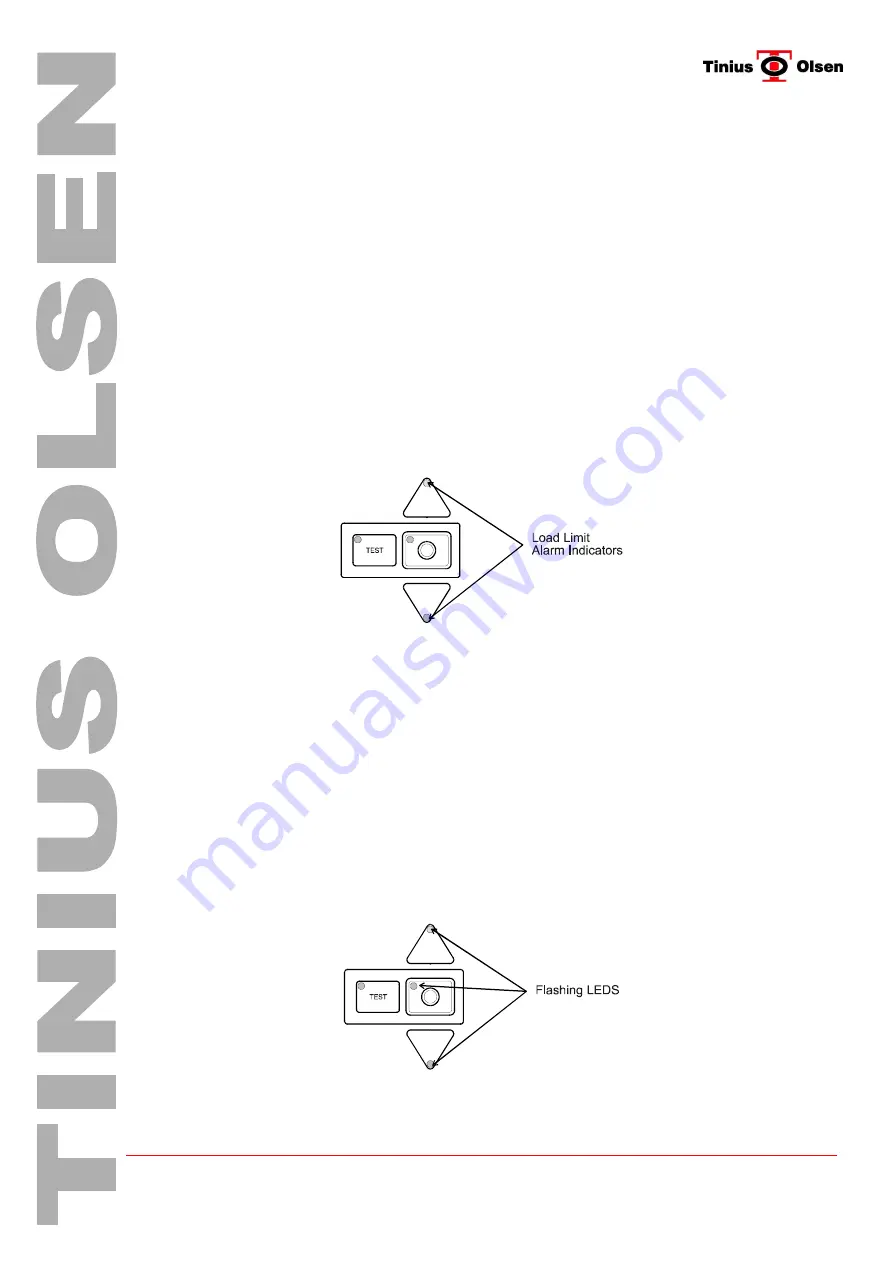
© Tinius Olsen Ltd
L-Series Manual – Issue 1
Page 24 of 31
6.5.2. Load Limit Alarm
A load limit alarm is flagged when the machine or load cell capacity is exceeded either
in tension or compression. The value of the alarm depends upon the load cell fitted and
is approximately 9% greater than load cell capacity. E.g. If a 10KN load cell was fitted
to a H50KL machine the alarm would be triggered at 10.9kN in tension or compression.
This system should not be relied on to protect the machine or operator, as the
machine’s ability to stop prior to damage is greatly reduced at high crosshead speeds.
The alarm direction is indicated by the Flashing LED indicator on the appropriate
direction key, reporting an alarm message on the software control panel and audible
alarm. The alarm can be cleared by backing the crosshead off in the opposite direction
to reduce the applied force using the appropriate direction key. If the alarm persists it is
possible that the load cell has been damaged.
Note A load limit alarm can be triggered if the load cell is not fitted or incorrectly
installed. The direction key which is indicating the alarm will be disabled. This is to
protect the machine or load cell in the event of incorrect direction selection.
The diagram below indicates the Load Limit alarm indicators.
6.5.3. Emergency Stop Alarm
Activation of the emergency stop switch is by pressing the top of the switch downwards.
On activating the emergency stop switch the machine will be placed into a stop
condition and flag an emergency stop alarm by flashing both direction and stop LED
indicators, reporting an alarm message on the software control panel and audible alarm.
To reset the emergency stop switch rotate the top part of the switch clockwise (direction
shown by arrows on top of switch). On rotation the top will spring upwards returning the
switch to its normal position. To clear the alarm indicators select ‘OK’ on the software
alarm panel. This panel automatically appears when an alarm condition is present. The
machine will now return to normal operation.
Note Resetting the emergency stop alarm by powering the machine OFF and ON
again may require restarting the software.