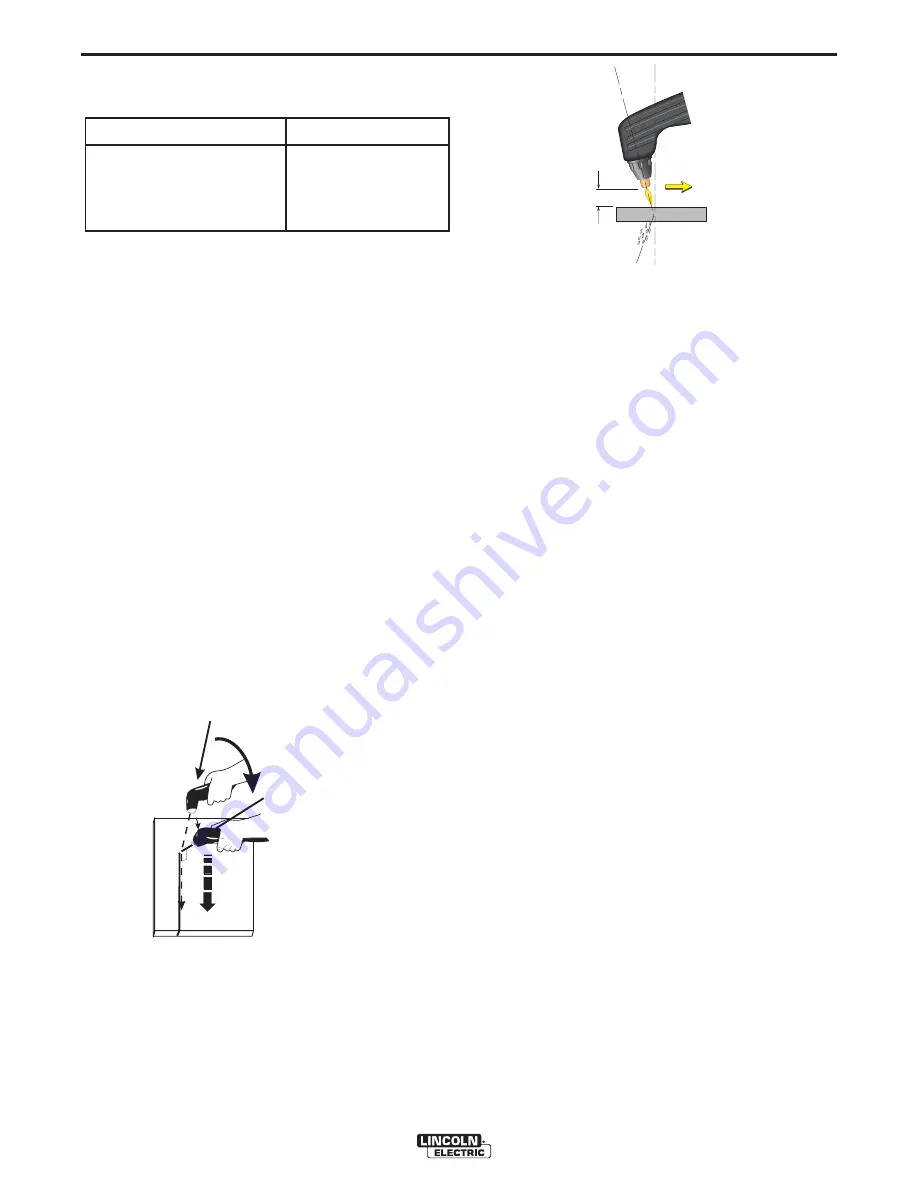
Direction of Travel
5 - 15
1/16”
10 - 20
Arc Lag
Leading Angle
• Use a 5° - 15° leading angle in the direction of the cut.
• Finish the cut to be made and release the trigger.
• If the dross is difficult to remove, reduce the cutting
speed. High speed dross is more difficult to remove
than low speed dross.
PROCESS GOUGING
Gouging is a process used to remove material without
cutting entirely through the workpiece. The Tomahawk
1000 has the capability of performing plasma gouging
with the proper consumables attached to the torch. In
general, gouging consumables provide a wider plas-
ma arc compared to a cutting arc. As the material
melts, it is blown forward by the pressurized gas com-
ing out of the torch. The dross will land on the surface
of the workpiece and can easily be removed after the
gouging process is complete.
Technique:
Hold the torch at a 45º angle to the workpiece. Pull
the torch trigger to start the gouging arc. As the mate-
rial is removed move the torch forward to continue
removing material. When the desired amount of
material has been removed, release the torch trigger
to stop the gouging process.
Typically, the larger the angle between the torch and
the workpiece, the deeper and slower the gouging.
As the torch angle is decreased, less material is
removed and the travel speeds can be increased.
Keeping the torch fixed while moving forward will
remove a straight line of material. Using a side-to-
side, weaving motion will remove a wider area of
material. The output of the Tomahawk 1000 can also
be increased or decreased to control the amount of
material being removed. Most users tend to maximize
the output in order to remove the most material in a
short amount of time.
B-6
OPERATION
B-6
TOMAHAWK™ 1000
• The Post Flow time is proportional to the selected
cutting current and it is divided into 4 time ranges:
• Pilot Arc
- The air will flow for a preflow time of 2 seconds
and the pilot arc will start. (Exceptions: the first
time that the trigger is pulled after the machine is
turned on, or after a thermal, the initial trigger will
be ignored. This is a safety feature to prevent the
pilot arc from firing unexpectedly. The other
exception is if the machine is in postflow, then the
preflow time is skipped and the pilot arc will start
immediately.)
- The pilot arc will run for 3.0 seconds and shut off
unless the arc is brought in contact with the work
and the arc is transferred. Avoid excessive pilot
arc time by transferring the arc to the workpiece
quickly. This will extend consumable life.
- When the arc is brought within 1/8” - 1/4" from the
work piece the arc will transfer, the current will
ramp to the setting on the control panel, and the
cut can last indefinitely (or until the duty cycle of
the TOMAHAWK™ 1000 is exceeded).
• Pierce the work piece by slowly lowering the torch
onto the metal at a 30
0
angle away from the opera-
tor. This will blow the dross away from the torch tip.
Slowly rotate the torch to vertical position as the arc
becomes deeper.
• Keep moving while cutting. Cut at a steady speed
without pausing. Maintain the cutting speed so that
the arc lag is 10° to 20° behind the travel direction.
30
30
0
0
VER
VERTICAL
ANGLE
TICAL ANGLE
FOR CUTTING
FOR CUTTING
CUT
90
0
TORCH AT 30
0
ANGLE
TO PIERCE
ROTATE TO
90
0
ANGLE TO CUT
Selected Cutting Current
Post Flow Time
Less than 30A
15 seconds
Between 30A and 40A
20 seconds
Between 40A and 50A
25 seconds
Greater than 50A
30 seconds
Summary of Contents for 1000
Page 4: ...NOTES ...