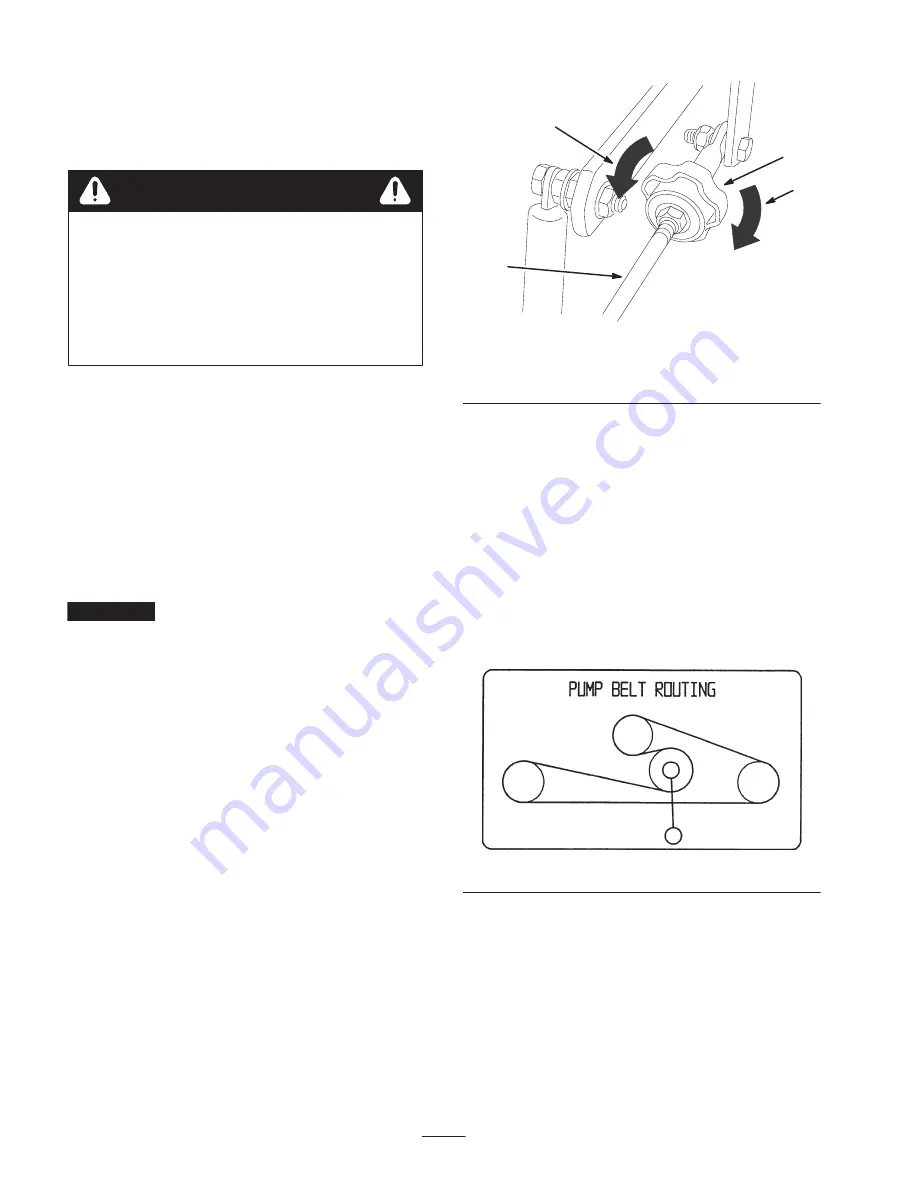
42
5. Open the throttle to fast. Make sure the wheel remains
stopped or slightly creeps in reverse, re-adjust if
necessary.
6. Tighten the locknuts at the ball joints (Fig. 54).
Electrical system will not perform proper safety
shut off with jumper wire installed.
•
Remove jumper wire from wire harness
connector and plug connector into seat switch
when adjustment is completed.
•
Never operate this unit with jumper installed
and seat switch bypassed.
Warning
7. After both pump neutrals are set, shut off the machine.
8. Remove the jumper wire from the wire harness
connector and plug the connector into seat switch.
9. Reinstall the prop rod and lower the seat into position.
10. Remove the jack stands.
Adjusting the Tracking
The right hand pump has a knob for adjusting the
tracking.
Important
Adjust the handle neutral and hydraulic
pump neutral before adjusting the tracking. Refer to
Adjusting the Handle Neutral on page 40 and Adjusting
the Hydraulic Pump Neutral on page 41.
1. Push both control levers forward the same distance.
2. Check if the machine pulls to one side. If it does, stop
the machine and set the parking brake.
3. Tip the seat up to access the tracking knob.
Note: Determine the left and right sides of the machine
from the normal operating position.
4. To make the machine go right, turn the knob towards
the rightside of the machine. Refer to figure 57.
5. To make the machine go left, turn the knob towards
the leftside of the machine. Refer to figure 57.
6. Repeat this adjustment until the tracking is correct.
3
1
2
4
m–6280
Figure 57
1.
Pump rod
2.
Turn this way to track left
3.
Tracking knob
4.
Turn this way to track right
Replacing the Pump Drive Belt
Check pump drive belt for wear after every 50 hours of
operation.
1. Pull the spring loaded idler down and remove traction
belt from the engine and hydro pump pulleys (Fig. 58).
Remove belt between pulleys.
2. Install new belt around engine and hydro pump pulleys
(Fig. 58).
3. Pull spring loaded idler down and align below traction
belt. Release pressure on spring loaded idler (Fig. 58).
Figure 58
Summary of Contents for 74242 Z500 Z Master
Page 6: ...6 ...
Page 7: ...7 Slope Chart ...
Page 8: ...8 ...
Page 11: ...11 107 2102 107 1622 107 1621 106 9969 ...
Page 12: ...12 107 2112 107 1857 107 1860 107 1861 103 2433 ...
Page 13: ...13 106 9989 106 7492 ...
Page 55: ......