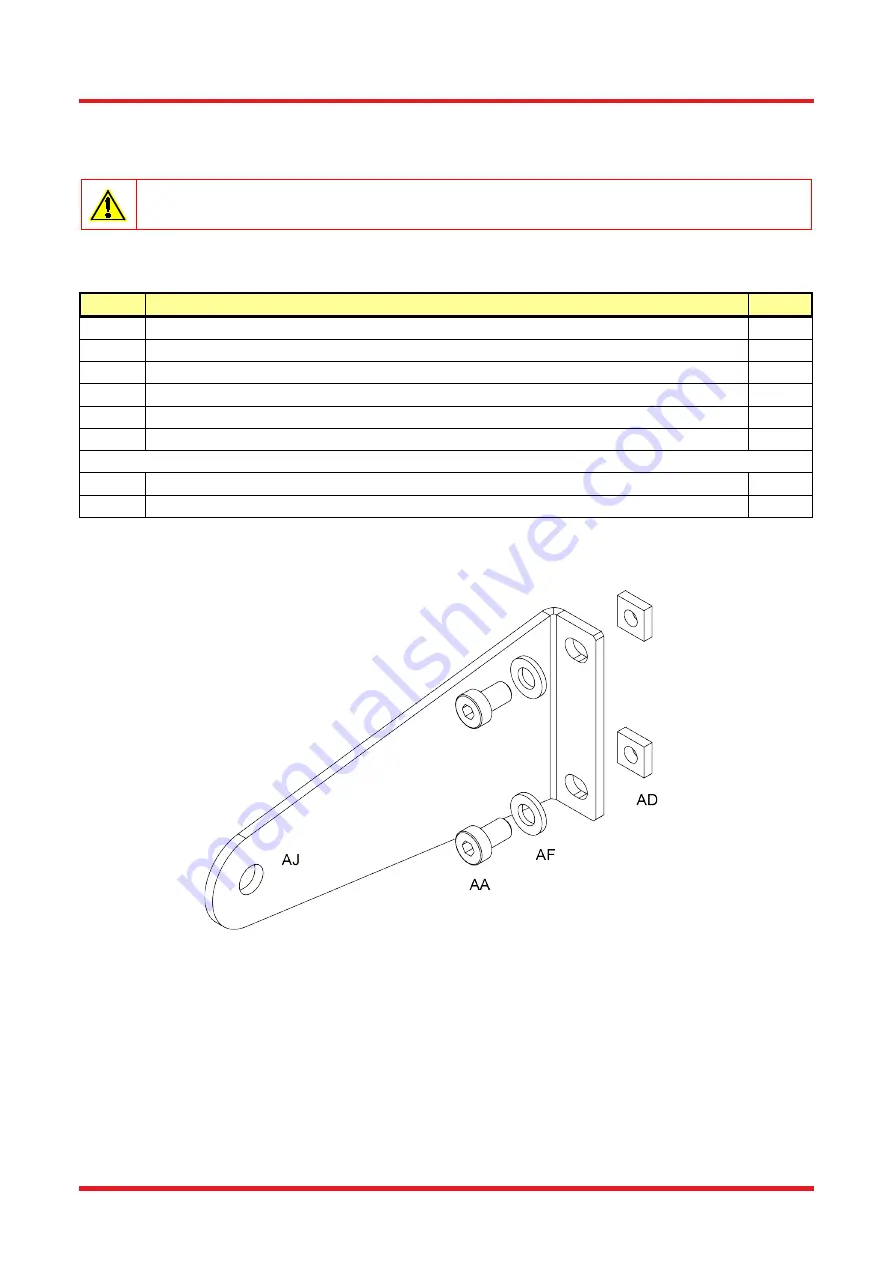
LFE1220-US, -EU, and -UK Laminar Flow Enclosures
Chapter 3: Installation
Rev A August 2020
Page 45
3.10. Attach Curtain Bar
The curtain bar has been provided to be attached to the primary side of access, to allow the user to lift strip curtains out of
the way during periods of access. It attaches to one long side of the Laminar Flow Enclosure.
Warning
The Curtain Bar is not a structural member, and should not be used to hang anything other than the strip curtains.
3.10.1. Required Parts:
Code
Description
Qty
O
Curtain Bar
1
AA
M6 x 1.0 Low Profile Channel Screw, 10mm Long
4
AD
XE25T3/M Square Nut
4
AF
M6 Washer
4
AJ
Curtain Bar Bracket
2
AK
M8 x 14 Cap Screw
2
Tools Required
AL
4 mm T-handle hex driver
AM
6mm hex key
3.10.2. Attaching the Curtain Bar
52. Assemble fasteners to qty 2 Curtain Bar Brackets (AJ):
Figure 48 Fitting Fasteners to the Curtain Bar Brackets
Summary of Contents for LFE1220-EU
Page 60: ...www thorlabs com ...