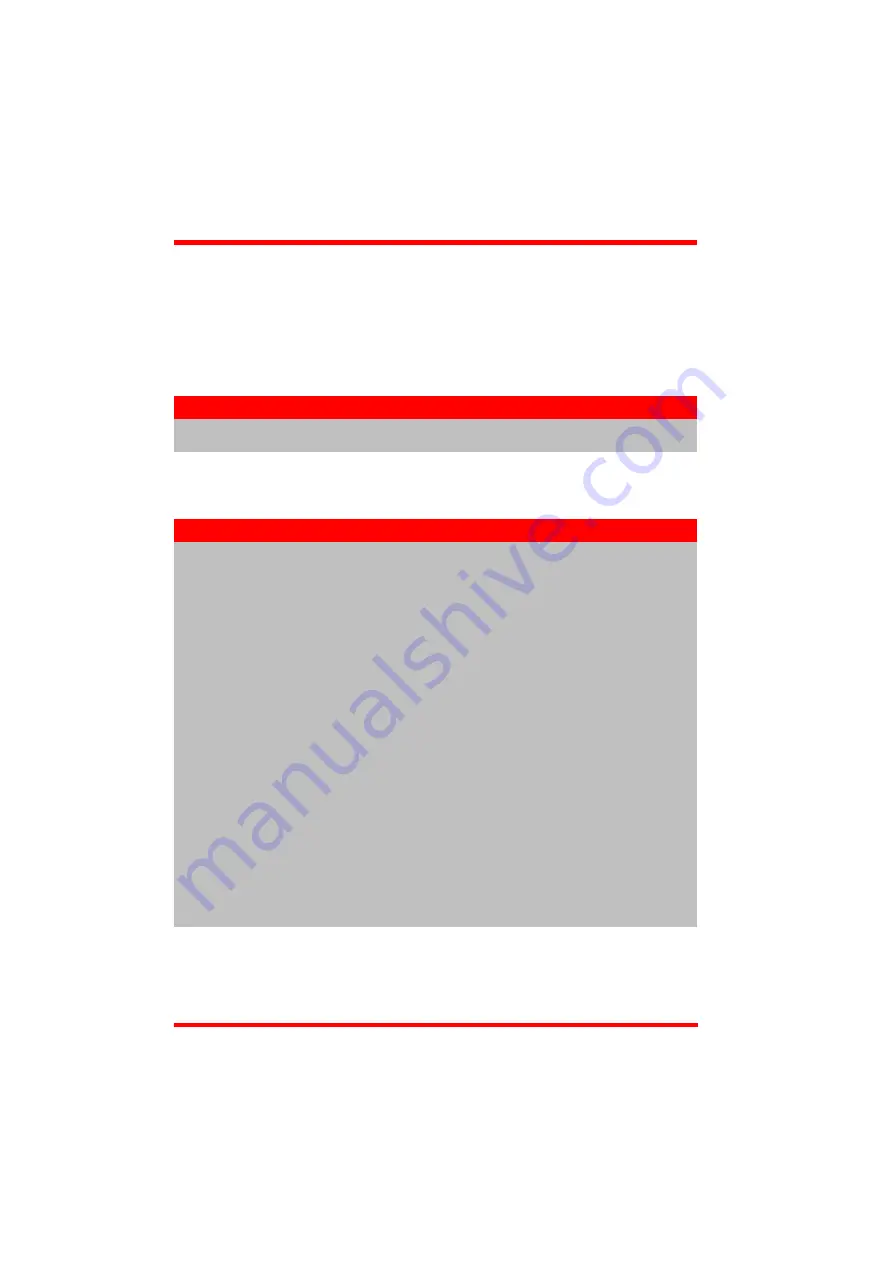
50
HA0141T Rev 7 Oct 2014
Chapter 6
Motor
These parameters are used to set the 'resolution' characteristics of the stepper motor
connected to the selected channel. The resolution of the motor, combined with other
characteristics (such as lead screw pitch) of the associated actuator or stage,
determines the overall resolution.
Steps Per Rev
- The number of full steps per revolution of the stepper motor
(minimum '1', maximum '10000').
Gearbox Ratio
- The ratio of the gearbox. For example, if the gearbox has a reduction
ratio of X:1 (i.e. every 1 turn at the output of the gearbox requires X turns of the motor
shaft) then the Gearbox Ratio value is set to X. (minimum '1', maximum '1000').
Persist Settings to Hardware -
Many of the parameters that can be set for the Stepper
Driver T-Cube can be stored (persisted) within the unit itself, such that when the unit
is next powered up these settings are applied automatically. This is particularly
important when the driver is being used manually in the absence of a PC and USB
Note
The
Gearbox Ratio
parameter is applicable only to motors fitted with a
gearbox.
Note
The ‘Steps Per Rev’ and ‘Gearbox Ratio’ parameters, together with the
‘Pitch’ and ‘Units’ parameters are used to calculate the calibration factor
for use when converting real world units to microsteps. However, the
‘Steps Per Rev’ parameter is entered as full steps, not microsteps. The
system automatically applies a factor of 128 microsteps per full step.
The stepper motors used on the majority of Thorlabs stages/actuators
have 200 full steps per rev and no gearbox fitted. For these motors the
Steps Per Rev and Gearbox Ratio parameters have values of 200 and 1
respectively. As an exception to this, the ZST family of actuators use 24
steps per rev stepper motors fitted with a 76:1 reduction gearbox. In this
case, the Steps Per Rev and Gearbox Ratio should be set to '24' and '76'
respectively. The equivalent calibration constant is then calculated as:
24 x 128 x 76 x 2 = 466944
24 steps per revolution
128 microsteps per full step
76:1 reduction gearbox
0.5mm lead screw pitch
The correct default values for Steps Per Rev and Gearbox Ratio are
applied automatically when the APTConfig.exe utility is used to associate
a specific stage or actuator type with a motor channel. See the APTConfig
helpfile and the tutorial Section 3.5. for more details.