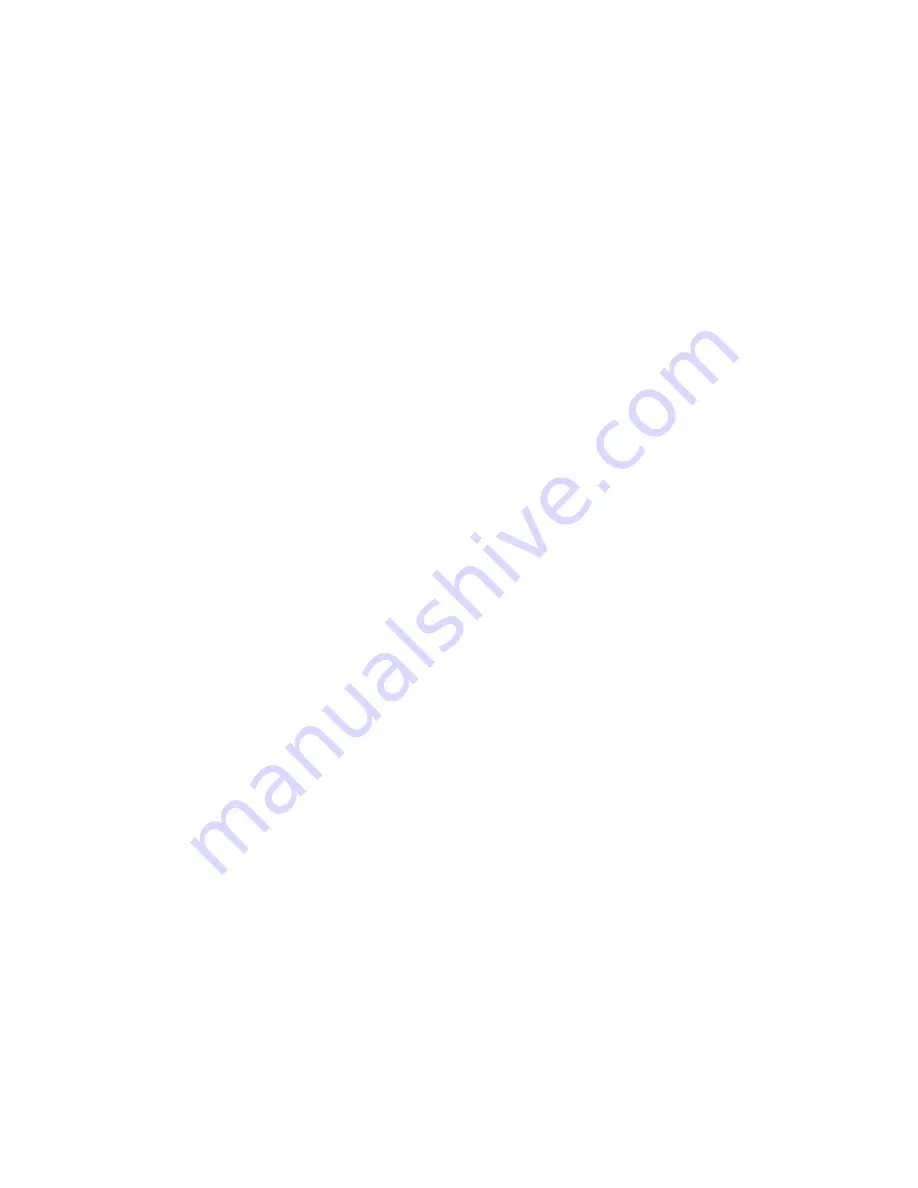
5
Bending and repeat bends - Bending is accomplished by clamping the work piece
under the ram assembly so that the desired line of bend is held at the forward edge of
the nose bar and by elevating the apron assembly until the desired degree of bend is
obtained. The maximum degree of bend is approximately 140 degrees. Due to the
”spring back” in various materials some overbending may be required to get the
desired bend angle. For repeat bends, adjust the stop on the stop rod to limit the swing
of the apron assembly. The stop is secured in place with a setscrew.
There are four adjustments to do in the following order. Use test strips approximately 2
inch x 3 inch of the same material and thickness you will be forming. You will also need
several full lengths or near full-length pieces by about 4 inches wide of the material you
are setting up for.
Check CLAMPING PRESSURE by placing test strips in the brake about 3 or 4 inches
away from each end of brake. Adjust the clamping pressure so that it is at most only
enough to keep the material from slipping. It is not desirable to use more clamping
pressure. More pressure can “pre-load” the brake in a way, which will force a distortion.
Your best results may be with zero clamping pressure. To change clamping pressure use
the nuts at the bottom of the cam assembly stem.
RADIUS/SET BACK refers to the distance between the leading edge of the clamp and
the inside edge of the apron. Look at your brake from behind. Loosen bolts allowing you
to move the clamp forward or back on the table. Now from the front, look at the distance
between the leading edge of the clamp and the inside edge of the apron. Move the clamp
back from the apron at least 1.5 times the thickness of the material being formed. Be sure
to move the clamp back a little too far and then move it forward to take out any slack.
Recheck clamping pressure. Be sure clamping pressure is very little or none.
Check END TO END CLAMP ALIGNMENT by placing a test strip about 3 or 4 inches
from each end of the brake, and bend to approximately 90 degrees. See if they appear to
be bent to the same degree. Remove the test strips from the brake and stack one inside the
other. Compare the sharpness of the radius. If one test strip is over bent or has a sharper
radius, increase the radius set back on the “tight end” slightly and test again. Here too,
you want to be sure move the clamp back a little extra and then bring it forward to take
out any slack.
TRUSS RODS are adjustable to help make the center of the brake bend the same as the
ends. Use truss rods to change the shape of the brake and/or to stiffen it. On models with
2 truss rods on the clamp, you can stiffen the clamp to some degree by “pushing” with the
larger truss and then “pulling back” with the smaller one.
There is a large nut on each of the truss rods, which can add pressure in the center of the
clamp, table, or apron. If adjustment is needed, usually the clamp is the place to start. A
combination of adjusting the clamp, apron and table truss rods may be needed. After
making a change, use the 2” x 3” test strips near the ends of the brake to re-check clamp
pressure and end to end alignment, then use a full length strip to see if the middle is
Summary of Contents for TK 422
Page 8: ...8...