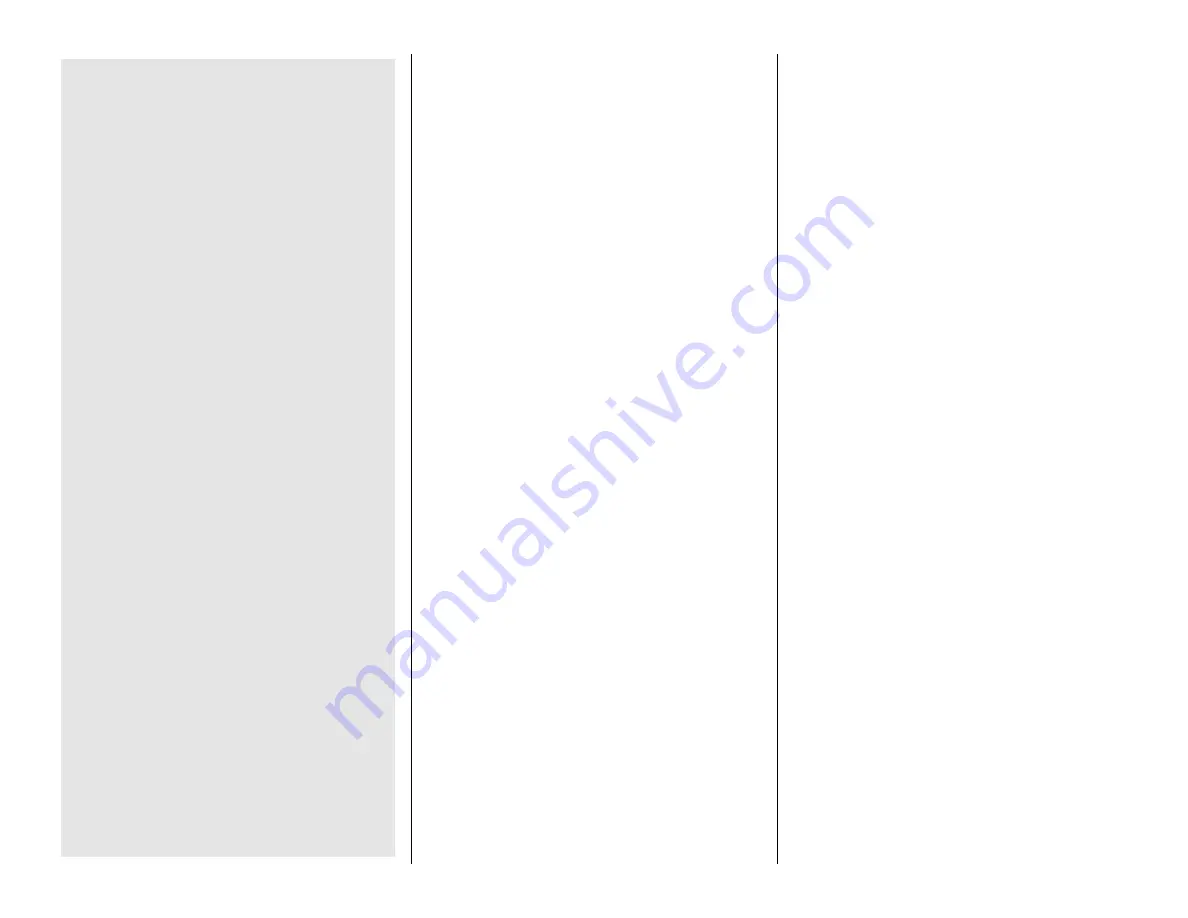
NOTES FROM THE DESIGNER
When I became interested in modeling as a kid the
Top Flite Nobler was a very popular control line
model. I built and flew several of them and still have
many fond memories from that time, almost fifty
years ago.
When the Top Flite R/C Nobler was introduced I just
had to have one. That was thirty years ago, and it
was a great flying model in its day. Now I design
models for Top Flite and jumped at the chance to
redesign the model for the anniversary re-release of
this classic model. Isn’t this hobby great!
