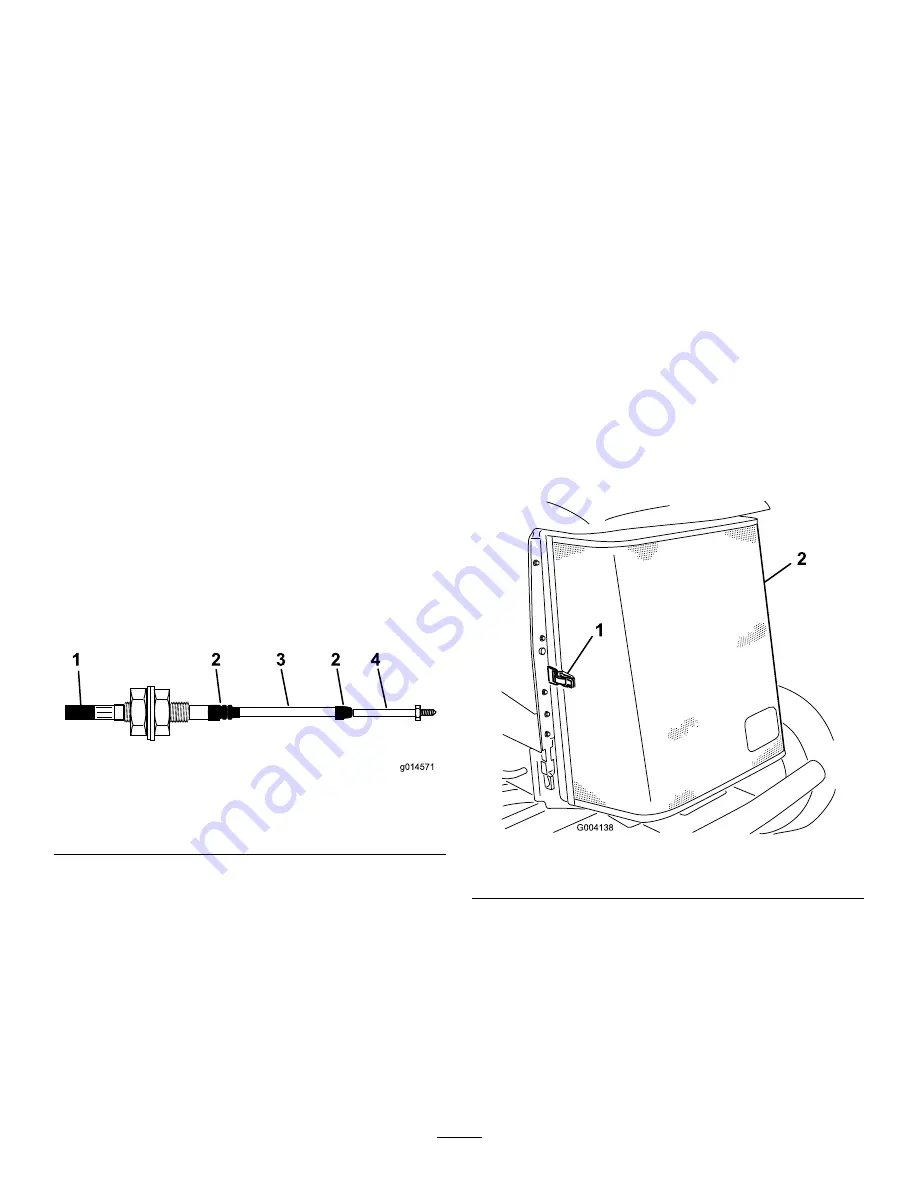
Inspecting the Transmission
Control Cable and Operating
Mechanism
Service Interval:
Every 250 hours
Check the condition and security of the cable and operating
mechanism at the speed-control pedals and transmission
pump ends.
•
Remove buildup of dirt, grit and other deposits.
•
Ensure that the ball joints are securely anchored and
check that the mounting brackets and cable anchors are
tight and free from cracks.
•
Inspect end fittings for wear, corrosion, broken springs,
and replace if necessary.
•
Ensure that the rubber seals are correctly located and are
in good condition.
•
Ensure that the articulating sleeves supporting the inner
cable are in good condition and firmly attached to the
outer cable assembly at the crimped connections. If there
are any signs of cracking or detachment install a new
cable immediately.
•
Check that sleeves, rods, and inner cable are free from
bends, kinks, or other damage. If they are not, install a
new cable immediately.
•
With the engine shut off, operate the pedal controls
through the entire range and ensure that the mechanism
moves smoothly and freely to the neutral position without
sticking or hanging up.
g014571
1 2 3 2 4
Figure 58
1.
Outer cover
3.
Sleeve
2.
Rubber seal
4.
Rod end
Cooling System
Maintenance
Removing Debris from the
Cooling System
Service Interval:
Before each use or daily
Every 100 hours
Every 2 years
Note:
To prevent the engine from overheating, the radiator
and oil cooler must be kept clean. Normally, check daily and,
if necessary, clean any debris off these parts. However, it is
necessary to check and clean more frequently in extremely
dusty and dirty conditions.
1.
Turn the engine off and remove the key from the
ignition switch.
2.
Thoroughly clean all debris out of the engine area.
3.
Unlatch the clamp and pivot open the rear screen
(
).
Figure 59
1.
Rear screen latch
2.
Rear screen
4.
Clean the screen thoroughly with compressed air.
5.
Pivot the latches inward to release the oil cooler (
45