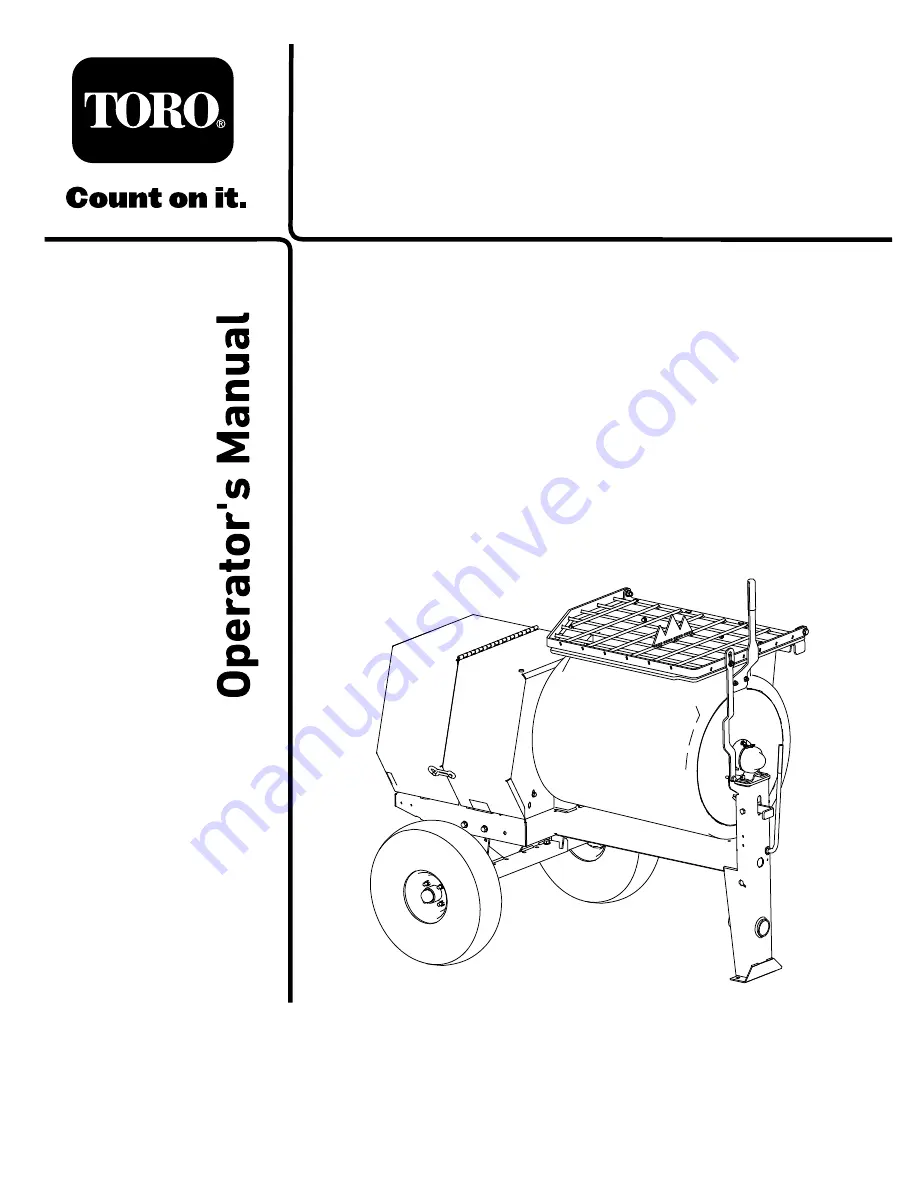
Form No. 3422-822 Rev A
MMX-658K-P, MMX-858K-P, and
MMX-858H-P Mortar Mixers
Model No. 60217—Serial No. 400000000 and Up
Model No. 60217C—Serial No. 400000000 and Up
Model No. 60221—Serial No. 400000000 and Up
Model No. 60221C—Serial No. 400000000 and Up
Model No. 60221HD—Serial No. 400000000 and Up
Register at www.Toro.com.
Original Instructions (EN)
*3422-822* A
Summary of Contents for 60217
Page 10: ...decal137 7491 137 7491 1 Read the Operator s Manual 10 ...
Page 52: ...Notes ...
Page 53: ...Notes ...
Page 54: ...Notes ...