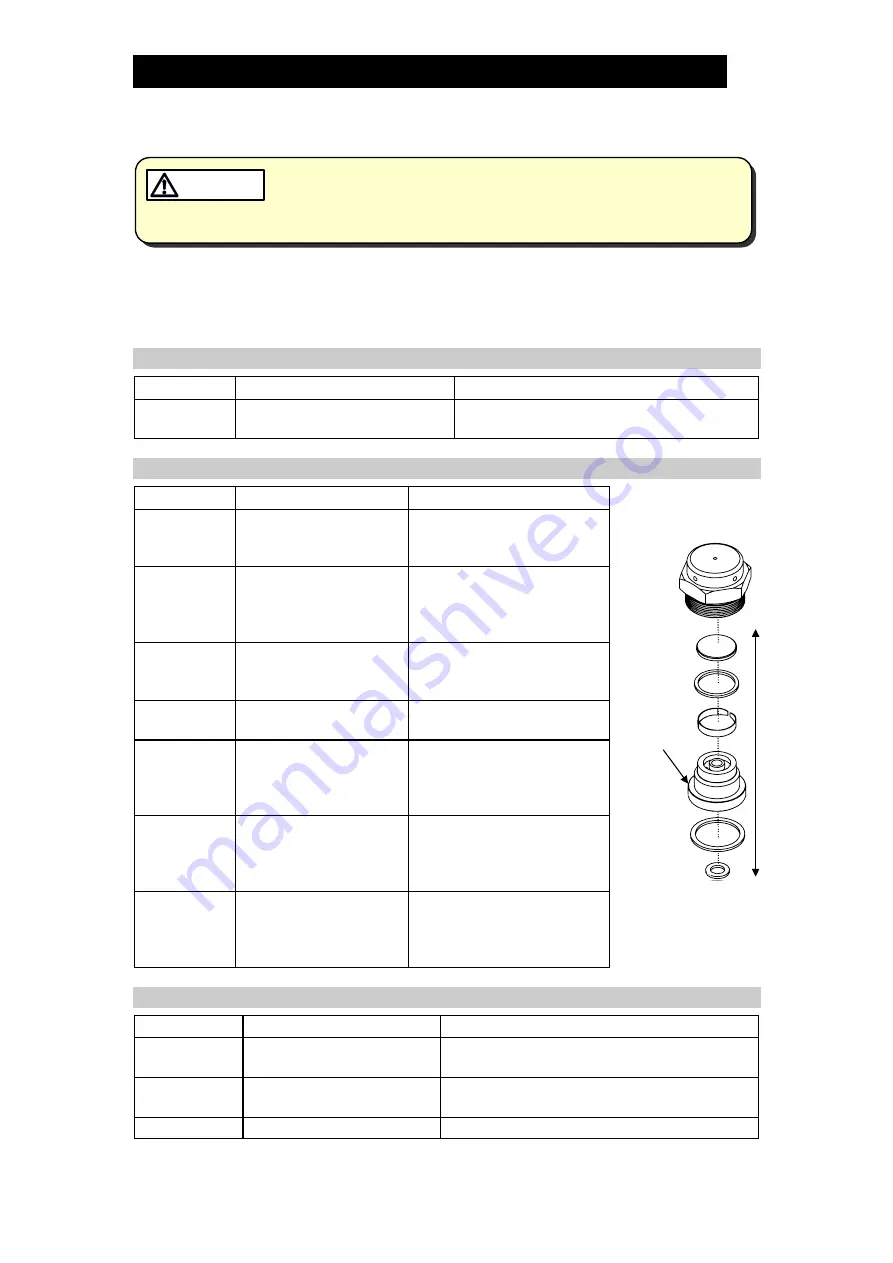
172-65135MA-01 (P46SR + BO2) 1 Oct 2009
8
Disassembly / Reassembly
When disassembling or removing the product, wait until the internal
pressure equals atmospheric pressure and the surface of the product
has cooled to room temperature. Disassembling or removing the
product when it is hot or under pressure may lead to discharge of fluids,
causing burns, other injuries or damage.
CAUTION
Use the following procedures to remove components. Use the same procedures in
reverse to reassemble.
(Installation, inspection, maintenance, repairs, disassembly, adjustment and valve
opening/closing should be carried out only by trained maintenance personnel.)
Removing / Reattaching the Cap
Part
During Disassembly
During Reassembly
Cap
Gently turn the cap to remove Being careful not to bend it, gently turn the
cap to tighten
Removing / Reattaching the Cover and its Components
Part
During Disassembly
During Reassembly
Cover
Remove with a socket
wrench
Consult the table of
tightening torques and
tighten to the proper torque
Disc
Remove carefully, being
careful not to scratch
the polished seat
surface
Be careful that the seat
surface (the lapped side) is
facing down (toward the
body)
Disc Holder
Ring
Remove without
bending
Set on the air vent ring;
make sure that it does not
sit on the valve seat surface
Air Vent Ring Remove without
bending
Reinsert without bending
Module Valve
Seat
Remove carefully, being
careful not to scratch
the polished seat
surface
Insert into the body levelly,
being careful not to tilt it or
to scratch the seat surface
(Figure A)
Outer Module
Gasket
Remove with a
screwdriver, or other
suitable tool and clean
the gasket housing
Replace with a new gasket
if damaged
Inner Module
Gasket
Remove with a
screwdriver, or other
suitable tool and clean
the gasket housing
Replace with a new gasket
if damaged
Disassembly / Reassembly of Components Inside the Body
Part
During Disassembly
During Reassembly
Screen Holder Remove with a socket
wrench
Consult the table of tightening torques and
tighten to the proper torque
Screen Holder
Gasket
—
Replace with new gasket; coat surfaces with
anti-seize
Screen
Remove without bending
Reinsert without bending
Figure A
Module
Valve Seat