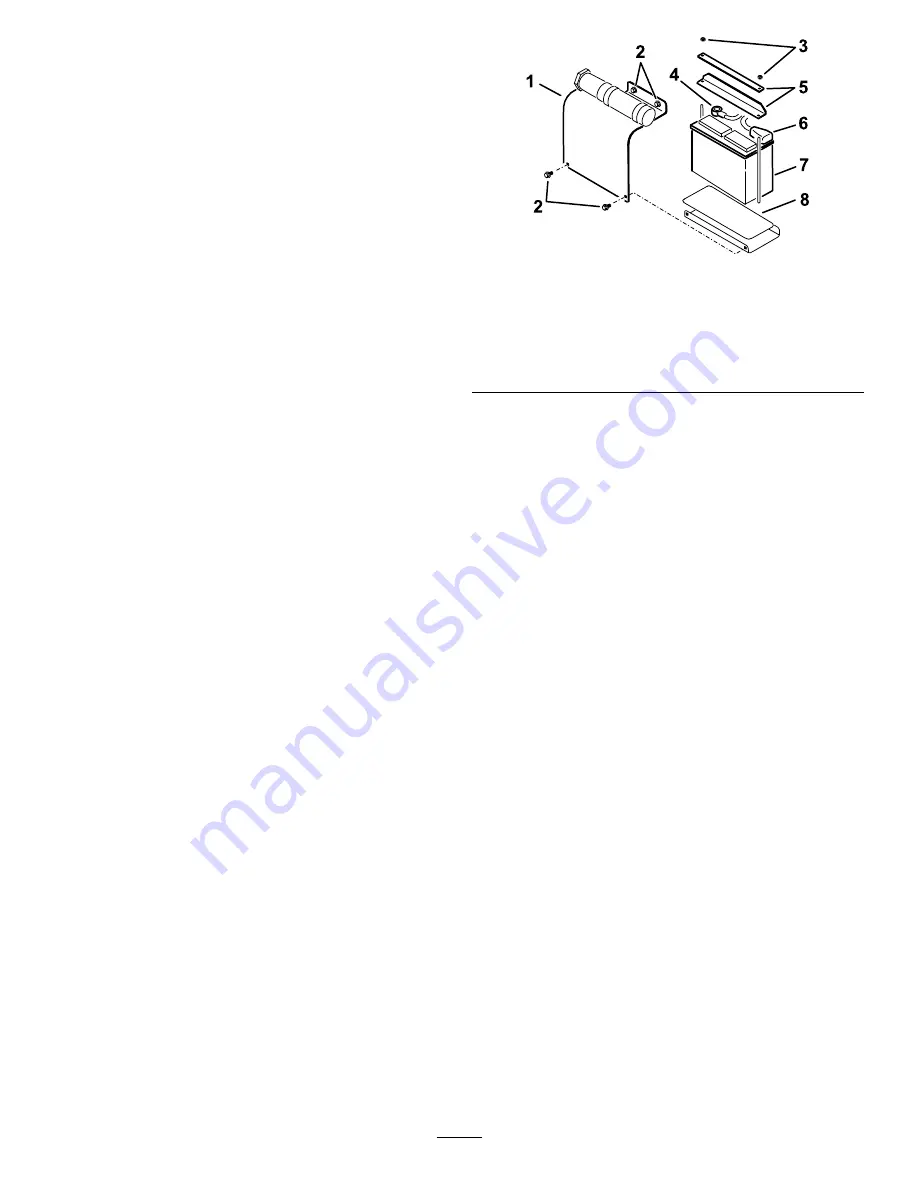
Electrical System
Maintenance
Electrical System Safety
•
Disconnect the battery before repairing the
machine. Disconnect the negative terminal first
and the positive last. Connect the positive terminal
first and the negative last.
•
Charge the battery in an open, well-ventilated
area, away from sparks and flames. Unplug the
charger before connecting or disconnecting the
battery. Wear protective clothing and use insulated
tools.
•
Battery acid is poisonous and can cause burns.
Avoid contact with skin, eyes, and clothing. Protect
your face, eyes, and clothing when working with a
battery.
•
Battery gases can explode. Keep cigarettes,
sparks, and flames away from the battery.
Servicing the Battery
Service Interval:
Every 75 hours—Check the battery
cable connections.
Every 75 hours—Clean the battery.
Always keep the battery clean and fully charged. Use
a paper towel to clean the battery case. If the battery
terminals are corroded, clean them with a solution of
4 parts water and 1 part baking soda. Apply a light
coating of grease to the battery terminals to reduce
corrosion.
Specifications:
12 V, 450 A (cold cranking)
Removing the Battery
1.
Park the machine on a level surface, engage the
parking brake, and lower the loader arms.
2.
Shut off the engine and remove the key.
3.
Remove the battery cover (
)
g230939
Figure 35
1.
Battery cover
5.
Nut
2.
Bolt
6.
Positive battery cable
3.
Battery
7.
Negative battery cable
4.
Bars
8.
Battery pad
4.
Remove the nuts and bars securing the battery
(
).
5.
Disconnect the negative (black) cable to the
negative (-) battery post (
6.
Disconnect the positive (red) cable to the
positive (+) battery post (
7.
Lift the battery off the platform.
33