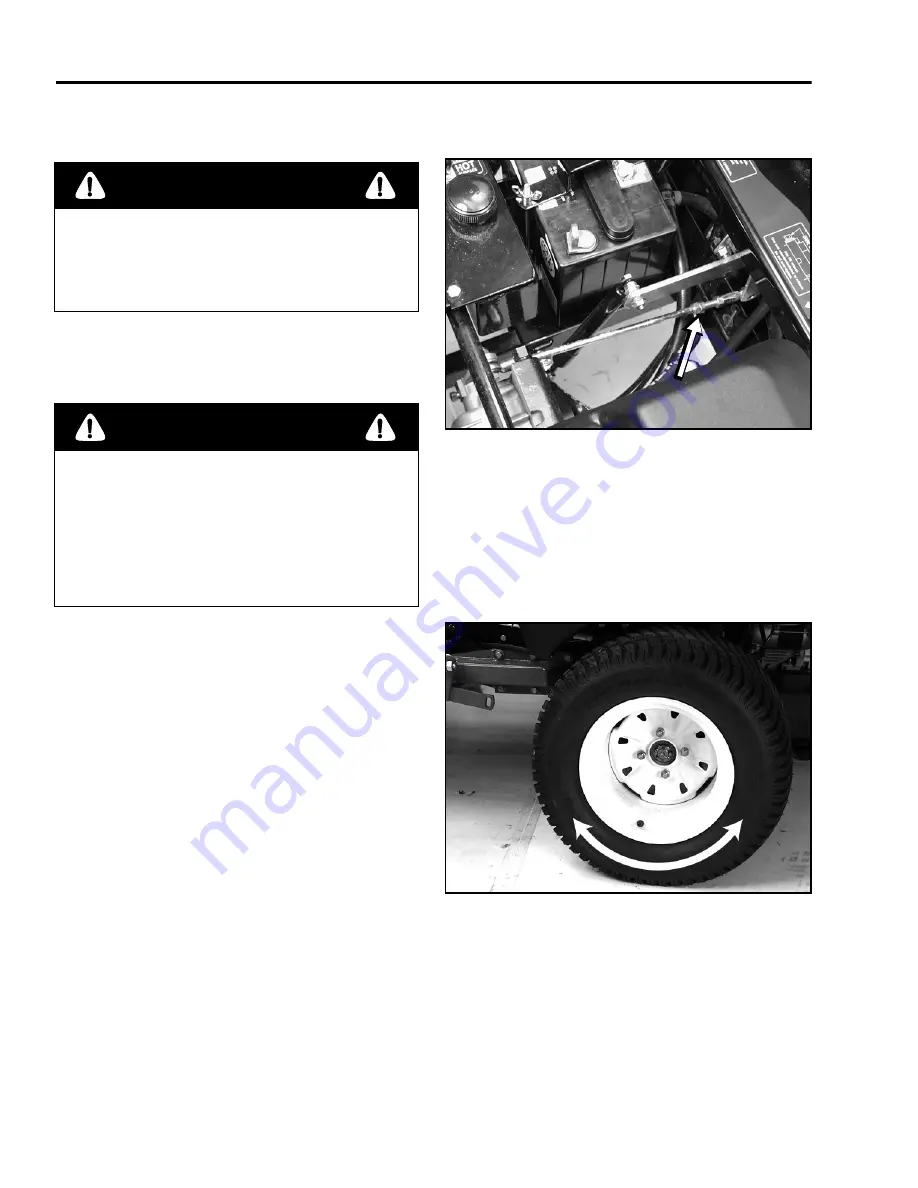
HYDRAULIC SYSTEMS
4 - 4
Mid-Mount Z Service Manual
Refer to "Replacing the Parking Brake and Linkage" on
page 5 - 4
1.
This adjustment must be made with drive wheels
turning. First raise the frame and block up so drive
wheels can rotate freely.
2.
Slide seat forward, disconnect prop rod and tilt
seat fully forward.
3.
Disconnect electrical connector from the seat
safety switch.
