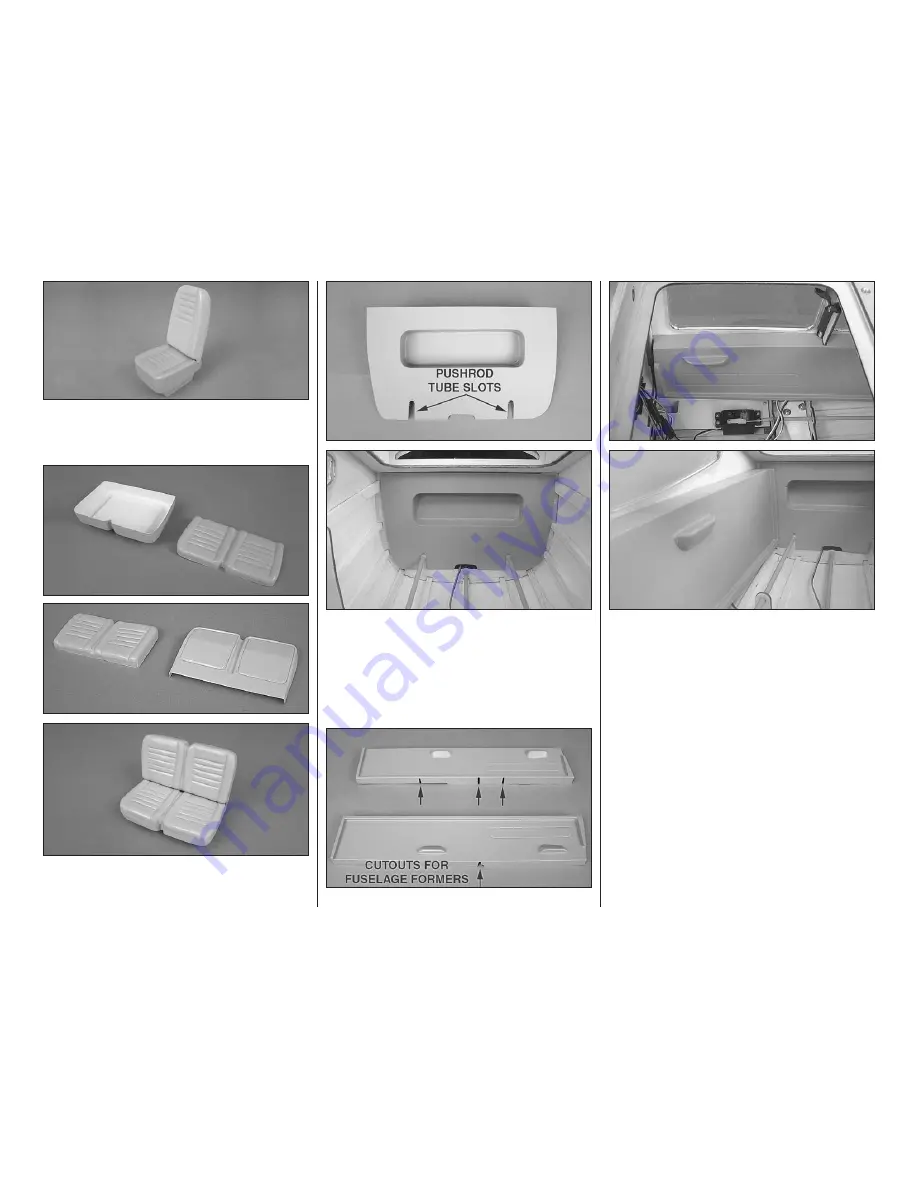
27
o
4. Fit the assembled seat back to the seat bottom.
Make any final adjustments to the fit and glue the
assemblies together.
o
5. The back seat is assembled in the same manner
as the front.
o
6. Cut out the cockpit back panel. Slots will need to be
made for the elevator and rudder pushrod tubes, as well
as a cutout for the tail light wire to pass under. The piece
should sit flat against the fuselage former just behind
the back window. Glue the cockpit back in place.
Work slowly during step 7 to cut cockpit side panels
that fit well.
o
7. Rough cut the cockpit side panels leaving as
much material as possible. Slots will need to be cut
at the top and bottom of the pieces to fit around the
fuselage formers. Temporarily fit the pieces in place
and use a felt-tip pen or pencil to mark the center
of each former onto the side pieces where they will
need to be trimmed (be careful not to get pen marks
in areas that will not be cut away since the ink would
be difficult to remove from the painted pieces). With
the slots cut in the correct positions, carefully start
trimming the top, outside edges of the side panels.
The top of the panels should rest on the fuselage
stringers that are located just below the side windows.
Trim these edges so that there are no gaps between
the top edges of the side panels and the fuselage
sides. The panels will need to be gently forced
against the fuselage sides to follow the contour of the
fuselage. When satisfied with the fit, finish sand the
edges and glue the panels in place.