While the original R/C Nobler was a great flying
model, it did have a number of problems. It was
difficult to build, had terrible die-cutting and required
a lot of sanding and shaping. It also had some
structural problems. We have tried hard to correct
these problems. You will note that the aft section of
the model and the tail feathers have been changed to
improve the flying characteristics.
The original R/C Nobler had a D-tube wing
construction, but the spar was just a 1/16” balsa web
- with nothing else, no spars. It was not uncommon
for the wing to fail during snap rolls. The new version
of the model also has a D-tube wing construction, but
it has top and bottom basswood spars with a die-cut
3/32” I-beam type web. The original model had balsa
block wing tips that needed to be carved and
sanded. The new version of the model has wing tips
built from die-cut parts, much like the control line
model did.
The fuselage of the original R/C Nobler was built
from die-cut sides with many balsa blocks added.
These blocks required considerable carving, shaping
and sanding. The turtle deck had an annoying habit
of cracking, causing the tail feathers to loosen. The
new version of the model has no blocks at all. The
model has die-cut sides and formers that are then
sheeted. The turtle deck and tail section have been
redesigned and strengthened.
The tail feathers on the original R/C Nobler were
made from 1/4” sheet balsa and were a bit heavy. On
hard landings the weight of the tail feathers would
cause the turtle deck to crack at various glue joints.
The tail feathers on the new version are built-up for
lightness and strength from sticks that are then
sheeted with 1/16” balsa.
I did not enjoy building the original version of the
model. The die-cutting was bad, parts fit was poor
and it required a lot of carving and sanding. I hope
you find the new version fun to build. The die-cutting
is great and the parts fit is right on, thanks to modern
computer CAD design systems. And it takes only
about 15 minutes to sand the entire model! If you are
a quick builder it would be possible to build the model
and have it ready to cover in a long weekend.
The original R/C Nobler had a fixed wing that could
not be removed from the fuselage, and could be a bit
difficult to transport and store. The new version of the
model has a removable wing held in place with three
nylon bolts.
While the original model required only four servos to
operate ailerons, rudder, throttle and elevators with
coupled flaps, the new version requires six servos.
You can also add a seventh servo for retractable
landing gear. That’s right, you can now build the
model with retractable main landing gear.
Our prototype models, with seven full size servos and
retractable landing gear weighed 5 lbs 8 oz, almost
exactly the same weight of the original model. The
structure of the new version is much lighter due to the
elimination of all the balsa blocks and also the built up
tail feathers. At the same time, it is also much stronger.
For Retractable Landing Gear you will need
these items (not included):
Great Planes Retracts (GPMQ2905)
Retract servo (FUTM0670 or HCAM0160)
(2) 2-1/4” [57mm] wheels (GPMQ4222)
(2) Nylon Clevis (GPMQ3800)
(2) 2-56 x 12” [305mm] pushrod, threaded one
end (GPMQ3750)
(2) Screw-Lock connectors (GPMQ3870)
(8) #4 x 3/8” [9.5mm] flat head sheet metal screws
FLAPS
Your R/C Nobler is designed to incorporate flaps.
You must build these flaps, but you do not have to
make them operational. If you do not want
operational flaps simply glue them into place. As
the wing is removable, the flaps cannot be
mechanically coupled to the elevator as the
original R/C Nobler could.
For normal (independent) flap operation, only one
servo is required. This allows the flaps to be used
as normal flaps as well as for elevator to flap
mixing with a computer radio system.
Slight trim changes are needed when flaps are
extended. The trim corrections are discussed later
in the control surface throws section and you will
find more information on the flaps in the
Flying
section and the radio installation section.
For Flaps, you will need the following
additional item:
one standard servo.
- 4 -
Summary of Contents for Gold Edition Nobler
Page 7: ...7 DIE CUT PATTERNS...
Page 52: ...2 VIEW Use this layout to plan your trim scheme...
Page 53: ...B C...
Page 54: ...D A...