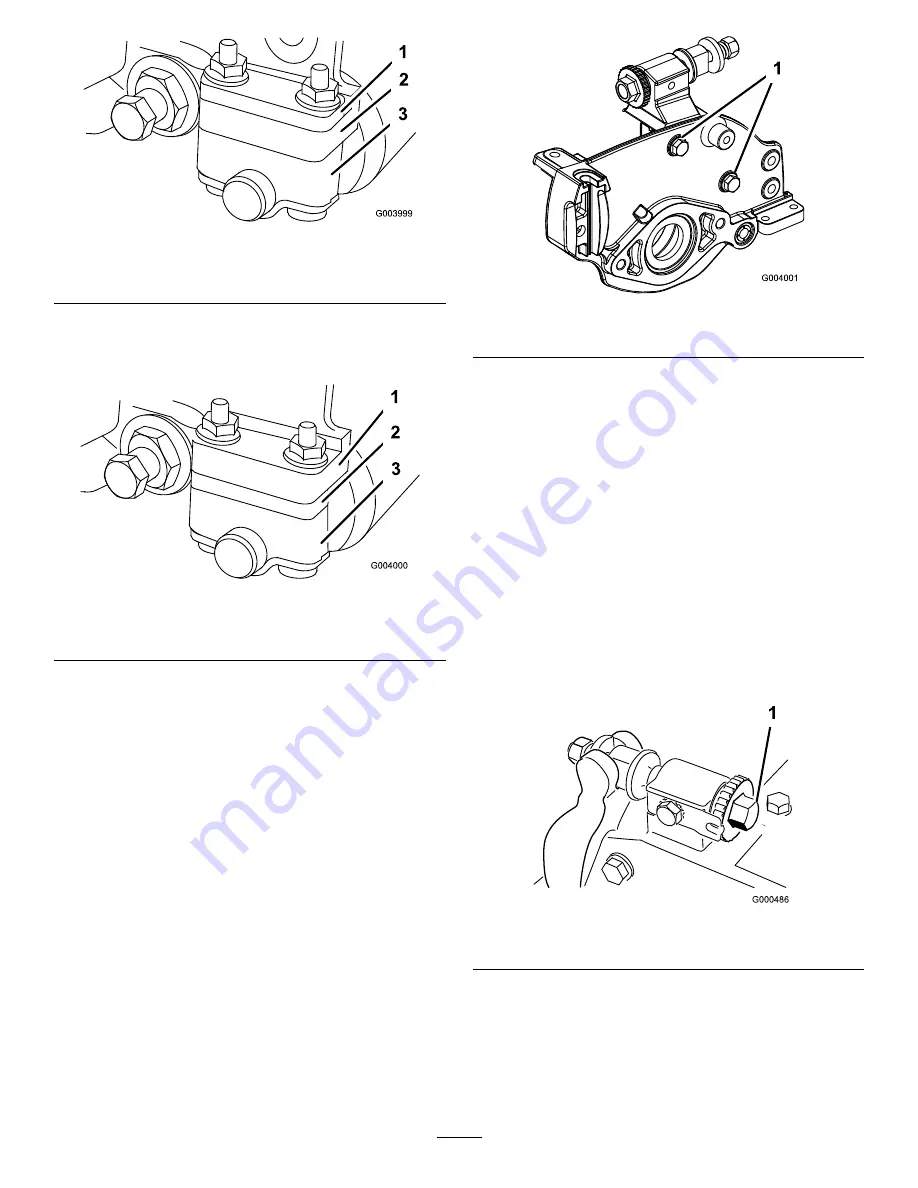
Figure 51
1.
Spacer
3.
Roller bracket
2.
Sideplate mounting flange
•
Position the spacer below the sideplate mounting
flange when height of cut settings range from
1/8" to 1" (Figure 52).
Figure 52
1.
Sideplate mounting flange
3.
Roller bracket
2.
Spacer
2. To adjust rear roller proceed as follows:
•
Raise rear of cutting unit and place a block under
bedknife.
•
Remove (2) nuts securing each roller bracket and
spacer to each sideplate mounting flange.
•
Lower roller and screws from sideplate mounting
flanges and spacers.
•
Place spacers onto screws on roller brackets.
•
Re-secure roller bracket and spacers to underside
of sideplate mounting flanges with nuts
previously removed.
3. Verify that the bedknife to reel contact is correct. Tip
mower to expose front and rear rollers and bedknife.
Note:
The position of the rear roller to the
reel is controlled by the machining tolerances of
the assembled components and paralleling is not
required. A limited amount of adjustment is possible
by setting the cutting unit on a surface plate and
loosening the sideplate mounting bolts (Figure 53).
Adjust and re-tighten bolts.
Figure 53
1.
Sideplate mounting bolts
Important:
Whenever the cutting unit has to
be tipped to expose bedknife/reel, prop up rear
of cutting unit to make sure nuts on back end
of bedbar adjusting screws are not resting on
work surface.
Adjusting the Bedknife to the
Reel
Bedknife to reel adjustment is accomplished by
loosening or tightening bedbar adjusting screws, located
on top of mower.
1. Position machine on a flat, level work surface.
2. Make sure reel contact is removed by turning bedbar
adjusting screws counterclockwise (Figure 54).
Figure 54
1.
Bedbar adjusting screw
3. Tilt mower on back to expose bedknife and reel.
4. At one end of reel, insert a long strip of newspaper
between reel and bedknife (Figure 55). While slowly
rotating reel forward, turn bedbar adjusting screw
clockwise (on same end of reel) (Figure 54), one click
at a time, until paper is pinched lightly, when inserted
32
Summary of Contents for 04030
Page 39: ...Notes 39 ...