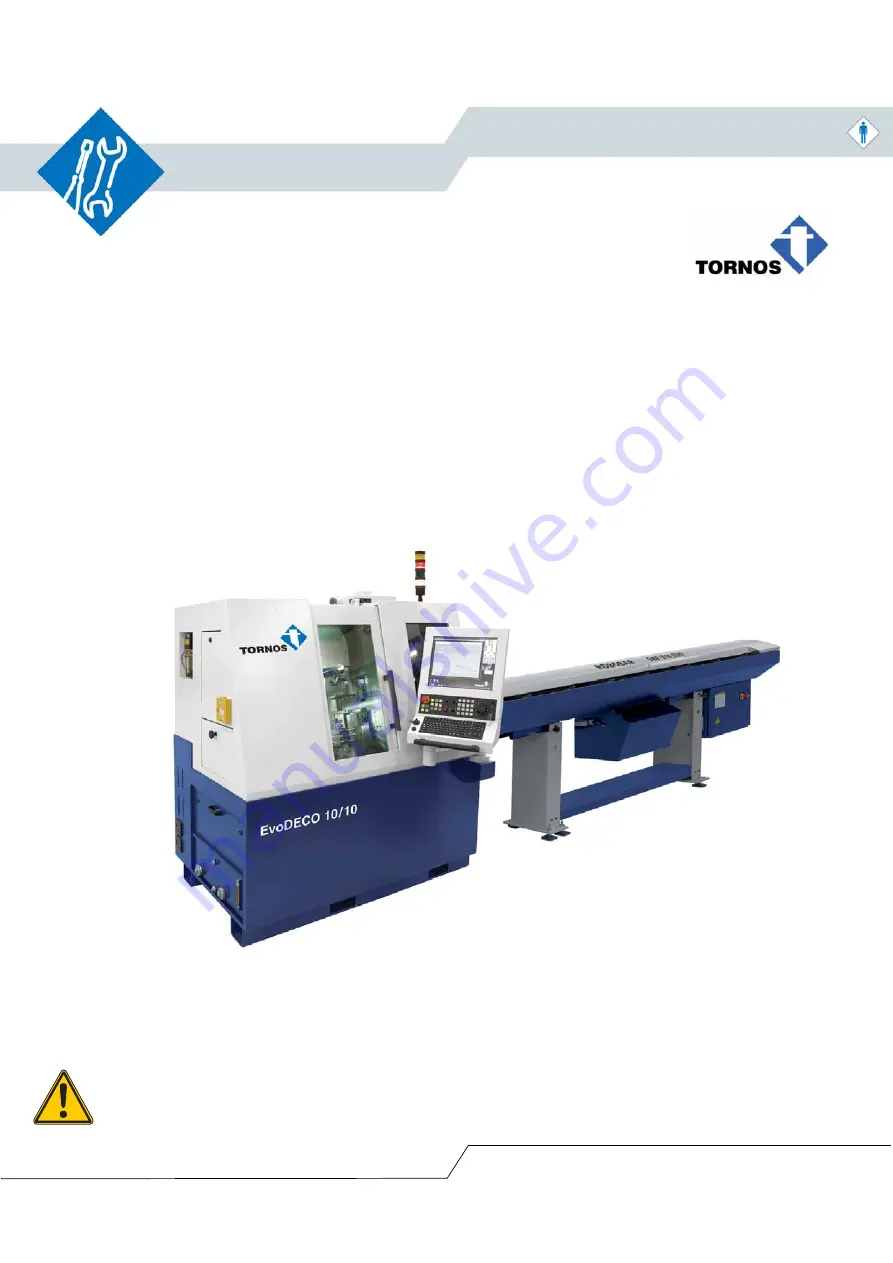
EvoDECO 10/10 & 10/8
INSTRUCTION MANUAL
ENGLISH VERSION TRANSLATED FROM THE ORIGINAL VERSION
TORNOS SA CH-2740 MOUTIER
http://www.tornos.ch
Ref.
: 298061_fr
e
d in S
w
itz
e
rland
-
Co
py
right
© 19
99-
201
2
Attention!
Read this precautions before,
all users must read the instruction manual and pay
particular attention to the "SAFETY INSTRUCTIONS" !
Keep this document for future reference.
Summary of Contents for EvoDECO 10/10
Page 2: ......
Page 6: ...298061_en 07 12 Instruction Manual EvoDECO 10 10 10 8 ...
Page 21: ...Instruction Manual EvoDECO 10 10 10 8 1 Installation conditions 298061_en 07 12 1 13 Fig 7 ...
Page 23: ...Instruction Manual EvoDECO 10 10 10 8 2 Installation 298061_en 07 12 2 1 2 Installation ...
Page 25: ...Instruction Manual EvoDECO 10 10 10 8 2 Installation 298061_en 07 12 2 3 Fig 1 ...