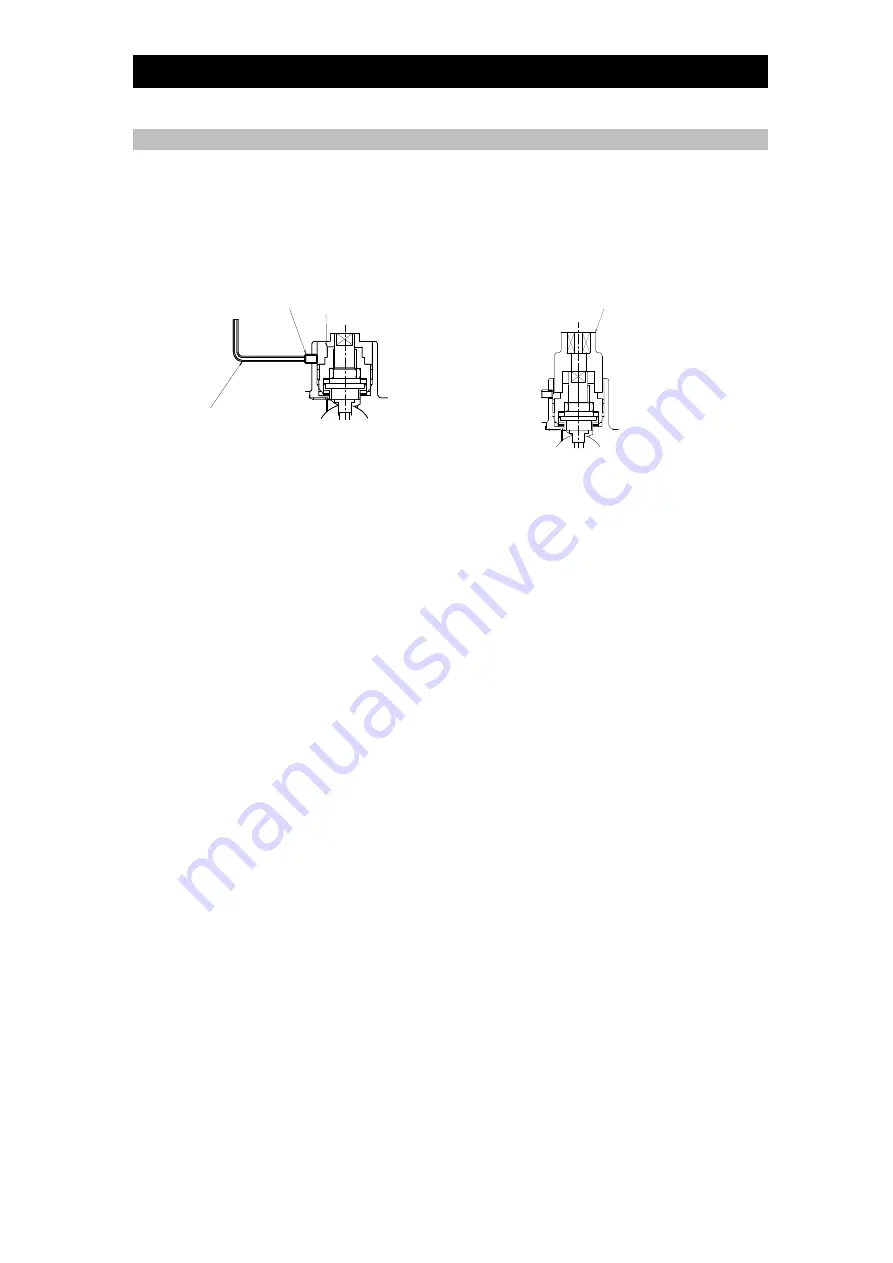
18
MBT3N/PBT3N: Additional Tightening of the Valve Unit Gland Section
It is possible to further tighten the gland section in the MBT3N/PBT3N valve units.
1. Detach the actuator unit (refer to the “Disassembly/Reassembly” section for
details).
2. Follow the steps given below to apply additional tightening
1) Loosen the holder screw.
2) Tighten the gland holder further in with
a socket wrench.
Holder Screw Gland Holder
Hex Key
Diameter: 2 mm
Socket Wrench:
diameter 17 mm
3) Retighten the holder screw.
Cautions when applying additional tightening:
•
Do not tighten the gland holder completely the first time. Do not tighten it any more
than necessary to stop leakage.
•
If leakage continues even after applying additional tightening to the gland holder,
replace parts.
172-65162M-03 (BT3N/MBT3N/PBT3N) 5 Jul 2013