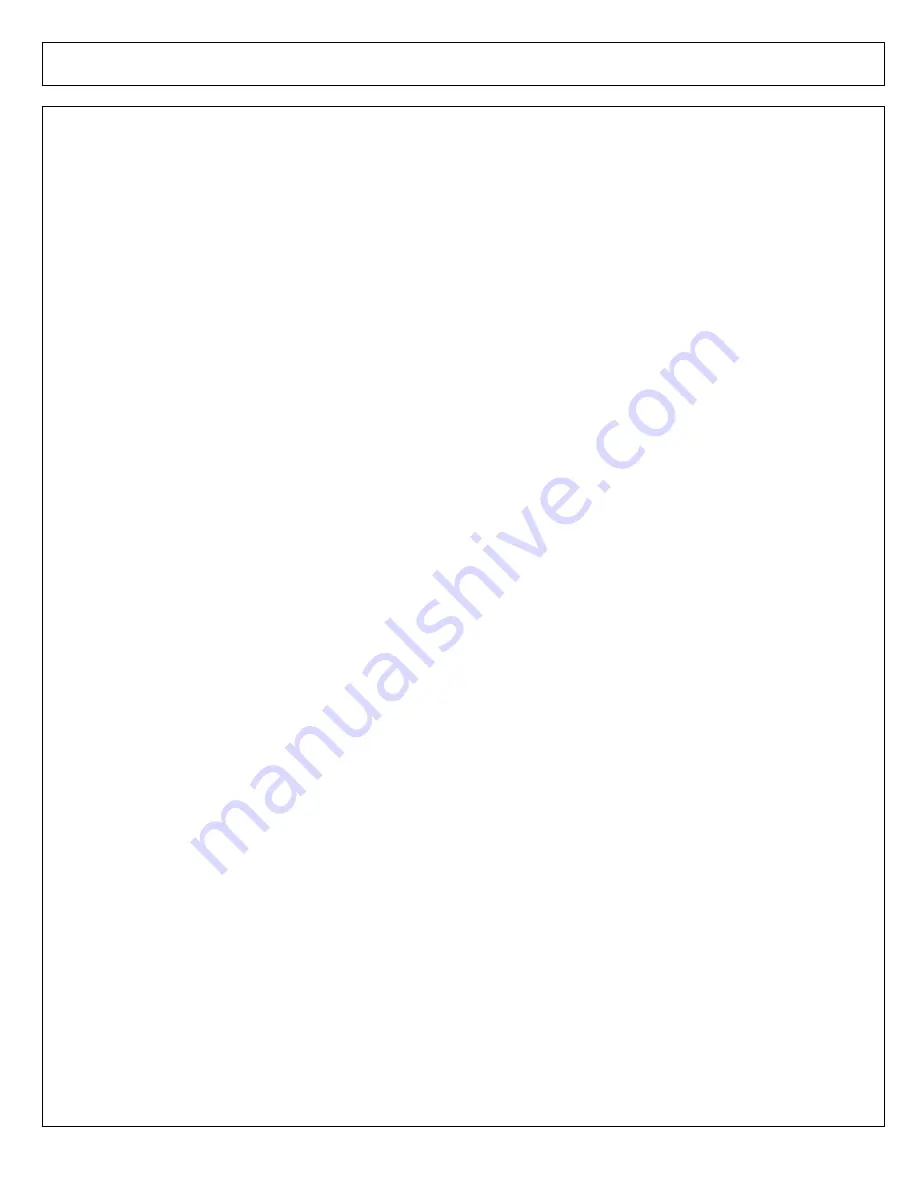
CABLE (MANUAL) LIFT VALVE BREAKDOWN - 31752
Continued...
ITEM
PART NO. QTY.
DESCRIPTION
1
TB1017S
1
INLET END COVER
2
TB1702
1
END COVER, POWER BEYOND
3
TB1017P
1
VALVE SECTION (SINGLE ACTING, SPRING DETENT)
4
TB1017P
1
VALVE SECTION (SINGLE ACTING, SPRING DETENT)
5
N/A
-
N/A
6
N/A
-
N/A
7
TB1017M
1
SHUT-OFF PLUG
8
TB1017E
1
RELIEF VALVE, 2250 PSI
9
TB1017M
1
SHUT-OFF PLUG
10
TB1017M
1
SHUT-OFF PLUG
11
TB1017A
2
VALVE SEAL KIT (FOR ONE SECTION)
11A
------
2
WIPER
11B
------
2
O-RING SMALL
11C
------
1
O-RING LARGE
11D
------
1
SPRING
11E
------
1
PUCKET
12
TB1017L
2
LEVER KIT (FOR ONE SECTION)
12A
------
1
LEVER KNOB
12B
------
1
LEVER
12C
------
2
LEVER WASHER
12D
------
1
LEVER CLIP
12E
------
2
LINKAGE
12F
------
1
LEVER PIN
12G
------
1
ROLL PIN
12H
------
1
LEVER BOOT
12J
------
1
LEVER BOLT
12K
------
1
LEVER DUST COVER
12L
------
1
LEVER NUT
13
TB1017X
1
TIE ROD KIT
14
24214
1
O-RING, LARGE
©2011 Alamo Group Inc.
Parts Section 6-27
COMMON SIDE FLAIL - SD
Summary of Contents for JD 5065M
Page 4: ......
Page 6: ......
