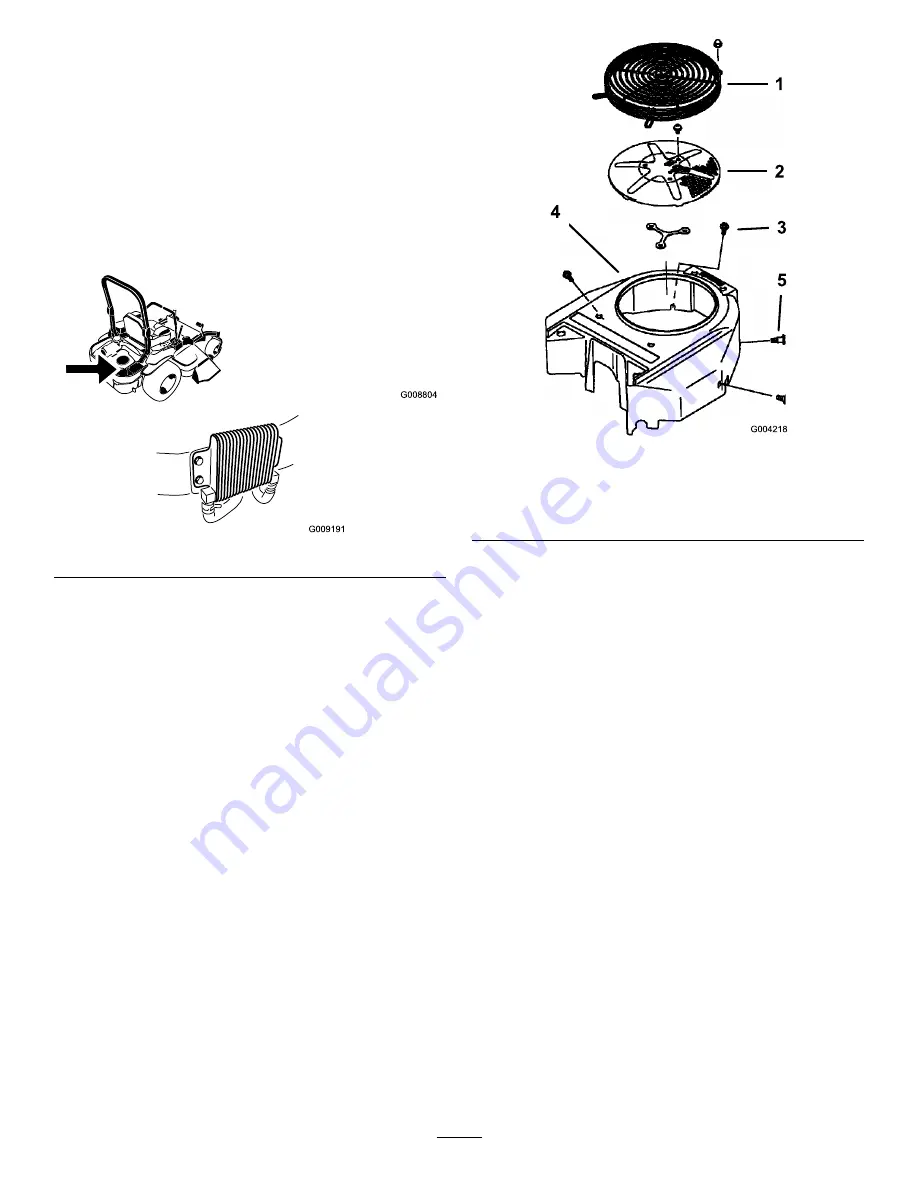
Cooling System
Maintenance
Cleaning the Engine Screen
and Engine Oil Cooler
Service Interval:
Before each use or daily
Remove any build-up of grass, dirt, or other debris from the
oil cooler (Figure 68).
G008804
Figure 68
Before each use remove any build-up of grass, dirt, or
other debris from the engine screen. This will help ensure
adequate cooling and correct engine speed and will reduce
the possibility of overheating and mechanical damage to the
engine (Figure 69).
Cleaning the Engine Cooling
Fins and Shrouds
Service Interval:
Every 100 hours/Yearly (whichever comes
first)
1.
Disengage the PTO and set the parking brake.
2.
Stop the engine, remove the key, and wait for all moving
parts to stop before leaving the operating position.
3.
Remove the air intake screen, recoil starter, and fan
housing (Figure 69).
4.
Clean the debris and grass from the engine parts.
5.
Install air intake screen, recoil starter, and fan housing
(Figure 69).
Figure 69
1.
Engine guard
4.
Fan housing
2.
Engine air intake screen
5.
Screw
3.
Bolt
44
Summary of Contents for 74959
Page 62: ...Schematics G020788 Electrical Schematic Rev A 62 ...
Page 63: ...Notes 63 ...