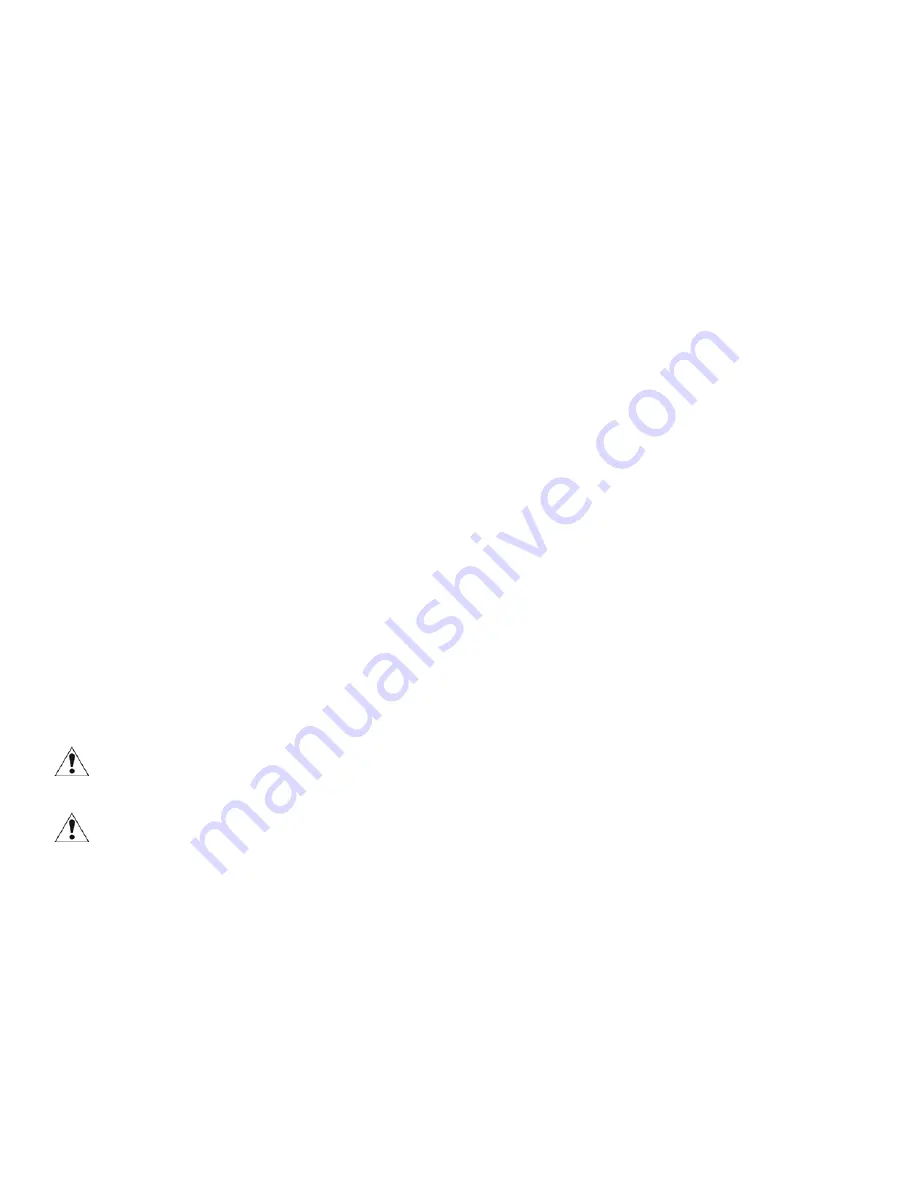
9
SET UP INSTRUCTION
Filter Installation
There are three filters in the Pro 500/750: inlet filter, main filter and pump protection filter. It is imperative to
the efficient operation of the Pro 500/750 that the filters are installed properly.
Pump Protection Filter – Position on brass fitting on the filter mound. Slide it down.
Main Filter – Wet the rim of the filter and position it on the filter mound. (white plastic disc) Twist and slide
over the mound by pushing downward.
Inlet Filter – Position on top of the tank.
OPERATING INSTRUCTIONS
1. Remove lid and inlet filter.
2. Check main filter. Make sure the main filter is installed snugly.
3. Fill tank with water to a desired level. Use solution level gauge.Maximum water temperature to be used
is 130 degrees F.
4. Add in-tank cleaner per chemical label use instructions. In addition, pre-spraying is often desirable
and will assist in producing the fastest and best cleaning results. See chemical product labels for more
information.
Note: Use caution when moving machine (especially on inclines) with fluid in the tank to prevent fluid from
entering vacuum standpipe at back of machine tank and flooding the vacuum.
The user MUST ONLY use chemicals that have been speically formulated to work with CFR technology
machines.
5. Prime pump by re-circulating fluid through priming hose included for 15/30 seconds. Re-circulating the
fluid primes the pump and expels trapped air from the system.
6. Replace inlet filter and lid
7. Attach hose assembly to machine. Connect fluid hose to the quick-disconnect found on the front of
machine.
8. Attach the desired tool to the valve end of the hose assembly.
9. Close tank cover lid, turn on vacuum and pump switches.
10. Clean surface with tool attached to hose assembly.
11. During the cleaning process, the fluid level will be reduced and the lower level float switch will shut off
the pump. When the pump shuts off, drain and rinse tank, rinse main filter, refill with fresh water and
cleaning chemical, and continue cleaning.
CAUTION! When cleaning, monitor foam in the machine’s tank. Areas cleaned with other cleaning
equipment or chemicals may cause excessive foam to collect in the tank.
WARNING! EXCESSIVE FOAM IN THE TANK MAY CAUSE VACUUM MOTOR FLOODING AND MACHINE
DAMAGE.
Pour one to two ounces of Defoam directly into the tank or into the vacuum hose while the vacuum is
running. Defoam has been speically formulated to work with this machine.
When finished cleaning, perform the daily maintenance procedure. Be sure that all filters are cleaned
thoroughly and replaced in machine. Leave lid off for drying.