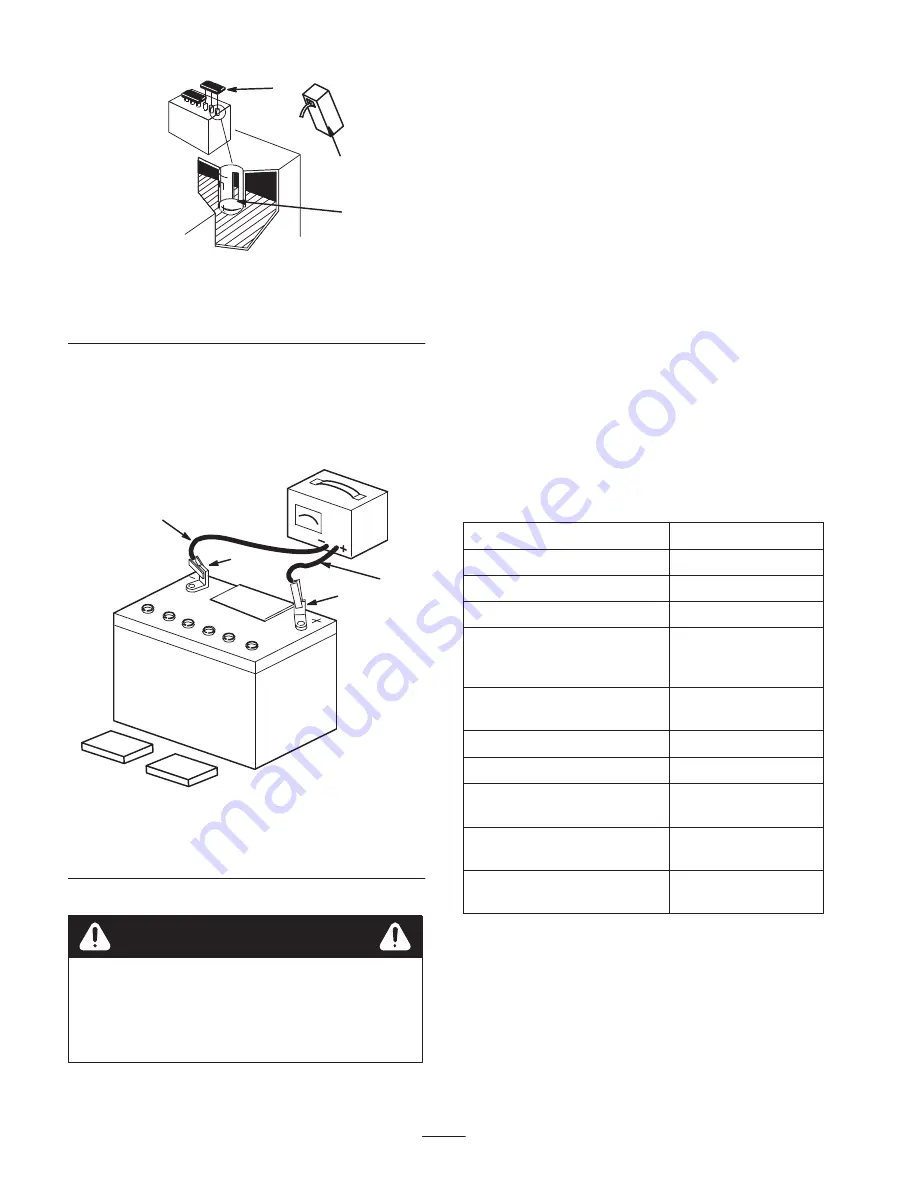
10
1
2
3
1262
Figure 4
1.
Filler caps
2.
Electrolyte
3.
Lower part of the tube
5. Leave the covers off and connect a 3 to 4 amp battery
charger to the battery posts (Fig. 5).
6. Charge the battery at a rate of 4 amperes or less for 4
hours (12 volts).
4
1
2
3
1254
Figure 5
1.
Positive post
2.
Negative post
3.
Charger red (+) wire
4.
Charger black (–) wire
Charging the battery produces gasses that can
explode.
Never smoke near the battery and keep sparks
and flames away from battery.
Warning
7. When the battery is fully charged, disconnect the
charger from the electrical outlet and from the
negative and positive battery posts (Fig. 5).
8. Slowly pour electrolyte into each cell until the level is
once again up to the upper line on the battery case
(Fig. 4) and install covers.
9. Install the battery into the chassis (Fig. 3).
10. Secure the battery in the chassis with the battery
clamp, strip, and wing nut (Fig. 3).
11. Using the bolt and wing nut supplied with the battery,
connect the positive (red) cable to the positive (+)
battery post (Fig. 3). Slide the rubber cover over the
battery post.
12. Using the bolt and wing nut supplied with the battery,
connect the negative (black) cable to the negative (–)
battery post (Fig. 3).
Note: Ensure that the battery cables do not contact any
sharp edges or each other.
Specifications
Overall width
40.5 inches (103 cm)
Overall length
60.0 inches (152 cm)
Overall height
49.0 inches (125 cm)
Weight
1565 lbs (710 kg)
Rated operating capacity (with
200 lb operator and std.
bucket)
515 lbs (234 kg)
Tipping capacity (with 200 lb
operator and st. bucket)
l030lbs (467kg)
Wheelbase
28 inches (71 cm)
Dump height (with std. bucket)
47 inches (120 cm)
Reach—fully raised (with std.
bucket)
26.0 inches (66
cm)
Height to hinge pin (std bucket
in highest position)
66.0 inches (168 cm)
Engine
Kohler Command Pro,
20 HP, V–Twin
Specifications and design are subject to change without
notice.
Summary of Contents for 22311
Page 6: ...6 Slope Chart...