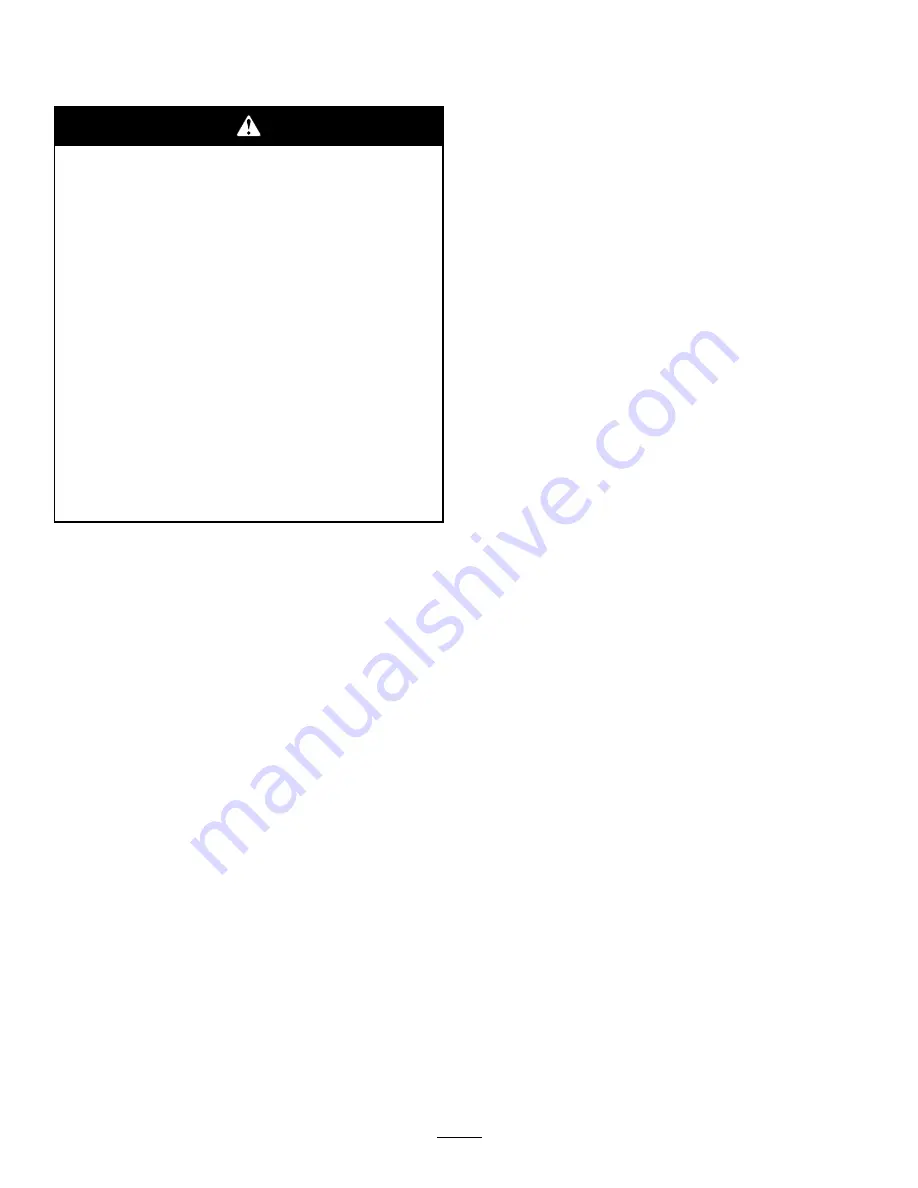
Checking the Hydraulic Lines
and Hoses
Hydraulic fluid escaping under pressure can
penetrate skin and cause injury.
•
Make sure all hydraulic fluid hoses and
lines are in good condition and all hydraulic
connections and fittings are tight before
applying pressure to the hydraulic system.
•
Keep your body and hands away from pin
hole leaks or nozzles that eject high pressure
hydraulic fluid.
•
Use cardboard or paper to find hydraulic
leaks.
•
Safely relieve all pressure in the hydraulic
system before performing any work on the
hydraulic system.
•
Get immediate medical help if fluid is
injected into skin.
Check the hydraulic lines and hoses daily for leaks, kinked
lines, loose mounting supports, wear, loose fittings,
weather deterioration, and chemical deterioration. Make
all necessary repairs before operating.
Storage
If you wish to store the machine for a long period of
time, the following steps should be performed prior to
storage:
1. Remove accumulations of dirt and old grass
clippings. Sharpen the reels and bedknives, if
necessary; refer to the
Cutting Unit Operator’s Manual
.
Use a rust preventive on bedknives and reel blades.
Grease and oil all lubrication points; refer to
Lubrication.
2. Block up the wheels to remove any weight on the
tires.
3. Drain and replace the hydraulic fluid and filter and
inspect the hydraulic lines and fittings. Replace, if
necessary; refer to Changing the Hydraulic Oil and
Filter and Checking the Hydraulic Lines and Hoses.
4. All fuel should be removed from the fuel tank. Run
the engine until it stops from lack of fuel. Replace
the fuel filter; refer to Replacing the Fuel Filter.
5. While the engine is still warm, drain the oil from the
crankcase. Refill it with fresh oil; refer to Changing
the Engine Oil and Filter.
6. Clean dirt and chaff from the cylinder, cylinder head
fins, and blower housing.
7. Remove the battery and charge it fully. Either store
it on the shelf or on the machine. Leave the cables
disconnected if it is stored on the machine. Store
the battery in a cool atmosphere to avoid quick
deterioration of the charge in the battery.
8. If possible, store the machine in a warm, dry location.
48
Summary of Contents for Greensmaster 3250-D
Page 49: ...Schematics Electrical Schematic Rev B 49 ...
Page 50: ...Hydraulic Schematic Rev C 50 ...
Page 51: ...Notes 51 ...