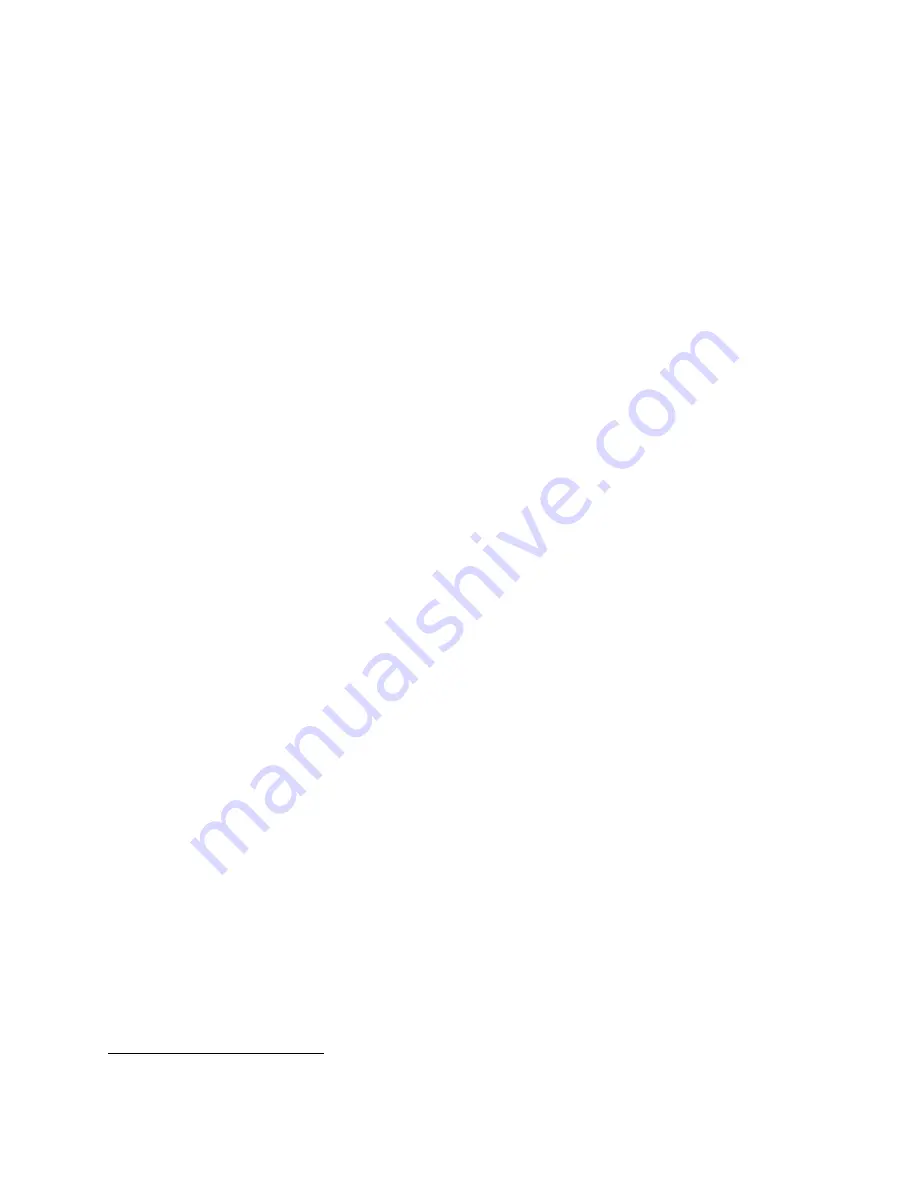
CNC SCOPE
UM10138_0712A
14
Tormach® CNC Scanner
5.
Camera Settings. Adjusts camera settings (See section 5.4).
6.
Quit. Exits CNC Scope.
7.
Record Scope Setting. You can save up to three scope settings that can be recalled later.
8.
Adjust Crosshair Size. Changes the size of the crosshair circle. This is helpful for centering
over a hole.
9.
Pan Crosshairs. Moves Crosshairs with respect to center of image.
4.3
Centering the Scope
If you intend to use CNC Scope as an optical centering device the following procedure is
recommended for the most accurate results.
1.
Using the machine, drill a hole in a piece of stock with a good sharp drill bit (a .25 drill bit works
well). Then set the X and Y coordinates to zero.
2.
Mount the camera into the camera housing, using the bands provided.
3.
Insert the 4 set screws into the 4 locations on the camera housing.
4.
Using an Allen wrench, tighten or loosen the screws until the camera appears to be centered in
the camera housing.
5.
Mount the camera housing in the machine spindle.
6.
Make sure the machine is at the zero coordinate for X and Y, then start the CNC Scope Plug-in
within the Mach 3 control software.
7.
Move the Z axis of the machine close to the surface of the material that you drilled a hole into,
and focus the camera using the focus wheel.
8.
Using the set screws in the side of the housing adjust the screws in or out to place the red
crosshairs as close to the center of the hole as you can.
9.
Using the CNC Scope software, increase or decrease the diameter of the circle on the
crosshairs to closely match the drilled holes diameter.
10.
Using your hand slowly rotate the machine spindle while watching the screen. If it appears that
the red circle rotates concentrically around the edge of the drilled hole, then the camera is
centered; otherwise continue to adjust the screws until the circles are concentric.
To test your centering, move the machine away from the drilled hole. Then, by using the machine jog
controls or MDI interface move the crosshairs back over the drilled hole until you think it is over center
and check your X and Y position. If it is close to zero, the scope is centered. If it is not very close, go
back to step 4.
Please be aware that any further focusing or refocusing of the scope after completing the alignment
procedure can have an adverse effect on its performance as an Optical Centering device. For the most
accurate results, the centering procedure should be repeated for each instance.
1
1
CNC Scanner Design Analysis