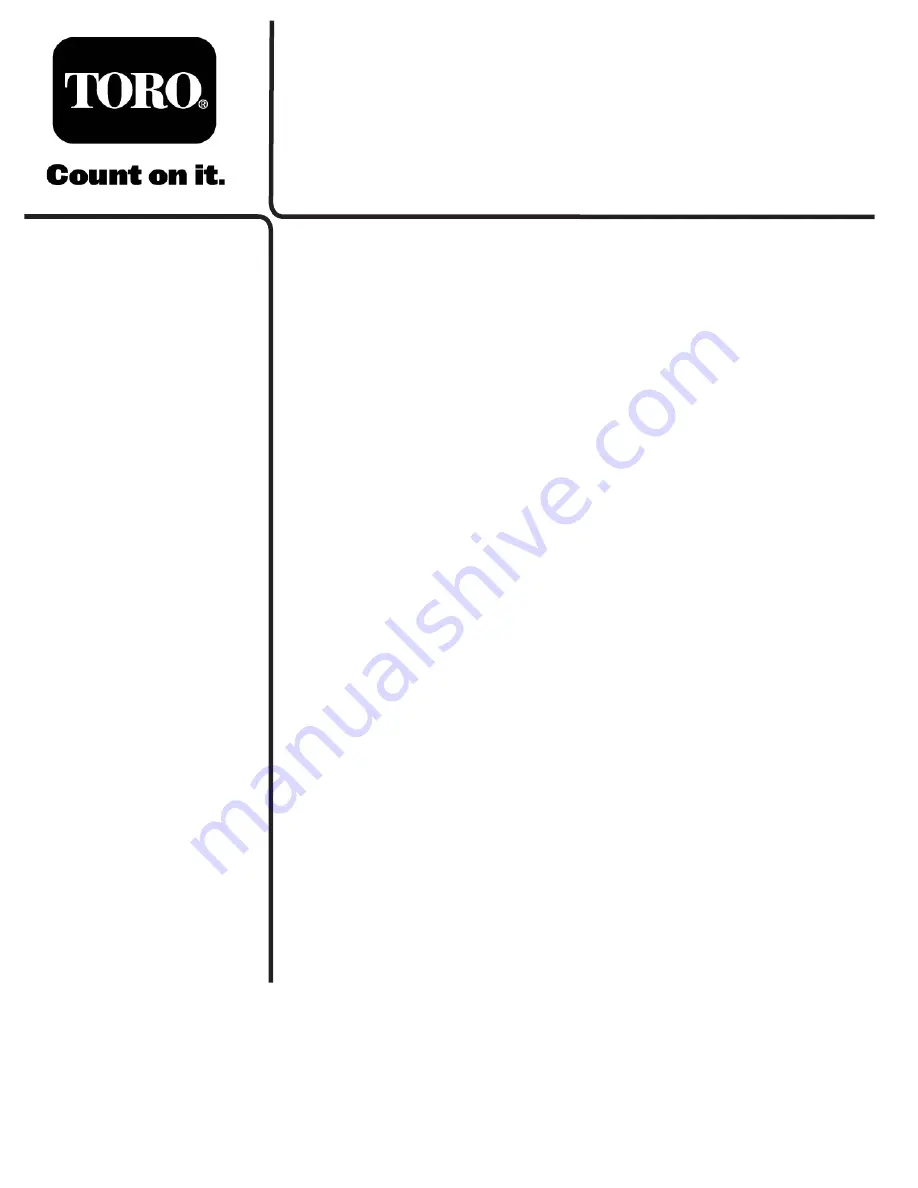
Form No. 3364-606 Rev A
MH-400 Material Delivery Unit
Model No. 44930--Serial No. 310000001 and Up
Model No. 44931--Serial No. 310000001 and Up
Model No. 44933--Serial No. 310000001 and Up
Model No. 44934--Serial No. 310000001 and Up
Model No. 44937
Model No. 44938
Register your product at www.Toro.com
Original Instructions (EN)
Operator
’s Manual
Summary of Contents for 44931
Page 2: ......
Page 58: ...Page 52 Troubleshooting MH 400 Maintenance Record Service Performed Date Notes...
Page 59: ...Troubleshooting Page 53...
Page 60: ......