Page 7: ...Side Rear flail Safety Section 1 1 SAFETY SAFETY SECTION ...
Page 23: ...Side Rear flail Safety Section 1 17 SAFETY 34852 HYDRAULIC TANK 06550054 ON MOWER HEAD ...
Page 26: ...Side Rear flail Safety Section 1 20 SAFETY ...
Page 27: ...Assembly Section 2 1 ASSEMBLY SECTION JD5XX5M TSF ...
Page 46: ...ASSEMBLY Assembly Section 2 20 CONTINUOUS DUTY SOLENOID SWITCH MOUNTING ASM JD 0096 ...
Page 52: ...ASSEMBLY Assembly Section 2 26 ...
Page 53: ...Operation Section 3 1 2011 Alamo Group Inc OPERATION SECTION ...
Page 88: ...OPERATION Side and Rear Flail Operation Section 3 36 2011 Alamo Group Inc OPERATION ...
Page 89: ...Maintenance Section 4 1 2011 Alamo Group Inc MAINTENANCE SECTION ...
Page 119: ...MAINTENANCE Side and Rear Flail Maintenance Section 4 31 2011 Alamo Group Inc MAINTENANCE ...
Page 121: ...PARTS SECTION JD 5XX5M TSF ...
Page 122: ...NOTES ...
Page 124: ...PARTS ORDERING GUIDE 2011 Alamo Group Inc Parts Section 5 4 JD5XX5M TSF ...
Page 125: ...NOTES 2011 Alamo Group Inc Parts Section 5 5 JD5XX5M TSF ...
Page 126: ...TRACTOR MOUNT KIT 2011 Alamo Group Inc Parts Section 5 6 JD5XX5M TSF ...
Page 130: ...2 SPOOL CABLE CONTROL STAND 2011 Alamo Group Inc Parts Section 5 10 JD5XX5M TSF ...
Page 132: ...CABLE MANUAL LIFT VALVE 2 SPOOL 2011 Alamo Group Inc Parts Section 5 12 JD5XX5M TSF ...
Page 134: ...CABLE MANUAL LIFT VALVE BREAKDOWN 24873 2011 Alamo Group Inc Parts Section 5 14 JD5XX5M TSF ...
Page 138: ...NOTES 1 2011 Alamo Group Inc Parts Section 5 18 JD5XX5M TSF ...
Page 139: ...COMMON SIDE FLAIL SUPER DUTY PARTS SECTION ...
Page 140: ......
Page 142: ...PARTS ORDERING GUIDE 2011 Alamo Group Inc Parts Section 6 4 COMMON SIDE FLAIL SD ...
Page 143: ...NOTES 2011 Alamo Group Inc Parts Section 6 5 COMMON SIDE FLAIL SD ...
Page 144: ...COMBO DRAFT BEAM 2011 Alamo Group Inc Parts Section 6 6 COMMON SIDE FLAIL SD ...
Page 146: ...63IN SIDE FLAIL STANDARD ROTATION 2011 Alamo Group Inc Parts Section 6 8 COMMON SIDE FLAIL SD ...
Page 148: ...63IN SIDE FLAIL REVERSE ROTATION 2011 Alamo Group Inc Parts Section 6 10 COMMON SIDE FLAIL SD ...
Page 152: ...75IN SIDE FLAIL REVERSE ROTATION 2011 Alamo Group Inc Parts Section 6 14 COMMON SIDE FLAIL SD ...
Page 154: ...SIDE FLAIL DRIVE ASSEMBLY 2011 Alamo Group Inc Parts Section 6 16 COMMON SIDE FLAIL SD ...
Page 159: ...NOTES 2 2011 Alamo Group Inc Parts Section 6 21 COMMON SIDE FLAIL SD ...
Page 176: ...COOLER ASSEMBLY 2011 Alamo Group Inc Parts Section 6 38 COMMON SIDE FLAIL SD ...
Page 179: ...BRAKE VALVE HYDRAULIC SCHEMATIC 2011 Alamo Group Inc Parts Section 6 41 COMMON SIDE FLAIL SD ...
Page 183: ...SWITCH BOX SCHEMATIC 2011 Alamo Group Inc Parts Section 6 45 COMMON SIDE FLAIL SD ...
Page 184: ...NOTES 3 2011 Alamo Group Inc Parts Section 6 46 COMMON SIDE FLAIL SD ...
Page 185: ...FIRE SUPRESSION SYSTEM 2011 Alamo Group Inc Parts Section 6 47 COMMON SIDE FLAIL SD ...
Page 186: ...FIRE SUPRESSION SYSTEM PARTS 2011 Alamo Group Inc Parts Section 6 48 COMMON SIDE FLAIL SD ...
Page 189: ...WETCUT 2011 Alamo Group Inc Parts Section 6 51 COMMON SIDE FLAIL SD ...
Page 192: ...WETCUT TANK PLUMBING 2011 Alamo Group Inc Parts Section 6 54 COMMON SIDE FLAIL SD ...
Page 194: ...WETCUT SPRAYER HEAD ASSEMBLY 2011 Alamo Group Inc Parts Section 6 56 COMMON SIDE FLAIL SD ...
Page 196: ...WETCUT CABLES 2011 Alamo Group Inc Parts Section 6 58 COMMON SIDE FLAIL SD ...
Page 197: ...WARRANTY SECTION Warranty Section 7 1 ...
Page 198: ... ...
Page 202: ...Printed in USA Tiger Corporation ...