Temporarily
install a jumper wire
across terminals in the wiring harness connector.
4.
Loosen locknut at ball joint on pump control rod
(Figure 65).
Figure 65
1023-015
5.
Start engine, open throttle 1/2 way and release
parking brake.
Note:
The front nut of each rod has left-hand threads.
6.
Adjust pump rod length by rotating double nuts on
rod, in the appropriate direction, until wheel is still
or slightly creeps in reverse (Figure 66).
Figure 66
1227-005
7.
Move motion control lever forward and reverse,
then back to neutral. Wheel must stop turning or
slightly creep in reverse.
Note:
Motion control lever must be in neutral while
making any adjustments.
DANGER
Mechanical or hydraulic jacks may fail to
support machine and cause a serious injury.
• Use jack stand when supporting machine.
• Do not use hydraulic jacks.
WARNING
Engine must be running so motion control
adjustment can be performed. Contact with
moving parts or hot surfaces may cause
personal injury.
Keep hands, feet, face, clothing and other body
parts away from rotating parts, muffler and other
hot surfaces.
Summary of Contents for 74161
Page 4: ...Mid Mount Z Service Manual ...
Page 11: ...vi Mid Mount Z Service Manual THIS PAGE INTENTIONALLY LEFT BLANK ...
Page 15: ...1 4 Mid Mount Z Service Manual THIS PAGE INTENTIONALLY LEFT BLANK ...
Page 27: ...2 12 Mid Mount Z Service Manual THIS PAGE INTENTIONALLY LEFT BLANK ...
Page 39: ...3 12 Mid Mount Z Service Manual THIS PAGE INTENTIONALLY LEFT BLANK ...
Page 75: ...6 14 Mid Mount Z Service Manual THIS PAGE INTENTIONALLY LEFT BLANK ...
Page 76: ...Mid Mount Z Service Manual 7 1 ELECTRICAL SYSTEMS ...
Page 79: ...ELECTRICAL SYSTEMS 7 4 Mid Mount Z Service Manual ...
Page 80: ...Mid Mount Z Service Manual 7 5 ELECTRICAL SYSTEMS Models 74211 74212 Start Circuit ...
Page 81: ...ELECTRICAL SYSTEMS 7 6 Mid Mount Z Service Manual Models 74211 74212 Run Circuit ...
Page 82: ...Mid Mount Z Service Manual 7 7 ELECTRICAL SYSTEMS ...
Page 83: ...ELECTRICAL SYSTEMS 7 8 Mid Mount Z Service Manual Models 74218 74219 Start Circuit ...
Page 84: ...Mid Mount Z Service Manual 7 9 ELECTRICAL SYSTEMS Models 74218 74219 Run Circuit ...
Page 85: ...ELECTRICAL SYSTEMS 7 10 Mid Mount Z Service Manual ...
Page 86: ...Mid Mount Z Service Manual 7 11 ELECTRICAL SYSTEMS ...
Page 87: ...ELECTRICAL SYSTEMS 7 12 Mid Mount Z Service Manual ...
Page 88: ...Mid Mount Z Service Manual 7 13 ELECTRICAL SYSTEMS ...
Page 89: ...ELECTRICAL SYSTEMS 7 14 Mid Mount Z Service Manual ...
Page 90: ...Mid Mount Z Service Manual 7 15 ELECTRICAL SYSTEMS ...
Page 91: ...ELECTRICAL SYSTEMS 7 16 Mid Mount Z Service Manual ...
Page 92: ...Mid Mount Z Service Manual 7 17 ELECTRICAL SYSTEMS ...
Page 93: ...ELECTRICAL SYSTEMS 7 18 Mid Mount Z Service Manual ...
Page 94: ...Mid Mount Z Service Manual 7 19 ELECTRICAL SYSTEMS ...
Page 111: ...7 36 Mid Mount Z Service Manual THIS PAGE INTENTIONALLY LEFT BLANK ...
Page 112: ......
Page 113: ...492 4758 ...