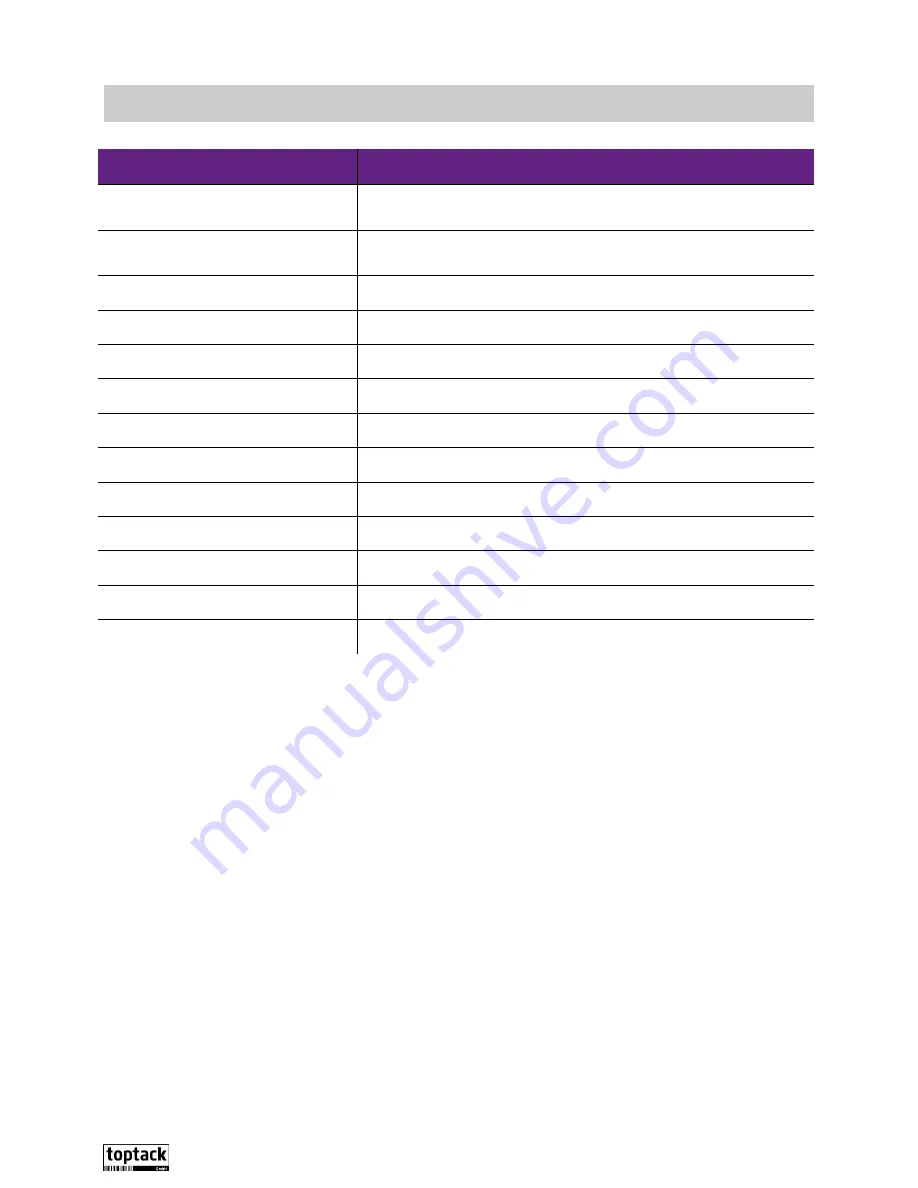
Annex
Label printing & lamination station
- Version: 2017-04-01
Page 45
ANNEX
No.
Designation
1
Circuit diagram for electrical system of the label printing &
lamination station
2
Overview plan of the pneumatic system of the label printing &
lamination station
3
"Annex 1" Description and operation of the laser control button
4
Operating manual of the thermal transfer printer
5
Operating manual of the laminate dispenser
6
Spare parts list of the label printing & lamination station
7
External data connection of the printer