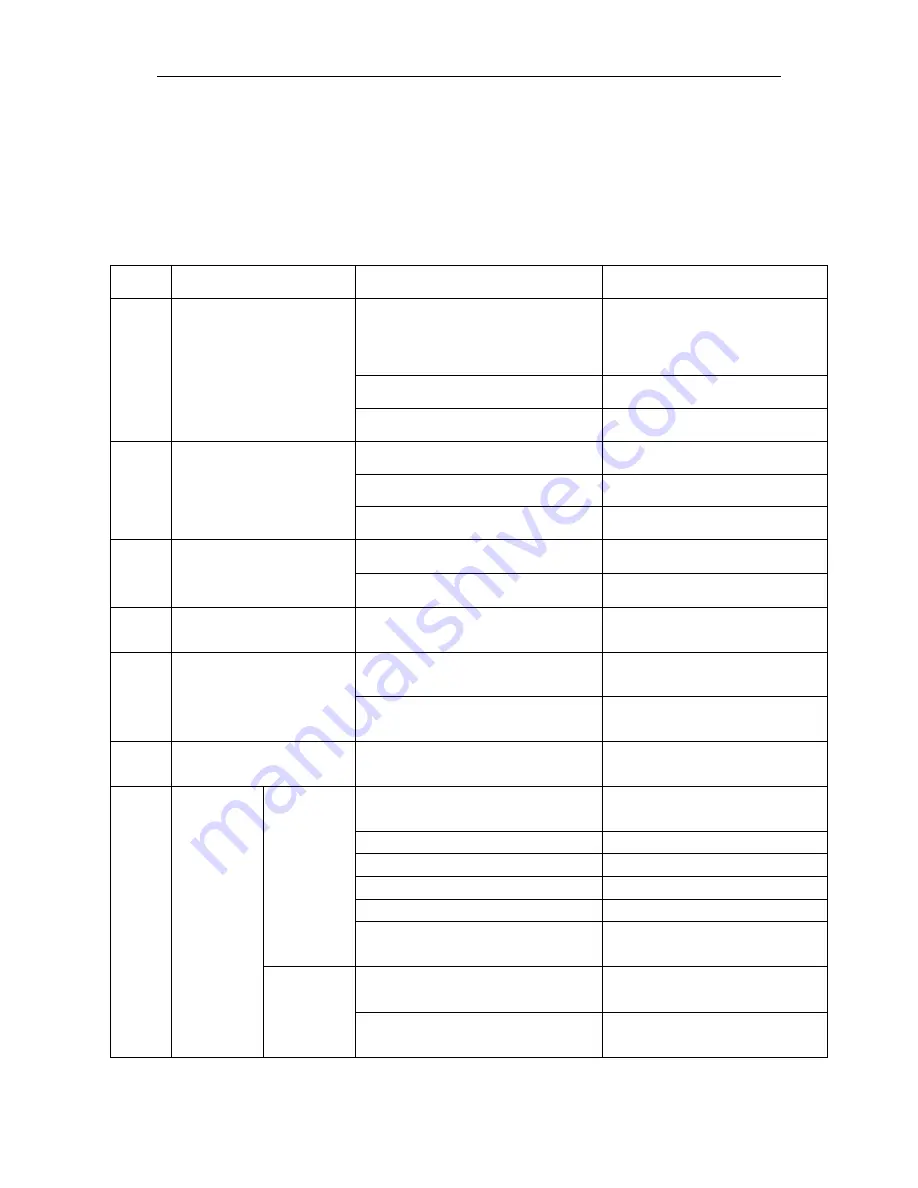
MAINTENANCE AND TROUBLESHOOTING
30
If there is any problem and has no the authorized professional maintenance personal, please
contact local agent or the branch company!
If there are some simple troubles of TIG200E AC/DC -series welding machine, you can consult the
following overhauling chart:
S/N
Troubles
Reasons
Solution
1
Turn on the power source, and
fan works, but the power pilot
lamp is not on.
The power light damaged or connection is
not good
Check and repair Pr7
The transformer of power is broken
Repair or change the transformer
Control PCB failures
Repair or change the control Pr4
2
Turn on the power source, and
the power lamp is on, but fan
doesn’t work
There is something in the fan
Clear out
The start capacitor of fan damaged
Change capacitor
The fan motor damaged
Change fan
3
Turn on the power source, the
power lamp is not on, and fan
doesn’t work
No power supply input
Check whether there is power supply
The fuse inside the machine damaged
Change it (3A)
4
The number on the display is not
intact.
The LED in the display is broken
Change the LED
5
The max and min value
displayed doesn’t accord with
the set value.
The max value is not accordant (refer to
§3.1)
Adjust potentiometer Imin on the power
board.
The min value is not accordant (refer to
§3.1)
Adjust potentiometer Imaxin the current
meter.
6
No no-load voltage output
(MMA)
The machine is damaged
Check the main circuit and the Pr4.
7
Arc can not be
ignited (TIG)
There is spark
on the HF
igniting board.
The welding cable is not connected with the
two output of the welder.
Connect the welding cable to the
welder’s output.
The welding cable damaged.
Repair or change it.
The earth cable connected unstably.
Check the earth cable.
The welding cable is too long.
Use an appropriate welding cable.
There is oil or dust on the workpiece.
Check and remove it.
The distance between tungsten electrode and
workpiece is too long.
Reduce the distance (about 3mm).
There is not
spark on the
HF igniting
board.
The HF igniting board does not work.
Repair or change Pr8
The distance between the discharger is too
short.
Adjust this distance (about 0.7mm).