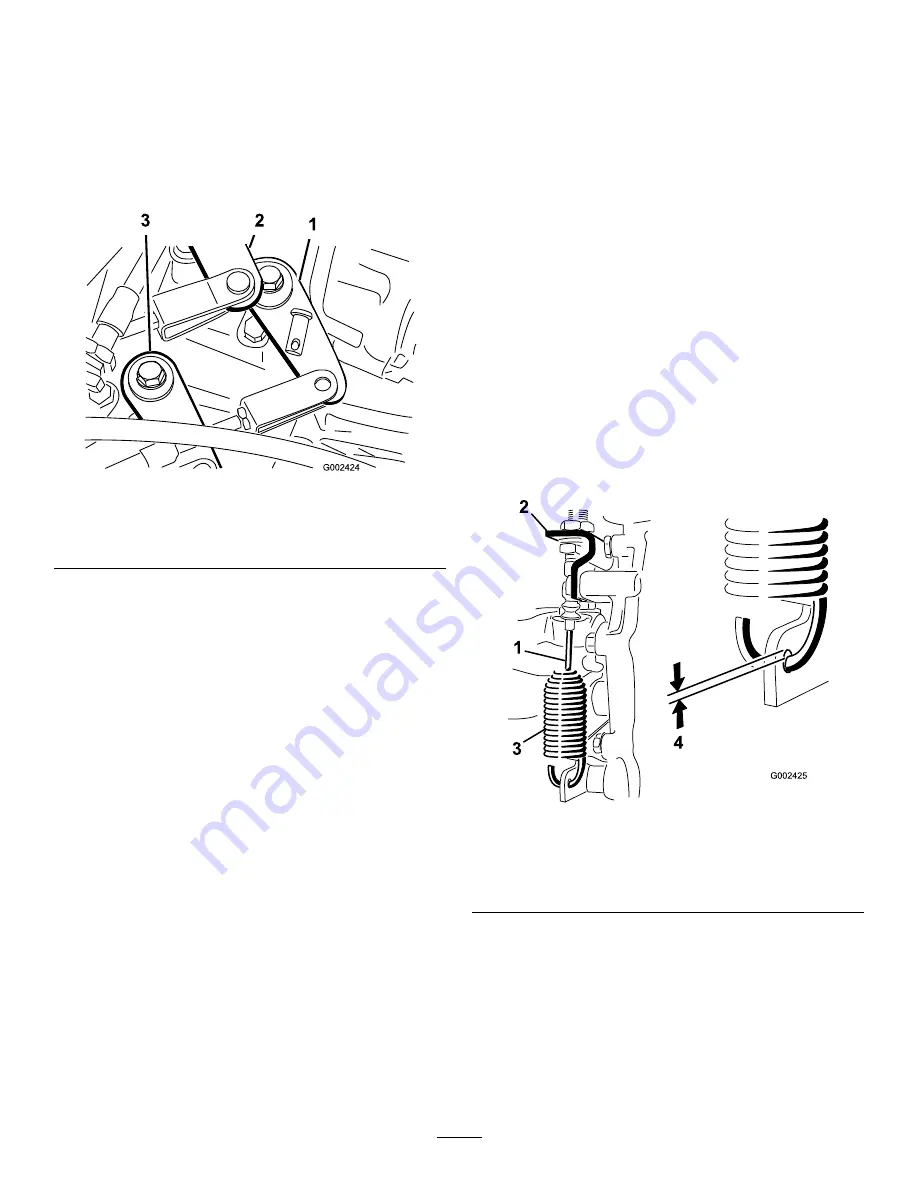
Adjusting the Shift Cables
Service Interval:
After the first 10 hours
Every 200 hours
1.
Move the shift lever to the N
EUTRAL
position.
2.
Remove the clevis pins securing the shift cables
to the transaxle-shift arms (
).
g002424
Figure 44
1.
Shift arm (1st to reverse)
3.
Shift arm (High to low)
2.
Shift arm (2nd to 3rd)
3.
Loosen the clevis jam nuts and adjust each
clevis, so that the cable free play is equal
forward and backward relative to the hole in the
transaxle-shift arm (with the transaxle lever free
play taken up in the same direction).
4.
Install the clevis pins and tighten the jam nuts
when finished.
Adjusting the High-Low
Cable
Service Interval:
Every 200 hours
1.
Remove the clevis pin securing the high-low
cable to the transaxle (
2.
Loosen the clevis jam nut and adjust the clevis
so that the clevis hole aligns with the hole in the
transaxle bracket.
3.
Install the clevis pin and tighten the jam nut
when finished.
Adjusting Differential-Lock
Cable
Service Interval:
Every 200 hours
1.
Move the differential-lock lever to the O
FF
position.
2.
Loosen the jam nuts securing the differential-lock
cable to the bracket on the transaxle (
).
g002425
Figure 45
1.
Differential-lock cable
3.
Spring
2.
Transaxle bracket
4.
0.25 to 1.5 mm (0.01 to
0.06 inch) gap
3.
Adjust the jam nuts to obtain a 0.25 to 1.5 mm
(0.01 to 0.06 inch) gap between the spring hook
and the OD of the hole in the transaxle lever.
4.
Tighten the jam nuts when finished.
47
Summary of Contents for 07385TC Workman HDX-D
Page 39: ...g010359 Figure 32 39...