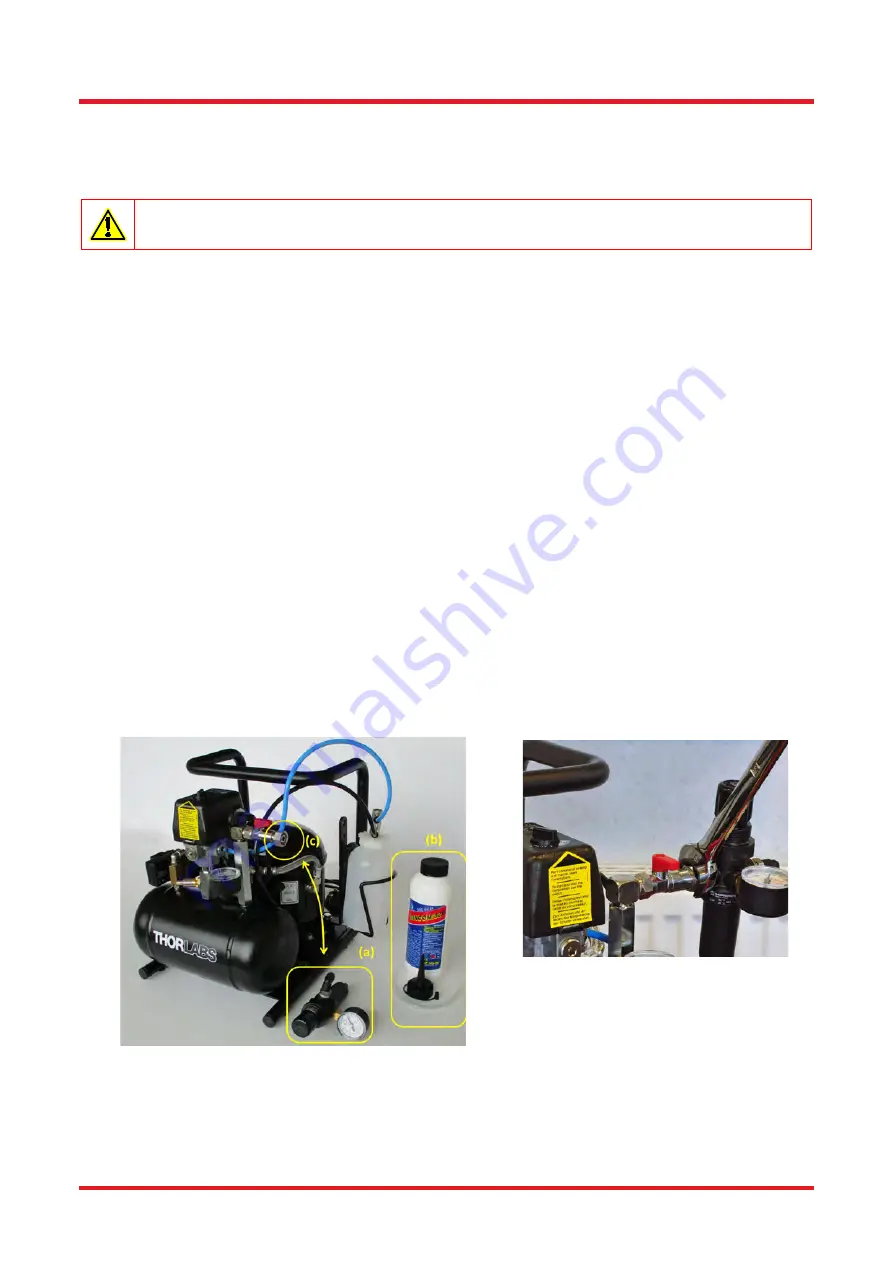
PTA522, PTA523 and PTA524 Automatic Silent Compressors
Chapter 2: Installation
Page 2
ETN057391-D02
Chapter 2
Installation
2.1.
Environmental Conditions
Warning
Operation outside the following environmental limits may adversely affect operator safety.
Location:
Indoor use only
Maximum altitude:
2000 m
Temperature range:
15°C to 40°C
Maximum Humidity:
Less than 80% RH (non-condensing) at 31°C
Line Voltage Fluctuations:
Less than ±10% of the line voltage
To ensure reliable operation the unit should not be exposed to corrosive agents or excessive moisture, heat or dust.
If the unit has been stored at a low temperature or in an environment of high humidity, it must be allowed to reach ambient
conditions before being powered up.
The unit is not designed to be used in explosive environments.
2.2.
Parts List
On unpacking, the kit should include the following items, as shown in Figure 1:
•
The compressor
•
one oil bottle, type ROLOIL - SINCOM/32E; one bottle nozzle; 20 cm length of clear plastic tube
•
Instruction manual
To avoid damage during transport, the outlet regulation valve (a) has been removed from the main compressor unit, and
should be re-attached to connection port (c) using a 19 mm (or adjustable) spanner, as detailed in Figure 1.
Figure 1 (Left) Compressor Parts and Accessories. (Right) Re-attaching the Outlet Regulator